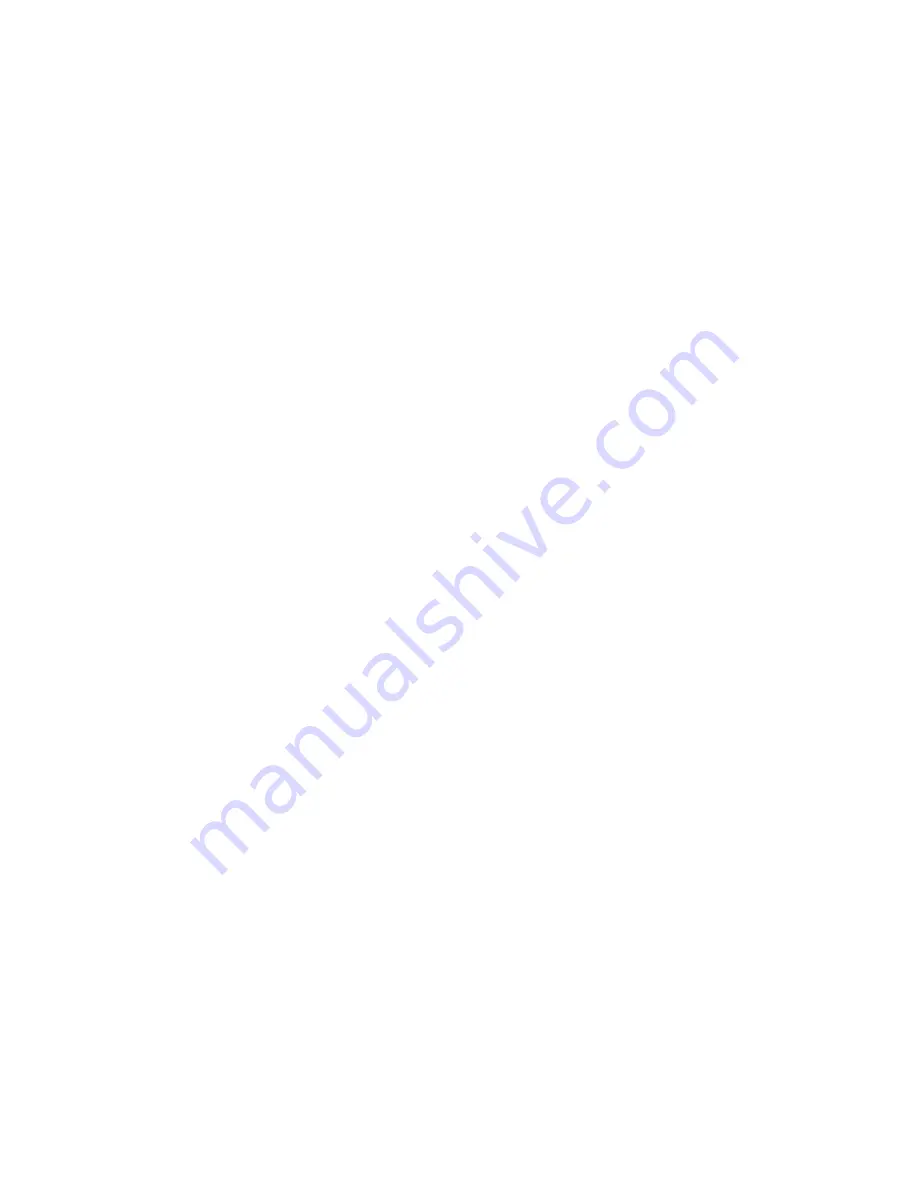
Transformer
(
See Fig. 12.0
)
The Transformer includes its own, internal thermal
fuse on the primary. If this has gone open circuit the
cause should be established before replacing the
Transformer.
Disconnect from the terminal strip and fuse
holder.
Undo the two screws holding it to the chassis and
replace.
Pool Thermostat
(
See Fig. 12.0
)
Pull off the Pool Thermostat Knob.
Release the Rear Retainer by undoing the Wing
Nut.
Pull off all the PCB connectors.
Slide out the Thermostat.
Replacement is the reverse.
Condensate Pressure Switch
(See
Fig. 12.0
)
Undo the single fixing screw.
Pull off the two electrical connectors and transfer
to the new Switch. They connect to the ‘C’ and
‘NO’ connections.
Replacement is the reverse
Heater Components
The remainder of the parts can be accessed
through the front.
Pool Temperature Sensor &
Heat Exchanger Flow Sensor
These are located on the connections to the Heat
Exchanger and are the same items. (
See Fig.13.4
)
Unclip the sensor from the connections.
Transfer the push on electrical connectors to the
replacement and clip back on.
Water Pressure Switch
This is located on the Inlet connection to the Heat
Exchanger and its removal will require the draining
of the Heater. (
See Fig.13.4
)
Pull off the Electrical Connectors
Unscrew from the Heat Exchanger connections.
Replacement is the reverse.
If the Water Pressure Switch needs adjustment See
Page 12 for details.
IMPORTANT. It is essential that all the air is
removed from the Heat Exchanger before the
Heater is fired. Running the Heater with air still in
it will damage the Heat Exchanger and invalidate
the warranty.
Control Thermostat
This is located on the Outlet connection of the Heat
Exchanger. (
See Fig.13.4
)
Unclip the sensor from the connection.
Transfer the push on electrical connectors to the
replacement and clip back on.
Condensing Pool Heater
24
14/11/06
Heat Exchanger Combustion
Temperature Sensor
This is located on the top of the Heat Exchanger, on
the right hand side. (
See Fig.13.1
)
Release the electrical connector by pressing the
latch and pulling up.
Twist the Sensor a quarter turn clockwise and
withdraw.
IMPORTANT
Ensure the O ring seal is fitted correctly
to the replacement before fitting.
Replacement is the reverse.
Flue Thermostat
This is located on the Flue Adapter. (
See Fig.13.1
).
Pull off the electrical connectors.
Slide out from under the clip.
Replacement is the reverse.
Ignition Control
(
See Fig.13.3
)
Undo the single screw holding the Ignition Control.
Release the two electrical connectors by pressing
the latch and pulling apart.
Pull the Ignition Control away from the Gas Valve.
Replacement is the reverse.
Gas Valve
(
See Fig.13.3
)
Remove the Ignition Control, see above.
Release the Gascock by undoing the four shoulder
bolts holding it to the Gas Valve.
Remove the Offset tube from the Gas Valve and
unscrew the Offset Connector and transfer to the
new Gas Valve.
Release the Gas Valve from the Venturi by
undoing three screws. (
See Fig.13.3
)
IMPORTANT
Ensure the rubber seal (and orifice if
Propane) is transfered from the old Valve and placed
between the Venturi and Gas Valve before assembly.
Replacement is the reverse.
Fire the Heater and check for gas leaks.
After five minutes check the rate and combustion
is correct to the Datatable. (inside cover). Adjust
using the throttle on the Gas Valve,
(See Fig. 13.3)
.
Fan
(
See Fig.13.2
)
Remove the two electrical connectors on the Fan.
See (
See Fig.13.2
)
Remove the two screws holding the Venturi to the
Fan.
Undo the four nuts holding the Fan to the Heat
Exchanger and withdraw. (
See Fig.13.2
)
Transfer the Venturi gasket to the new fan.
Replacement is the reverse.