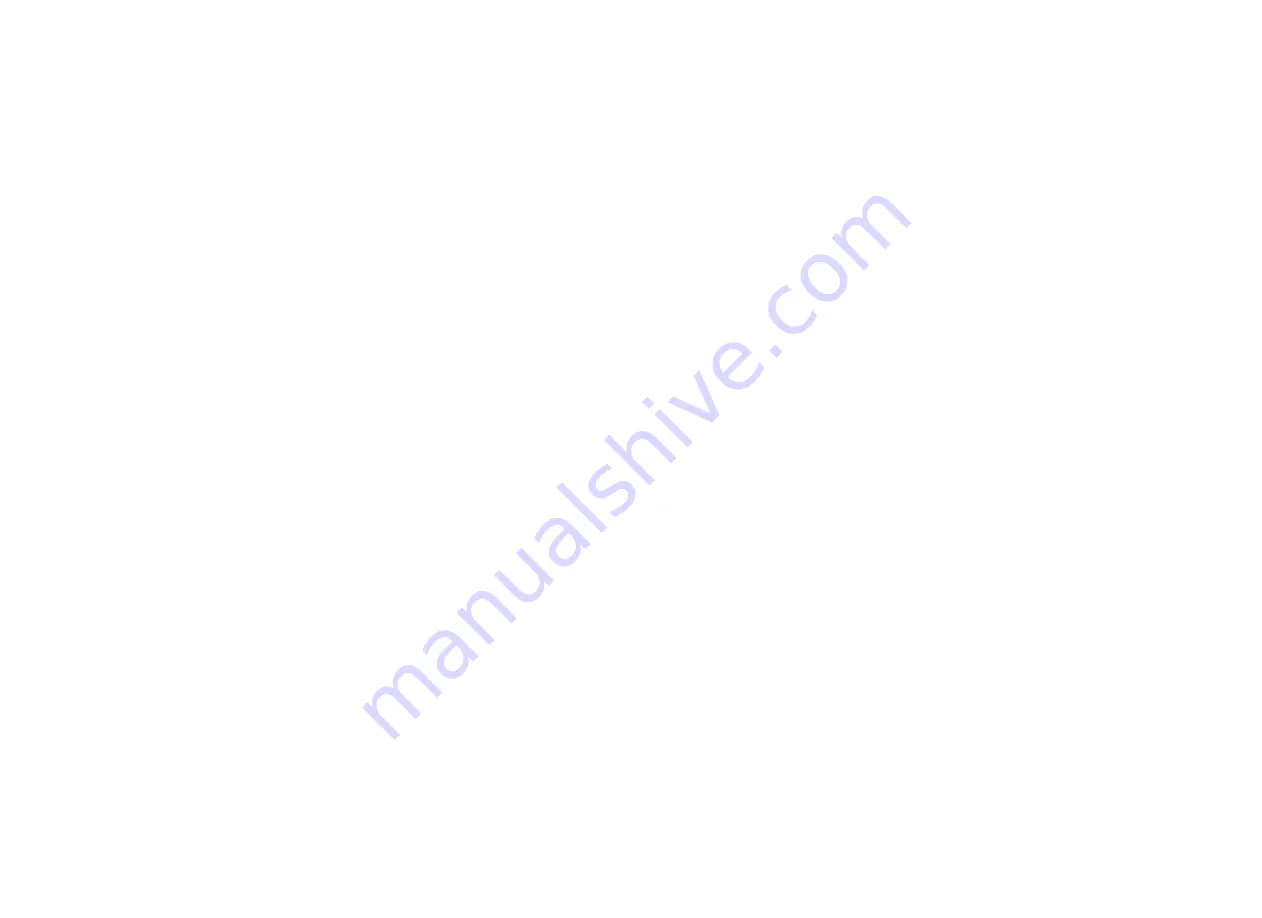
SECTION 7
CESSNA
AIRPLANE & SYSTEMS DESCRIPTIONS
MODEL 172RG
The fuel pressure gage, located on the upper left side of the instrument
panel, indicates fuel pressure to the carburetor. Gage markings indicate
that minimum pressure is 0.5 PSI (red line), normal operating range is 0.5
to 8 PSI (green arc), and maximum pressure is 8 PSI (red line).
An economy mixture (EGT) indicator is available for the airplane and
is located on the right side of the instrument panel. A thermocouple probe
in the right exhaust stack assembly measures exhaust gas temperature
and transmits it to the indicator. The indicator serves as a visual aid to the
pilot in adjusting the mixture during climb or cruise as described in
Section 4. Exhaust gas temperature varies with fuel-to-air ratio, power,
and RPM. However, the difference between the peak EGT and the EGT at
the desired mixture setting is essentially constant and this provides a
useful leaning aid. The indicator is equipped with a manually positioned
reference pointer which is especially useful for leaning during climb.
A carburetor air temperature gage is available for the airplane. Details
of this gage are presented in Section 9, Supplements.
NEW ENGINE BREAK-IN AND OPERATION
The engine underwent a run-in at the factory and is ready for the full
range of use. It is, however, suggested that cruising be accomplished at a
minimum of 75% power until a total of 25 hours has accumulated or oil
consumption has stabilized. This will ensure proper seating of the rings.
ENGINE OIL SYSTEM
Oil for engine lubrication and propeller governor operation is supp-
lied from a sump on the bottom of the engine. The capacity of the engine
sump is 8 quarts (one additional quart is required for the full flow oil filter).
OH is drawn from the sump through an oil suction strainer screen into the
engine-driven oil pump. From the pump, oil is routed to a bypass valve. If
the oil is cold, the bypass valve allows the oil to bypass the oil cooler and go
directly from the pump to the full flow oil filter. If the oil is hot, the bypass
valve routes the oil out of the accessory housing and into a flexible hose
leading to the oil cooler on the upper right side of the engine. Pressure oil
from the cooler returns to the accessory housing where it passes through
the oil filter. The filtered oil then enters a pressure relief valve which
regulates engine oil pressure by allowing excessive oil to return to the
sump while the balance of the oil is circulated to various engine parts for
lubrication. Residual oil is returned to the sump by gravity flow.
An oil filler cap/ oil dipstick is located at the rear of the engine on the
7-20
1 July 1979
CESSNA
SECTION 7
MODEL 172RG
AIRPLANE & SYSTEMS DESCRIPTIONS
right side. The filler cap/ dipstick is accessible through an access door in
the engine cowling. The engine should not be operated on less the five
quarts of oil. To minimize loss of oil through the breather, fill to seven
quarts for normal flights of less than three hours. For extended flight, fill
to eight quarts (dipstick indication only). For engine oil grade and
specifications, refer to Section 8 of this handbook.
An oil quick-drain valve is installed on the bottom of the oil sump, to
provide a quick, clean method of draining the engine oil. To drain the oil,
slip a hose over the end of the valve and push upward on the end of the valve
until it snaps into the open position. Spring clips will hold the valve open.
After draining, use a suitable tool to snap the valve into the extended
(closed) position and remove the drain hose.
Whenever the oil is drained from the sump, it must also be drained from
the oil cooler. This is accomplished by removing the cap at the tee fitting on
the oil cooler. Refer to the Service Manual for the correct procedure for
refilling the sump to prevent an air lock in the oil cooler.
I GNITION-STARTER SYSTEM
Engine ignition is provided by two engine-driven magnetos, and two
spark plugs in each cylinder. The right magneto fires the lower right and
upper left spark plugs, and the left magneto fires the lower left and upper
right spark plugs. Normal operation is conducted with both magnetos due
to the more complete burning of the fuel-air mixture with dual ignition.
Ignition and starter operation is controlled by a rotary type switch
located on the left switch and control panel. The switch is labeled clock-
wise, OFF, R, L, BOTH, and START. The engine should be operated on both
magnetos (BOTH position) except for magneto checks. The R and L
positions are for checking purposes and emergency use only. When the
switch is rotated to the spring-loaded START position (with the master
switch in the ON position), the starter contactor is energized and the
starter will crank the engine. When the switch is released, it will automati-
cally return to the BOTH position.
AIR INDUCTION SYSTEM
Ram air for the engine induction system is received through the left
opening in the nosecap. An induction system airscoop is located in the aft
vertical baffle just behind the engine on the left side. This scoop is covered
by an air filter which removes dust and other foreign matter from the
1 July 1979
7-21