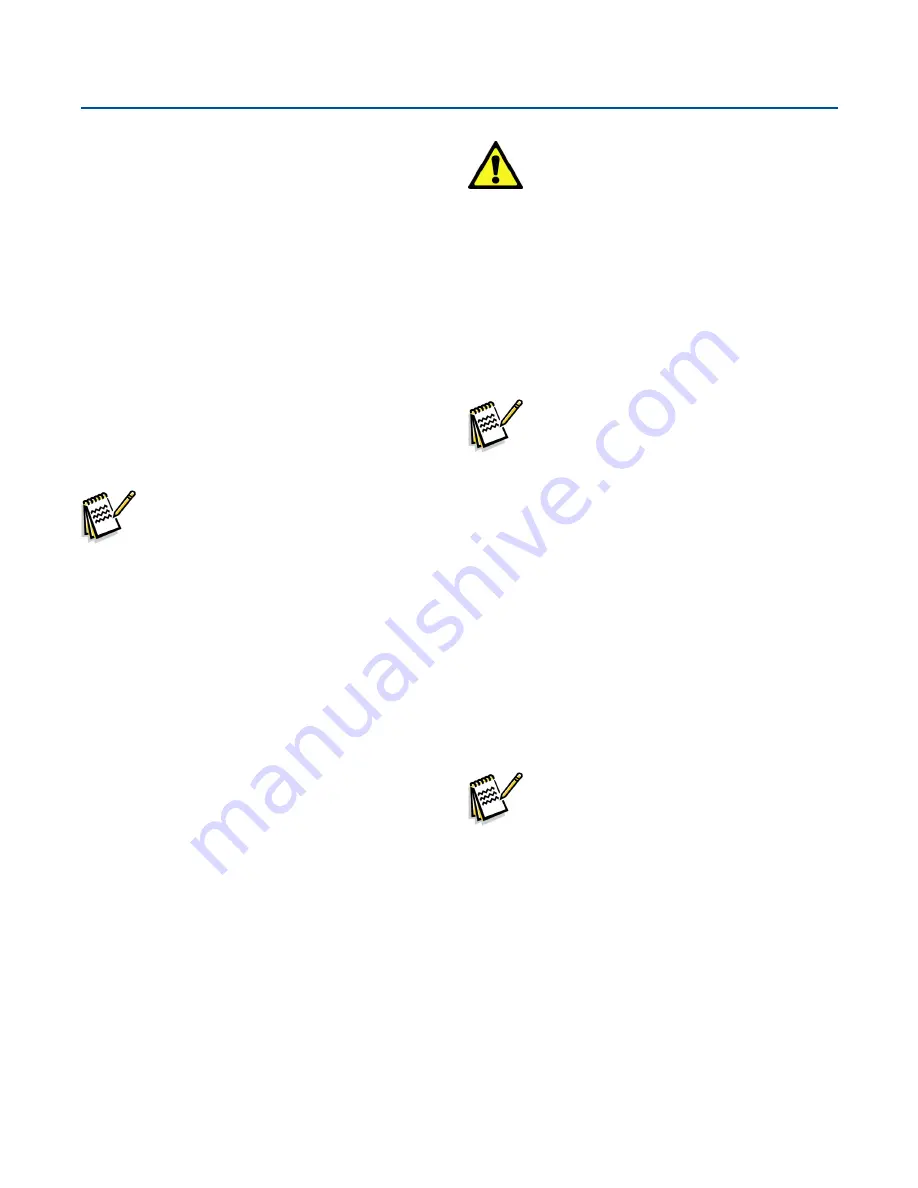
43
Product Manual - Orca
™
CO
2
Series MicroBulk Delivery System
General
This section contains maintenance information Service and/
or repairs are not difficult because parts are easily accessible
and replaceable Before performing any of the procedures
in this section be sure you are familiar with the location
and function of controls and indicators discussed in other
sections It is recommended that the Safety section of this
manual be reviewed and understood fully
Maintenance required usually becomes apparent during
inspection of units before a fill routine, observations
during and after a fill, and from improper performance of
components Proper and immediate action to correct any
damage or malfunction is advised
Persons making repairs to piping, valves, and gauges must be
familiar with cleanliness requirements for components used
in nitrogen, oxygen, argon or carbon dioxide service
Note: During first-ever load, it’s recommended
to check mounting hardward once
loaded.
Daily Observation Checks by
Operator
Beginning of the Day Checks
1 Observe pressure in tank, pressure should not rise much
in tank without the delivery systems operating (5-8 psi
is typical)
2 Ensure safety reliefs are not leaking (frost on safety
vent pipes is an indicator of a leak)
3 If ice forms around valves, ensure the valves are fully
operational If not, defrost with water
4 Check for loose hardware, hydraulic oil leaks, glycol
system leaks, and in general, items out of place
During PTO (Power Take Off) Operation
1 Verify engine speed meets desired speed based on PTO
type
2 Check that there is no vibration from PTO driveline
Preventive Maintenance
Caution:
If there is any vibration, the unit must be
reviewed by a mechanic prior to making
another delivery. Major damage may occur
to equipment.
During Deliveries
1 Review all plumbing and PB for any possible leaks
2 Valves should open and close freely
3 Check for pump noise or lack of building pressure
Note:
If loud grinding noise is observed, contact
Chart for proper diagnosis.
4 Check that printer is operational (if equipped)
5 Check that the Flowcom
®
Flow Meter System has
correct units, service, product type and no fault codes
(this should not change, but could if service work has
been performed)
Weekly Preventive Maintenance
Plumbing Inspection
1 Check that valves and piping are not leaking
2 Tighten nuts, bolts, seals and gaskets
Note:
Ice balls may be a sign of a possible issue.
Power Take Off & Hydraulic System
Inspection
1
Check hydraulic oil level.Top off with ECOSafe FR-46
oil as needed
2 Ensure that transmission has no leaks around PTO
housing
3 Run PTO, ensure a smooth engagement (no grinding/
clunking)
4 Inspect hydraulic lines for leaks or damage
Summary of Contents for Orca MicroBulk CO2 Series
Page 2: ......
Page 13: ...Safety 7 Product Manual Orca CO2 Series MicroBulk Delivery System...
Page 14: ...8 Safety Product Manual Orca CO2 Series MicroBulk Delivery System...
Page 28: ...22 Operations Product Manual Orca CO2 Series MicroBulk Delivery System...
Page 42: ...36 Components Systems Product Manual Orca CO2 Series MicroBulk Delivery System...
Page 48: ...42 Troubleshooting Product Manual Orca CO2 Series MicroBulk Delivery System...
Page 54: ...48 Specifications Product Manual Orca CO2 Series MicroBulk Delivery System Piping Schematic...
Page 55: ...49 Specifications Product Manual Orca CO2 Series MicroBulk Delivery System Nomenclature...
Page 62: ...Product Manual Orca CO2 Series MicroBulk Delivery System...