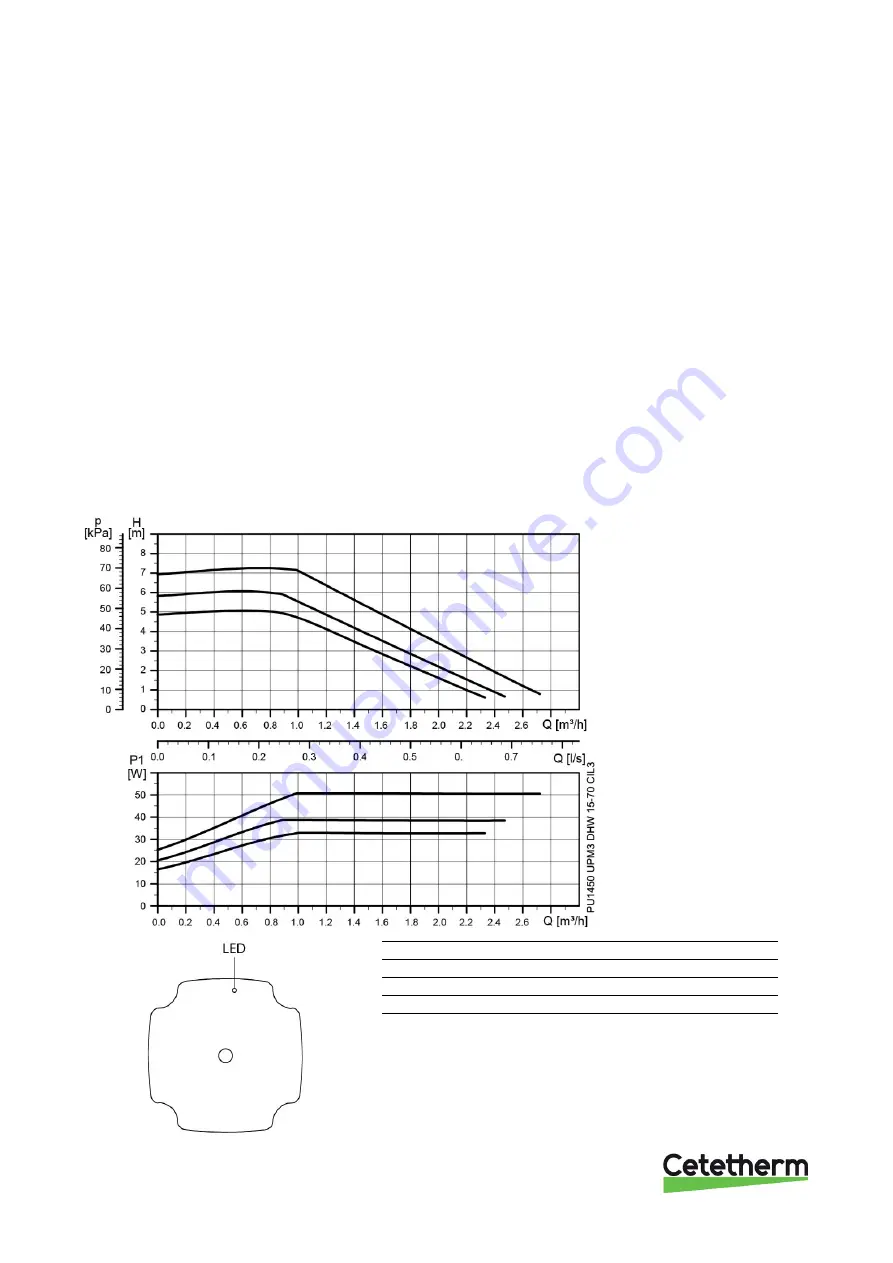
Cetetherm Midi Wall TA
Installation, service and operating instruction
12
5 Electrical installation
5.1 General
The wiring in Midi Wall conforms to the applicable rules for CE marking and has undergone electrical safety
testing and function testing. For permanent installation must the substation be connected to an all-pole isolated
switch. This must be done by a duly qualified electrician.
The substation must be connected to a grounded power outlet.
6 Pump settings and capacity
6.1 General
Mini Wall is equipped with two circulation pumps, one for the hot water circulation, DHWC-pump, and one for
the heating circuit.
The DHWC pump is a speed-controlled, high-efficiency pump.
The circulation pump for heating circuit is a pressure-controlled pump. The pump for heating circuit is available
in two different models.
6.2 DHWC pump Grundfos UPM3 DHW 15–70 CIL3, capacity
Picture 7
Picture 8
Green LED
Red LED
No external control
●
External control
●
1
Alarm
●
1)
12 flashes per second
.