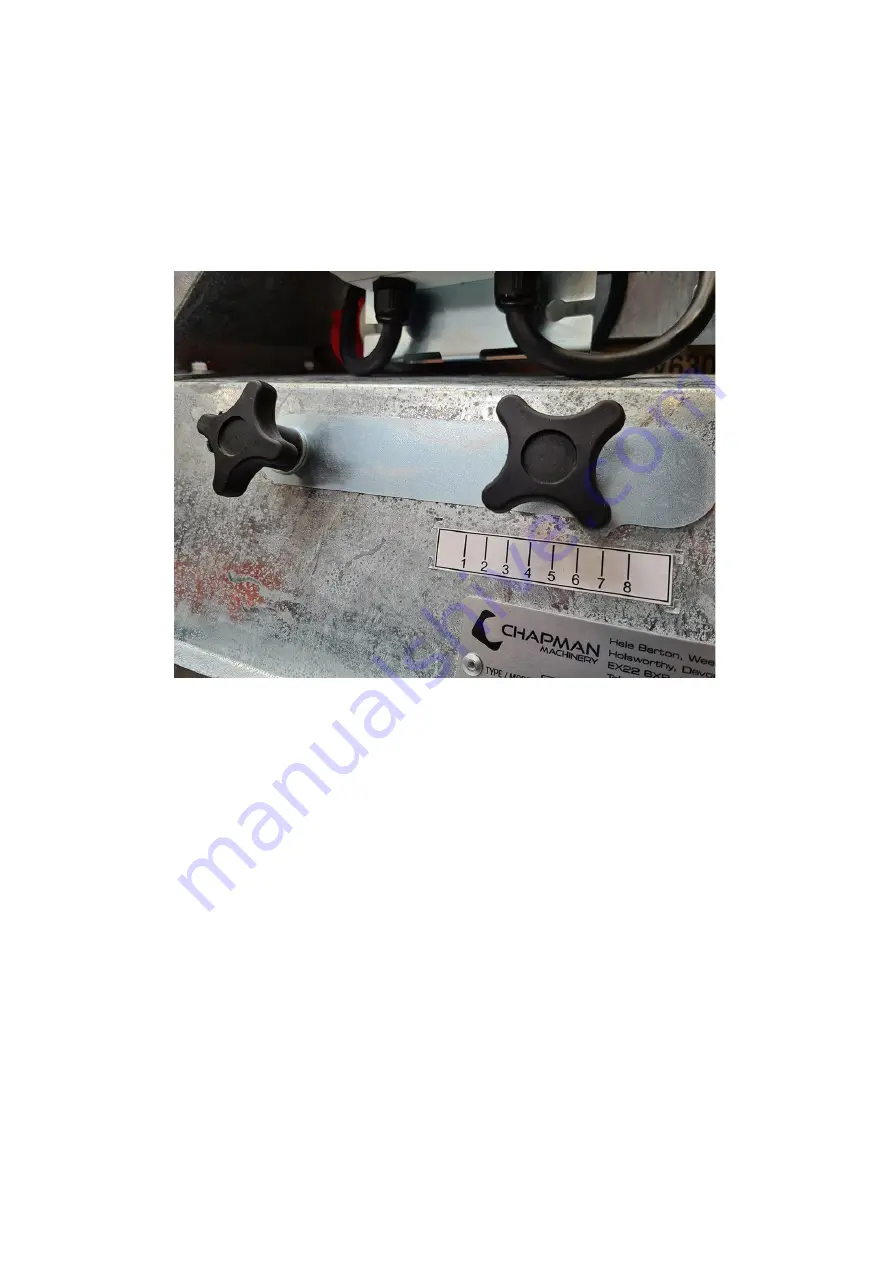
Page 9
Initial Calibration
On the RH Side at the rear of the machine you will find two black handwheels and an indicator plate as
shown below. Initially set the Feed adjustment plate to setting 2, as indicated by the arrow on the drop
adjustment plate. To adjust, loosen BOTH hand wheels, and slide the unit forwards or backwards to the
desired value. Tighten securely.
Setting 1: Minimum drop size
Setting 8: Maximum drop size
Fill the hopper 50% full of the feed to be distributed. Close the two deflector plates at the side of the
spinner and use a 25kg feedbag or similar so that the feed out the back of the spinner can be collected or
weighed. With the machine securely attached to the fitted vehicle and on level ground, run the feeder for
1 minute, Measure the weight of the deposited feed
–
this is the amount of feed deposited per minute.
Adjust the feed adjustment plate as required to increase or decrease the feedrate.
The feed rate setting will differ between different feed, due to the different particulate size. It is strongly
recommended to re-calibrate if you change feed make-up or consistency.
Once you have set the machine to the desired feed rate, securely tighten the two retaining
handwheels to ensure this does not change during use. Once happy with the feedrate is advisable to
make a mark in indelible ink on the machine so that the rate can be easily recalled if needed.