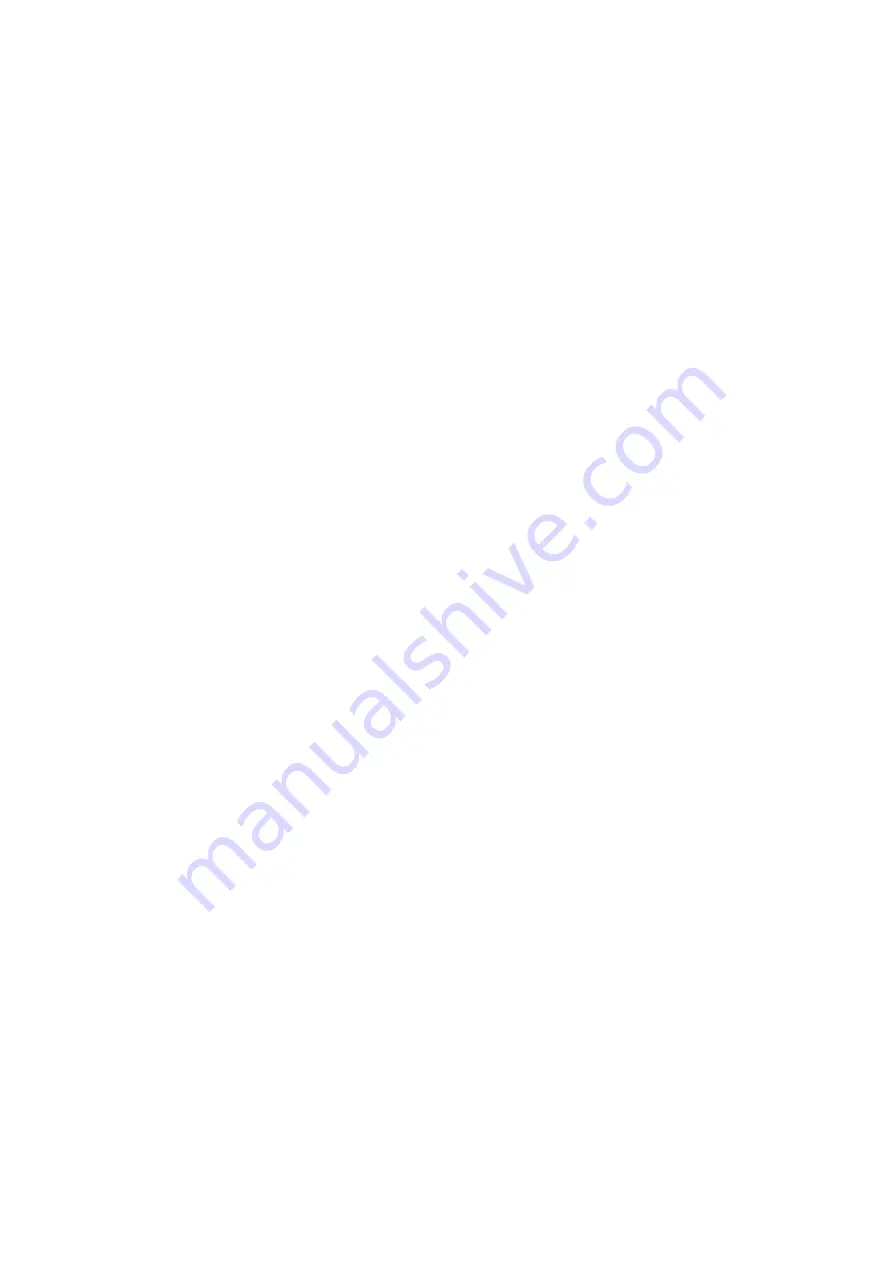
Page 14
Maintenance
All maintenance, cleaning and repair operations must be performed with the machine suitably supported, the engine
switched off (and cool), and the ignition keys removed.
NOTE: For commercial use, log hours of operation in a maintenance booklet to ensure proper maintenance
intervals and continued service.
Maintenance Schedule
After first 1 hours of work
•
Check all nuts and bolt for tightness
–
retighten if required.
•
Check belt tension and taper lock tightness
–
adjust / tighten if required
Every 8 hours or daily
CHECK
•
Check all nuts and bolt for tightness
–
retighten if required.
•
Check belt condition and replace if necessary
•
Check wear and condition of brushes
•
Check operation of emergency stop control
LUBRICATE
•
Lubricate main rotor bearings
–
apply 20 shots of grease to each main rotor bearing
After every 100 hours (or annually, whichever occurs first), in addition to the above
CHECK
•
Check belt condition - replace if required
•
Check axle bearing condition - replace or lubricate as required
•
Check main rotor bearings condition - replace as required
•
Check condition of battery & connections
•
Check condition of brushes and tines and replace as required
•
Check condition of battery cables - replace if damaged
•
Grease height adjustment mechanism
–
apply 20 shots of grease
Machine Disposal
Disposal of this machine and any of its component parts must be performed in a responsible and inoffensive
manner respecting all current laws relating to this subject. Materials forming this machine that must undergo
differentiated division and disposal are:
•
Steel
•
Mineral Oil
•
Rubber
•
Plastic