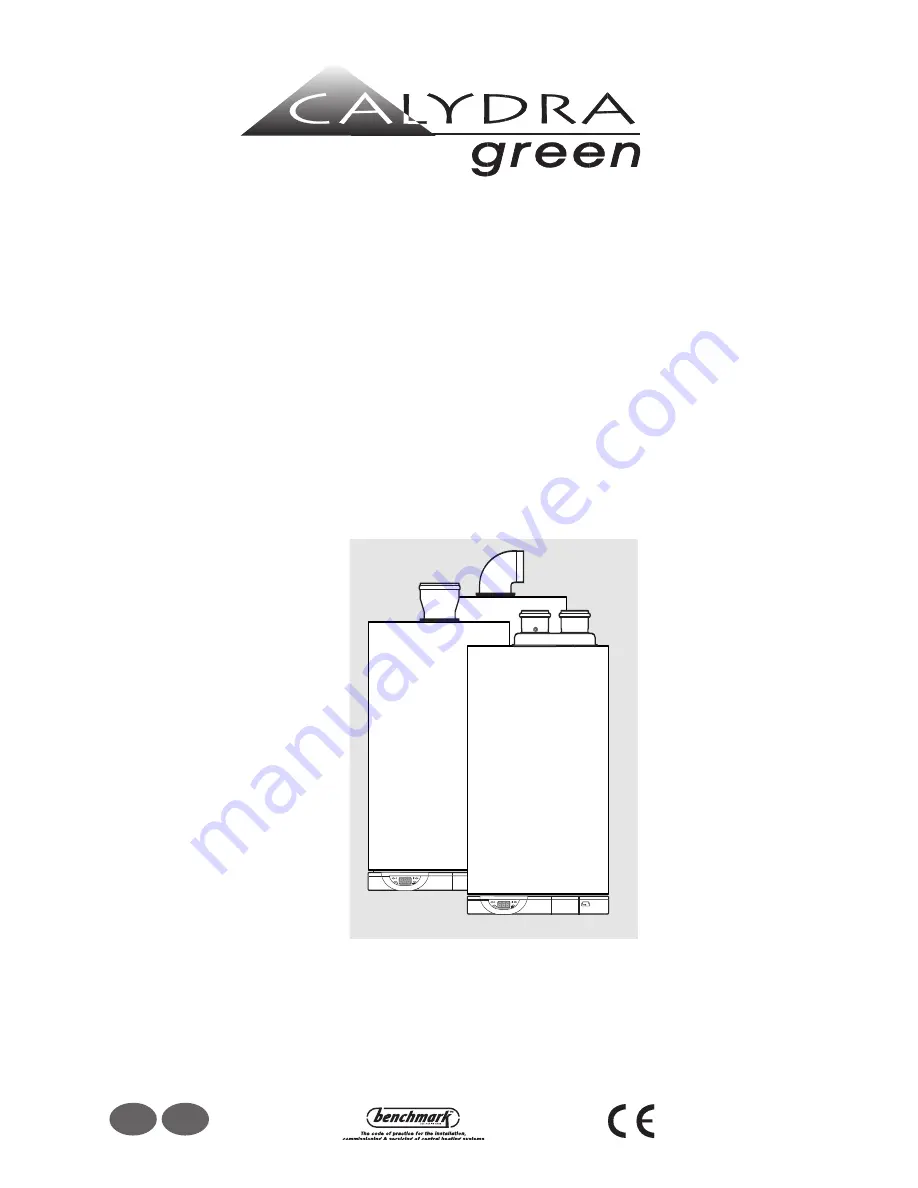
CONDENSING WALL HUNG COMBINATION BOILER
Heating and Instantaneous Domestic Hot Water with TSS®
Fanned Flue System
Installation and Operating
Instructions
Calydra green 24
Calydra green 30
c
Manufactures N°
Model Type
Gas Council N°
200906823037.31
Calydra green 24 Nat
47-980-25
200906826037.31
Calydra green 30 Nat
47-980-26
GB
IE
Summary of Contents for Calydra green 24
Page 9: ...9 5 A Fig 11 A A A Fig 9 Fig 10 L Fig 8 Fig 12 Installing the Boiler continued ...
Page 23: ...23 ...
Page 58: ...18 ...