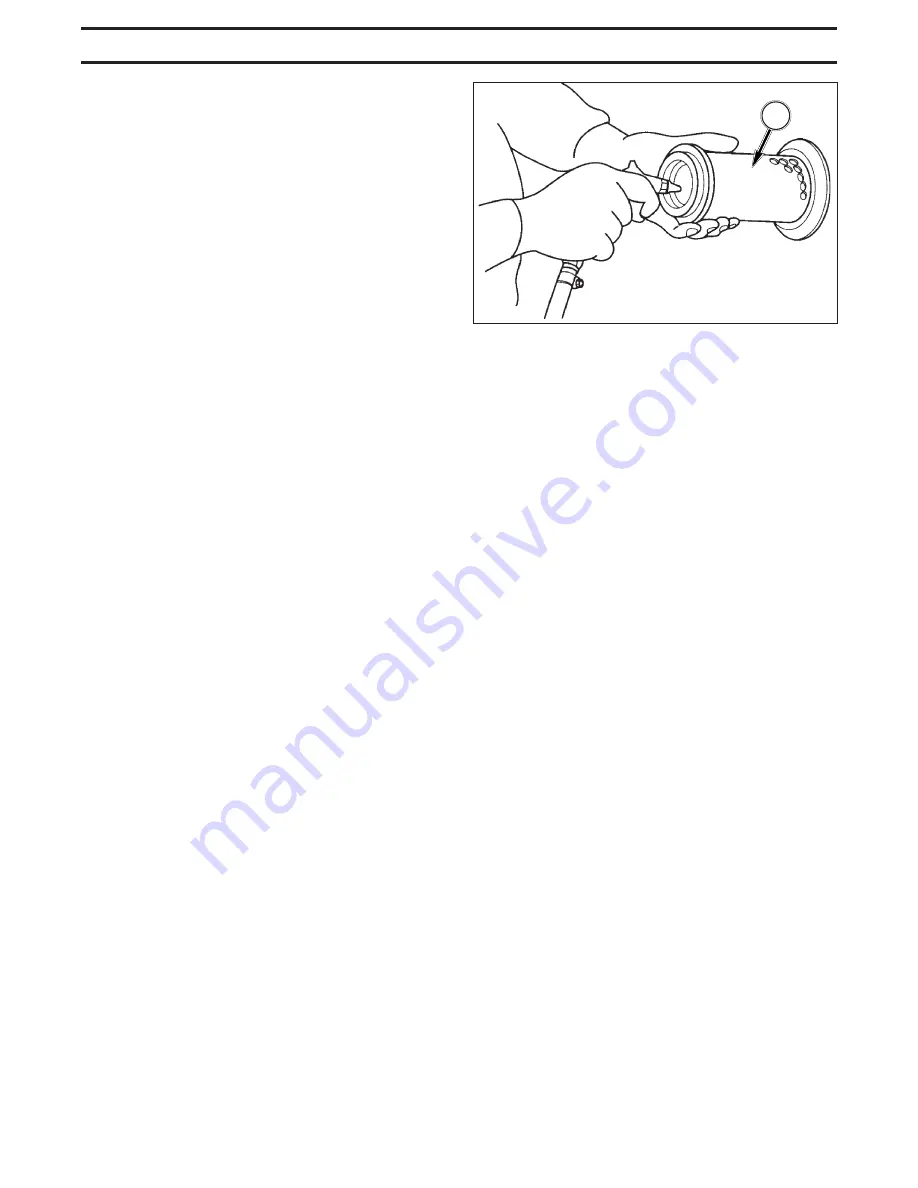
B6 - ENGINE
79019435B
FIG. 14
I-3125
4
FIG. 14: Air Filter element, 4, may be cleaned (if in
serviceable condition) using following procedures:
1.
Using compressed air not to exceed 30 psi (200 kPa)
from inside element, remove loose dirt, grass, chaff,
etc. Be careful not to damage element pleats with air
flow.
2.
If outer element is coated with oil or soot:
a.
Prepare solution of warm water and non-foaming
detergent.
b.
Soak element for thirty minutes.
c.
Agitate element in solution until oil and soot are
loosened.
d.
Rinse element until rinse water is clear.
e.
Allow element to completely dry. Do not dry by
using compressed air or heat.
f.
After cleaning (or washing) element examine for
pin holes, punctures, or tears. If element paper,
canister or seal show any signs of physical
damage, element must be replaced.
NOTE: Replace element which has already been washed
five times.