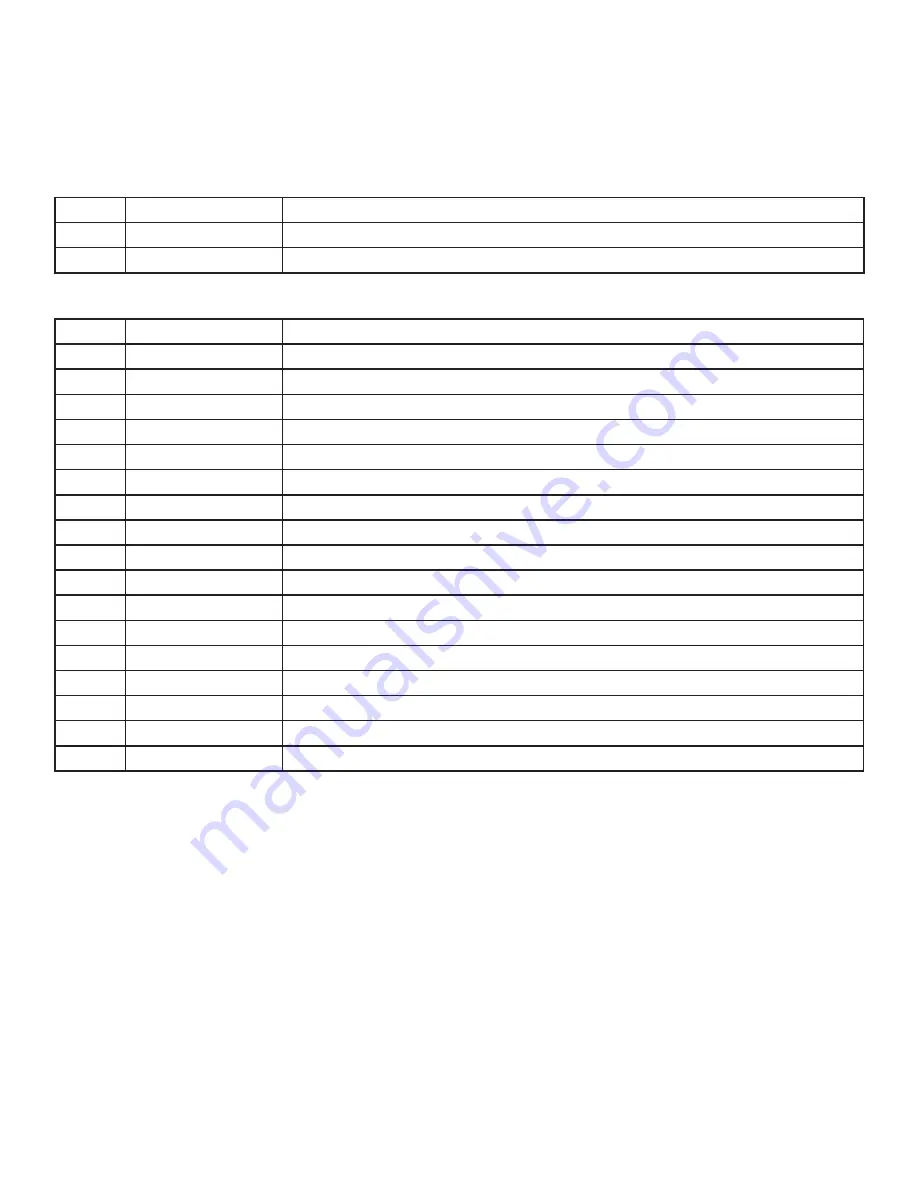
4
PARTS LIST
Prior to beginning installation use the following parts lists to verify that you have received all
components required for installation.
Mounts and Hardware - 300-0197
Qty
Part Number
Description
2
1086
Adjuster rod 3/8-24 x 3”
2
1162-0.495
Ballend tube adapter
2
1262
Lock ring 1-7/8-20
2
1468
Billet anti-roll bar arm 1-1/4” 48-spline
4
2121
Clevis tab 3/8” hole
4
3100-038F1.50Y
Bolt 3/8-24 x 1-1/2 hex head Grade 8
4
3101-038-24C
Locknut 3/8-24 nylon insert
2
3102-038-24LY
Jam nut 3/8-24 LH Grade 5, yellow zinc
2
3102-038-24RC
Jam nut 3/8-24 RH Grade 5, clear zinc
2
3103-038C1.75C
Allen head 3/8-16 x 1-3/4 socket head cap screw
2
3108-038H-C
Lock washer 3/8 high collar
2
3108-038L-C
Lock washer 3/8 regular
4
3109-038-S-2-Y
Aircraft washer 3/8 small OD
2
3111-038X038-LT Rod end 3/8-24 LH x 3/8 bore
2
3111-038X038-RT Rod end 3/8-24 RH x 3/8 bore
2
3157-038F-C
Fender washer 3/8 x 1-1/2 OD
2
3701
Preload adjuster assembly 1-7/8-20 thread
Splined-End Anti-Roll Bar - 5806-U10
Qty
Part Number
Description
1
4765-21
Anti-roll bar 3/4” diameter x 37.35” overall length
1
300-0197
Mounts and hardware
Summary of Contents for 5806-U10
Page 2: ...2 ...
Page 3: ...3 ...
Page 13: ...13 ...
Page 14: ...14 NOTES ...
Page 15: ...15 NOTES ...