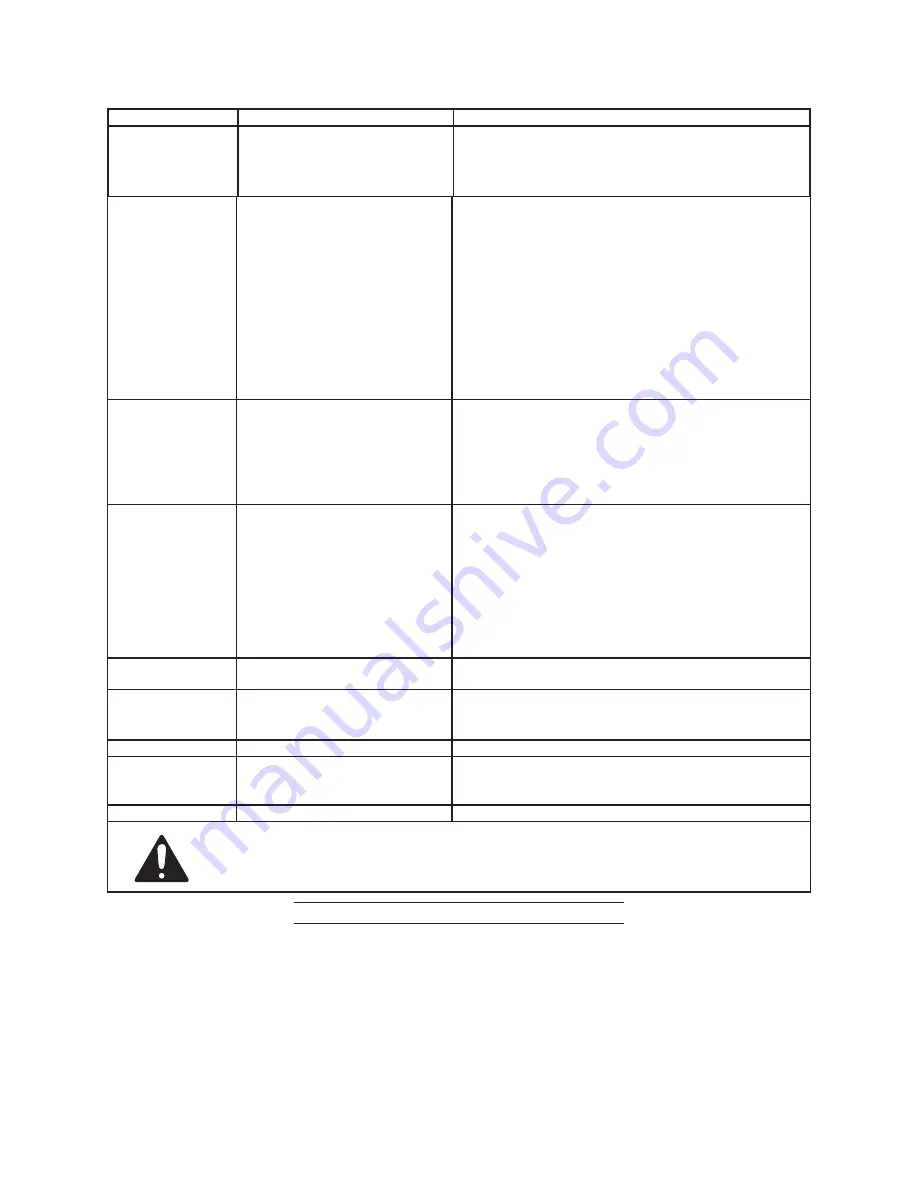
Page 17
For technical questions, please call 1-800-444-3353.
SKU 68064
Problem
Possible Causes
Likely Solutions
High Oil
Consumption
1. Crankcase oil too thin.
2. Unit not on level surface.
3. Crankcase vents clogged.
1. Drain oil and refill to proper level with recommended
oil.
2. Reposition unit on a level surface.
3. Clean Crankcase vents.
Overheating
1. Filters need cleaning/replacing.
2. Crankcase oil too thin or
incorrect type.
3. Crankcase oil level too low.
4. Unusually dusty environment.
5. Cord is too small of a gauge or
too long to handle compressor.
6. Unit not on level surface.
1. Check inlet and outlet filters. Clean and/or replace as
needed.
2. Drain oil and refill to proper level with recommended
oil.
3. Add oil to proper level, check for leaks.
4. Clean and/or replace filters more often or move unit to
cleaner environment.
5. Increase cord size or use shorter length extension
cord, or eliminate extension cord. See Recommended
Wire Gauge for Extension Cords in Safety section.
6. Reposition unit on a level surface.
Compressor
starts and stops
excessively
1. Compressor not large enough
for job.
2. Loose fittings.
1. Check if accessory SCFM is met by Compressor. If
Compressor doesn’t reach accessory SCFM, you need
a larger Compressor.
2. Reduce air pressure, then check all fittings with a soap
solution for air leaks and tighten as needed. Do not
overtighten.
Excessive noise
1. Crankcase overfilled with oil
or oil is incorrect thickness or
type.
2. Crankcase oil level too low.
3. Loose or damaged belt guard.
4. Loose fittings.
5. Unit not on level surface.
1. Drain oil and refill to proper level with recommended
oil.
2. Add oil to proper level, check for leaks.
3. Replace belt guard.
4. Reduce air pressure, then check all fittings with a soap
solution for air leaks and tighten as needed. Do not
overtighten.
5. Reposition unit on a level surface.
Moisture in
discharge air
Too much moisture in air.
Install inline air filter/dryer, and/or relocate to less humid
environment.
Oil in discharge air 1. Crankcase oil too thin or
crankcase overfilled with oil.
2. Crankcase vents clogged.
1. Drain oil and refill to proper level with recommended
oil.
2. Clean Crankcase vents.
Safety Valve “pops” Safety valve needs service.
Pull on test ring of safety valve. If it still pops, replace.
Air leaks from pump
or fittings
Loose fittings.
Reduce air pressure, then check all fittings with a soap
solution for air leaks and tighten as needed. Do not
overtighten.
Air leaks from tank Defective or rusted tank.
Have tank replaced by a qualified technician.
Follow all safety precautions whenever diagnosing or servicing the
compressor. Disconnect power supply before service.
PLEASE READ THE FOLLOWING CAREFULLY
THE MANUFACTURER AND/OR DISTRIBUTOR HAS PROVIDED THE PARTS LIST AND ASSEMBLY DIAGRAM IN
THIS MANUAL AS A REFERENCE TOOL ONLY. NEITHER THE MANUFACTURER OR DISTRIBUTOR MAKES ANY
REPRESENTATION OR WARRANTY OF ANY KIND TO THE BUYER THAT HE OR SHE IS QUALIFIED TO MAKE ANY
REPAIRS TO THE PRODUCT, OR THAT HE OR SHE IS QUALIFIED TO REPLACE ANY PARTS OF THE PRODUCT.
IN FACT, THE MANUFACTURER AND/OR DISTRIBUTOR EXPRESSLY STATES THAT ALL REPAIRS AND PARTS
REPLACEMENTS SHOULD BE UNDERTAKEN BY CERTIFIED AND LICENSED TECHNICIANS, AND NOT BY THE
BUYER. THE BUYER ASSUMES ALL RISK AND LIABILITY ARISING OUT OF HIS OR HER REPAIRS TO THE
ORIGINAL PRODUCT OR REPLACEMENT PARTS THERETO, OR ARISING OUT OF HIS OR HER INSTALLATION
OF REPLACEMENT PARTS THERETO.