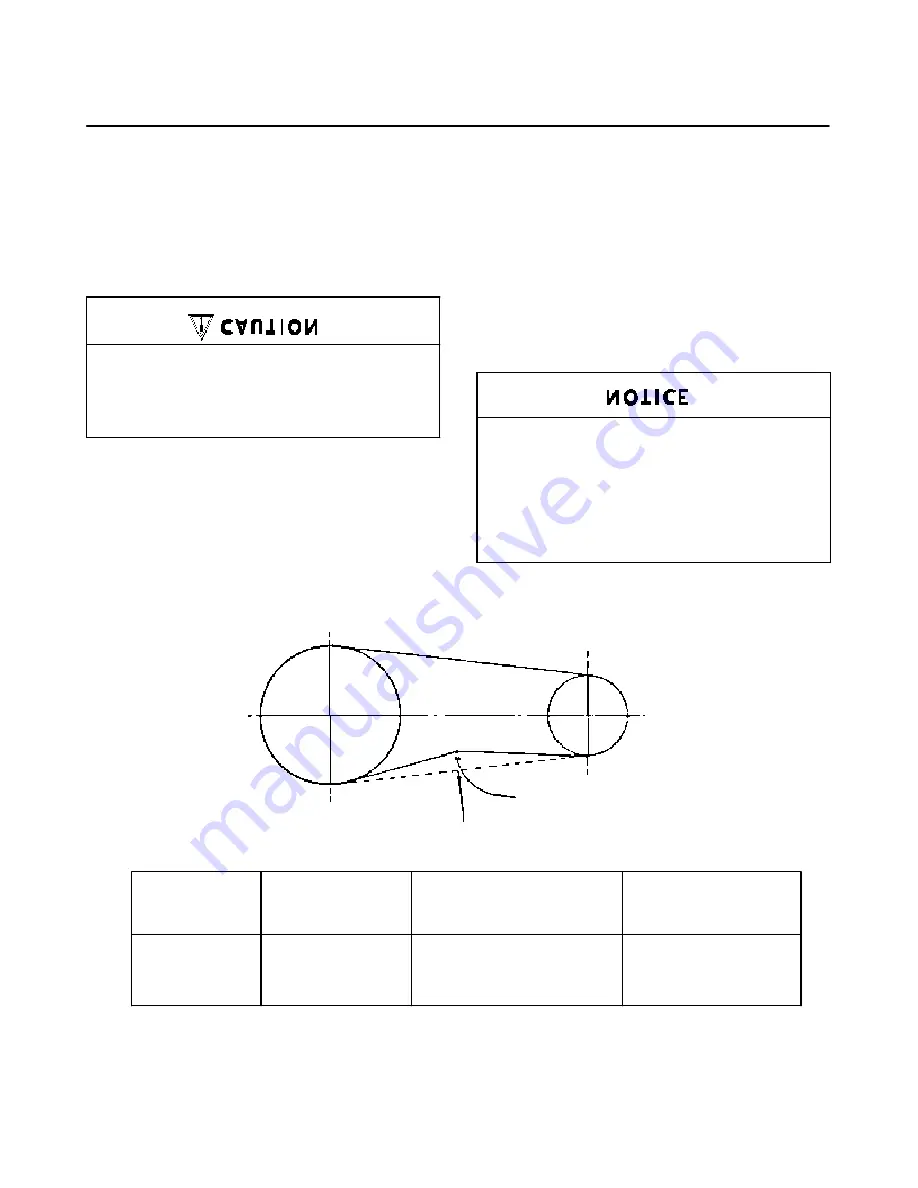
13- 11- 605
Page 44
SECTION 7
BELT DRIVE
Proper drive belt tension and alignment are provided at
the factory, however, good practice dictates checking
the drive alignment and tension after shipment and be-
fore initial start-- up.
Sheaves should align straight across the front with a
straight edge. The best tension is just enough tension
to keep belts from “squealing” on start-- up.
Excessive belt tension can damage
the equipment. Tension the belts as
shown in FIGURE 7--1.
Belts can be changed when necessary by the following
instructions. First, disconnect, tag and lockout power
to the starter. Then remove the belt guard. Then loos-
en, but do not remove, the four motor foot nuts.
Next, use the adjusting screws in the motor base to
loosen belt tension. Remove the belts, and replace with
new belts. Check for correct belt tension and sheave
alignment, tighten the motor foots bolts, and re-- attach
the wire guard.
CHECKING BELT TENSION
-- Using a spring scale,
apply a perpendicular force to each belt at the midpoint
of the span and measure the deflection. Correct deflec-
tion force and deflection are shown in FIGURE 7-- 1. To
tighten belts, merely increase the center distance be-
tween the sheaves.
When a new set of belts is installed on
a drive, the initial deflection force
should be 1/3 times greater than
shown in FIGURE 7--1. Recheck ten-
sion frequently during the first 24
hours of operation.
No.
Deflection
Deflection
Motor
Of
Force Pounds (Newtons)
In
H.P. (KW)
Belts
(per belt)
Inches (mm)
20 (15 KW)
4
6 to 7 (1.3 to 1.5)
5/16 (8)
25 (19 KW)
4
6 to 8.5 (1.3 to 1.9)
5/16 (8)
30 (22 KW)
4
6 to 7 (1.3 to 1.5)
5/16 (8)
FIGURE 7--1 -- BELT TENSION 3VX BELTS
DEFLECTION FORCE (LBS) (N)
DEFLECTION (INCHES) (mm)
Summary of Contents for ROTORCHAMP RCOF20
Page 13: ...13 11 605 Page 4 FIGURE 1 6 AIR WATER SCHEMATIC 300EWC797 B Ref Drawing ...
Page 16: ...13 11 605 Page 7 DECALS 206EAQ077 300EWC077 301EWC077 211EAQ077 207EAQ077 ...
Page 17: ...13 11 605 Page 8 DECALS 216EAQ077 206EWD077 222EAQ077 221EAQ077 208EAQ077 ...
Page 31: ...13 11 605 Page 22 FIGURE 4 2 FLOW CHART FOR SET UP PROGRAMMING 300EWC1255 Ref Drawing ...
Page 41: ...13 11 605 Page 32 FIGURE 4 6 CONTROL TUBING SCHEMATIC 300EWC797 B Ref Drawing ...
Page 45: ...13 11 605 Page 36 FIGURE 4 10 WIRING DIAGRAM FULL VOLTAGE 301EWC546 A Ref Drawing ...
Page 46: ...13 11 605 Page 37 FIGURE 4 11 WIRING DIAGRAM WYE DELTA 302EWC546 A Ref Drawing ...
Page 47: ...13 11 605 Page 38 FIGURE 4 12 AUTO SENTRY W CONTROLLER DISPLAY ...
Page 49: ...13 11 605 Page 40 FIGURE 5 1 OIL LEVEL SIGHT GLASS 306EWC797 A Ref Drawing ...
Page 50: ...13 11 605 Page 41 FIGURE 5 2 FLOW DIAGRAM AIR COOLED 300EWC797 A Ref Drawing ...