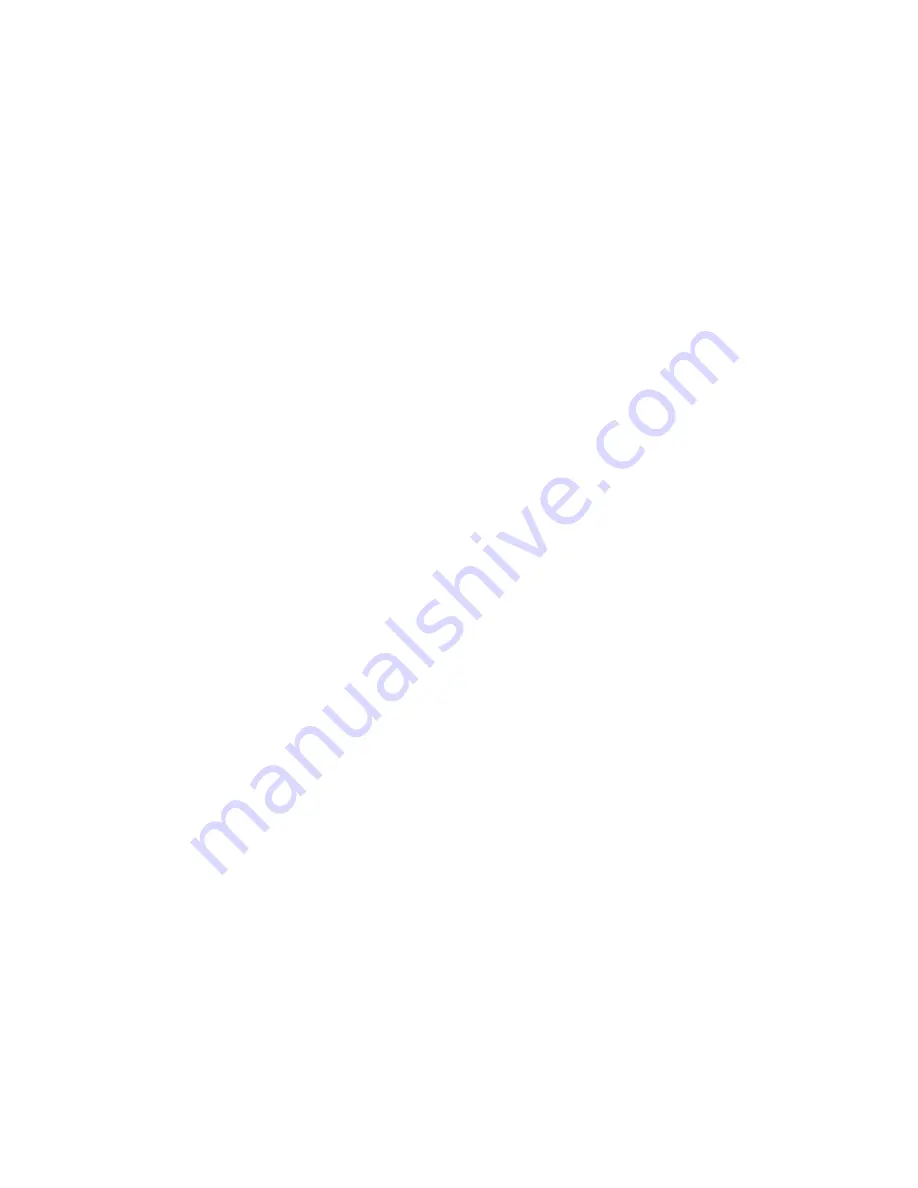
Cessna 170 Service Manual
Electrical System
12
170. Subsequent regulations increased candlepower requirements of aircraft lighting systems and aircraft
designed to meet those regulations specify the No. 7512-12 lamp which is a 12/14 volt, 26 watt lamp of
increased candlepower. Either may be used in the 170, however the 7512-12 lamps will provide brighter
light with only minimal increase (.66A) in load of the existing system.
The rudder navigation lamp was originally Cessna PN 0433006-3, which has been superceded to a common
GE-93. This is a 12/14-volt, 15 candlepower lamp.
PITOT AND STALL WARNING HEATER CIRCUITS
. All models 170 are capable of being provided a pitot
heater and stall warning heater system. The system originally designed for the aircraft is a Kollsman heated
pitot unit in accordance with Cessna Dwg. 0511051. This is a straight pitot similar to that used on C-
190/195 series aircraft. Some aircraft have been modified with “L”-type units of the AN-5812 types found on
later series Cessna aircraft. The electrical circuits for both systems are identical. Power is supplied via a
current limiter and a switch usually located on the instrument panel, to the heater elements contained within
the pitot tube and within the lift detector assembly. Each heater element draws approximately 5 amperes.
Both heated pitot types and lift detector assembly units heaters are field replaceable ceramic units
containing resistance wire. The only indication of failure of the heating element is loss of heat at the unit
itself coupled with a slightly lower amperage indication on the ammeter. This drop in electrical requirement
is only slightly observable. In rare instances fracturing of the heating units ceramic body may cause current
limiter activation (blown fuse/activated circuit breaker.) Pre-flight testing of the systems is imperative when
freezing precipitation is anticipated in flight. The system is tested during pre-flight by turning the Master
switch ON, turning the pitot/static system heat switch ON for 30 seconds, and feeling the units by hand for
generated heat. This test period must be kept to a short duration to avoid overheating the units on the
ground. Caution: The pitot/static heaters are capable of extremely high temperatures. Caution must be
taken to avoid serious burns and overheating of the units which will cause damage. Avoid static testing of
the units for periods exceeding 2 minutes.
REMOVAL AND REPLACEMENT OF PITOT/STATIC HEATERS
. The pitot tube has a nose-cone that is
removable by unscrewing it from the main body, exposing the ceramic heating unit surrounding the inner
pitot tube. Remove the local inspection cover and disconnect the wiring terminals from the harness. Slide
the heater unit from the pitot tube. Installation of the replacement unit is the reverse procedure.
The stall warning lift detector heating unit is removed by first removing the lift detector from the leading edge
of the wing. First note the relative position of the lift detector on the leading edge of the wing so as to avoid
the necessity of flight-testing the aircraft to correct an altered stall warning speed. A grease pencil may be
handy to mark the position of the lift detector prior to removal. Remove the local inspection cover and the
four PK screws mounting the lift detector to the wing. Locate the tubular, ceramic heater element held by a
small clamp inside the lift detector assembly, and remove it by loosening the clamp. This will require only a
screwdriver and a 5/16” wrench or socket. Remove the two heater wire leads from the harness terminals.
There is no polarity preference of this harness. Installation of the replacement heater element unit is the
reverse procedure.
Caution: Some pitot systems utilize poly tubing to carry air pressure to the cockpit instrumentation. Be
certain not to allow any resistance wiring to come into contact with the poly tubing or the tubing may melt
giving erroneous airspeed indications to the pilot. Use only the correct wiring terminal ends and isolate any
poly tubing from wiring.
STALL WARNING SYSTEM
. All models 170 were capable of having a stall warning system installed in
accordance with Cessna Dwg. 0511062. It is required equipment on the 170 B-model. The system consists
of a current limiter (shared with the turn-and-bank indicator) a warning horn/lamp unit located on the
instrument panel, a lift detector located on the left wing leading edge, and associated wiring. Electrical
power (12/14 volts DC) is supplied to the warning horn/light via the current limiter (fuse/circuit breaker)
whenever the Master Switch is ON. After the voltage passes through the warning unit it finds it’s ground out
on the wing, by passing first through the Lift Detector switch (operated by relative wind against the lift
detector vane on the leading edge) then to a nearby ground through a short wire terminating at a screw in
the airframe, thereby completing the circuit. When the lift detector completes the circuit, the warning horn
sounds and the indicator lamp illuminates. The lamp bulb is a GE-1816, 12/14volt .33 amp,
T-3 ¼ miniature bayonet.
The lift detector position on the leading edge of the wing is adjustable and should be adjusted to give
approximately 5 M.P.H. warning above a stall in level flight.
Summary of Contents for 170
Page 3: ...Cessna 170 Service Manual Electrical System ELECTRICAL ...
Page 25: ...Cessna 170 Service Manual Electrical System ELECTRICAL SCHEMATIC SNs 20267 THRU 25372 ...
Page 26: ...Cessna 170 Service Manual Electrical System ELECTRICAL SCHEMATIC SNs 25373 THRU 26995 ...
Page 27: ...Cessna 170 Service Manual Electrical System ELECTRICAL SCHEMATIC SNs 26996 AND ON ...
Page 29: ...Cessna 170 Manual Electrical System ...
Page 30: ...Cessna 170 Manual Electrical System ...
Page 31: ...Cessna 170 Manual Electrical System ...
Page 32: ...Cessna 170 Manual Electrical System ...
Page 33: ...Cessna 170 Service Manual Electrical System ...
Page 34: ...Cessna 170 Service Manual Electrical System ...
Page 42: ......