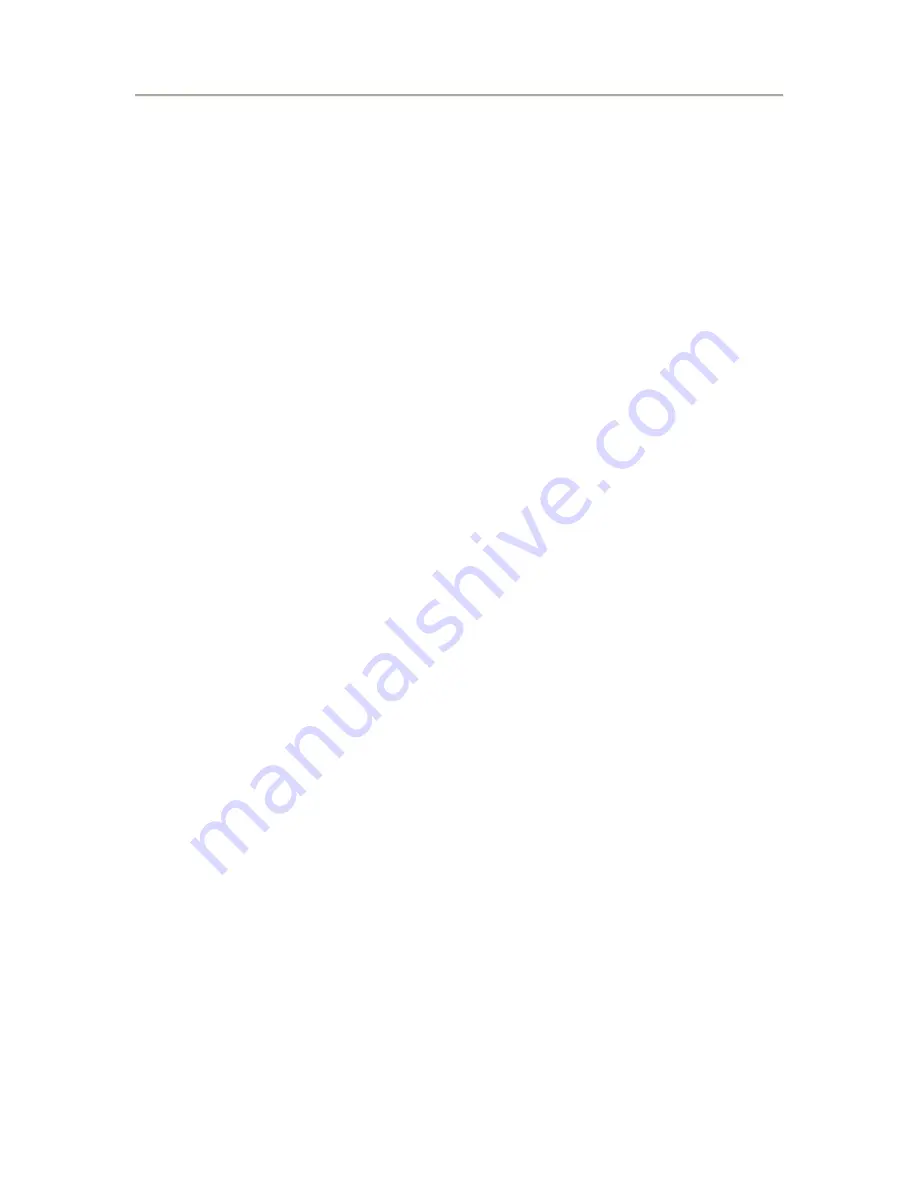
Operation Manual
KRO3000
Rev 2
5
4.0 Process Description and System Components
4.1 General Process
This is to be read in conjunction with the General Arrangement drawing (Figure 1).
The raw water is pre treated before entering the KRO3000. The first stage of pre treatment is a
water softener which eliminates hardness to prevent scaling problems.
The softened water flows to a carbon filter to remove the chlorine which is detrimental to RO
membranes. Following the carbon filter the water passes through a 5 and 1 micron filters
arrangement to remove suspended material.
Filtered water is pumped via a high pressure (boost) pump through the RO housing, containing
the membrane.
Permeate
(treated water) is sent to a break tank and the
Reject
(brine) is sent to
the drain.
A
Recycle
line is also provided, this line goes from the reject line to the pump suction line. The
purpose of the recycle is to create a hydraulic equilibrium, correct recovery rate and system
pressure.
The system is completed with an inlet solenoid valve. This valve automatically turns off the water
supply between the feed water and the membrane. A level control inside the tank sends a signal
to the valve to close when the tank is full. Once the level in the tank is low, the level control sends
another signal to the solenoid valve to permit the flow of raw water into the system. Every time
the valve opens/closes the system will start/stop automatically.
A Flush solenoid valve is also provided with the unit. This valve is under the control of a timer.
Periodically the valve opens to flush the membrane at low pressure. This extends the periods
between membrane cleans.
4.2 System Components
4.2.1 Water
Softener
The water is
Hard
when Calcium and Magnesium are dissolved in it. These salts precipitate out of
the water causing scaling problems. To prevent this situation the water is pre treated using a
water softener.
Raw water flows through a
media (small plastic beads or chemical zeolite)
covered in sodium
ions. The calcium and magnesium ions are replaced with sodium ions. As sodium does not
precipitate out of the water, the scaling problem is eliminated.
However, the media is exhausted after certain amount of water has been treated. This is because
no more sodium ions are available to swap places with calcium and magnesium. Consequently,
the media needs to be regenerated.
The regeneration process is very simple. The media is soaked with a Sodium Chloride (brine
tank) solution. The sodium ions change places with the calcium and magnesium trapped in the
media. In this way the media is being regenerated and is ready to exchange the sodium ions
again. The remaining brine plus all of the calcium and magnesium is flushed through a drain.
The regeneration cycles on the KRO3000 systems are programmed based on the hardness of
the inlet water.