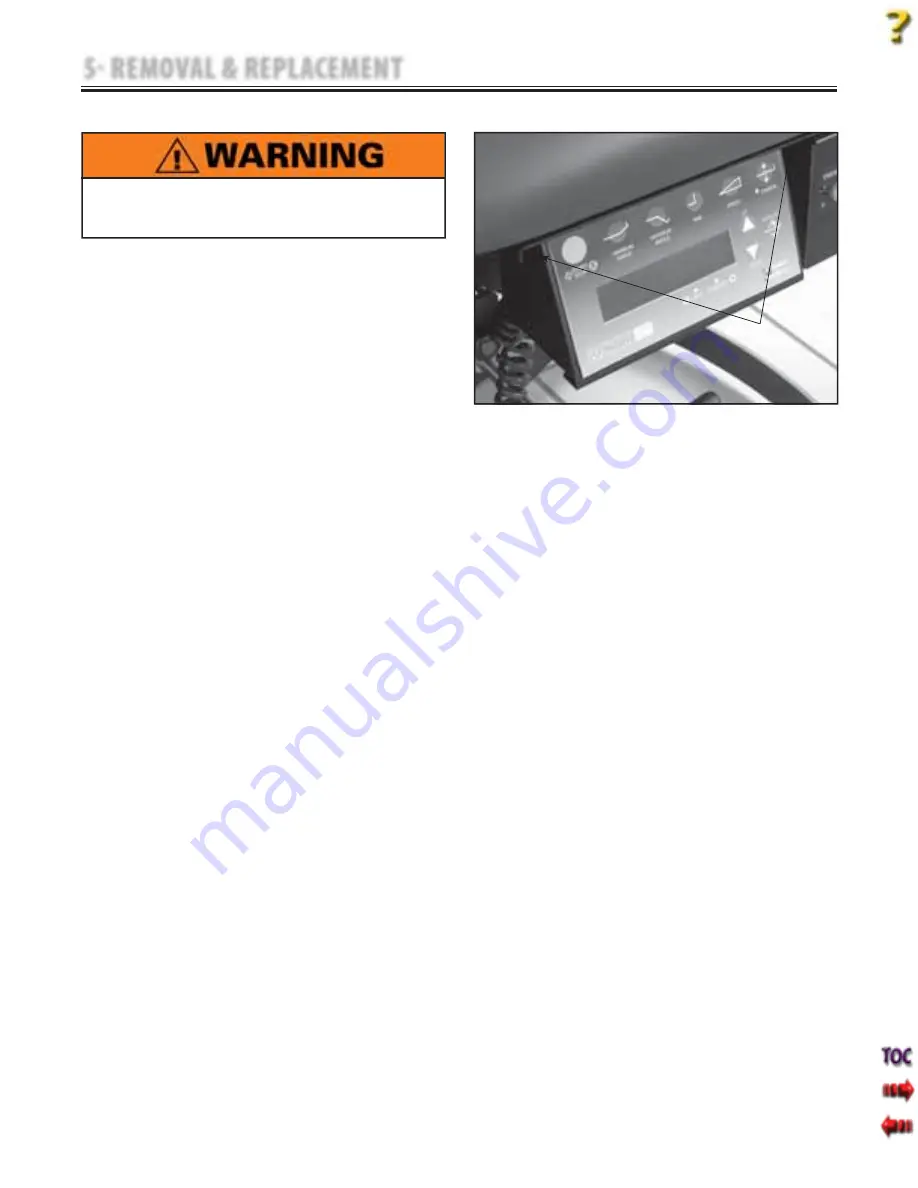
14
Ergostyle ™ FX Tables
5 REMOVAL & REPLACEMENT
5.4 CONTROL BOARD ASSEMBLY REMOVAL AND REPLACEMENT AUTO FLEXION ONLY
Unplug the unit from the power source before
attempting removal or replacement procedures to
prevent electrical shock.
A. Part Numbers
Control Board Assembly
. . . . . . . . . . . . . .58554
B. Equipment Required
#2 Phillips Screwdriver
3/8" and 7/16" End Wrenches
Ground Strap
C. Control Board Assembly Removal
1.
Put Ground Strap on to prevent damage to
the Control Board through static.
2.
Remove the Front Panel of the Control
Housing. See Figure 5.10.
3.
Remove the four Control Board Mounting
Screws securing the Control Board to the
housing.
4.
Remove all harnesses and connectors from
the
Control
Board.
D. Control Board Assembly Replacement
Replace Control Board in reverse order of
removal.
•
•
•
FIGURE 5.10
FRONT PANEL
MOUNTING
SCREWS
Summary of Contents for ERGOSTYLE FX 5820
Page 24: ...Ergostyle FXTables 22 8 SCHEMATICS Block Diagram 1 of 1 ...
Page 25: ...Ergostyle FXTables 23 8 SCHEMATICS Pneumatic 1 of 1 ...
Page 26: ...Ergostyle FXTables 24 8 SCHEMATICS Driver Board 58432 1 of 1 ...
Page 27: ...Ergostyle FXTables 25 8 SCHEMATICS Control Board 58433 1 of 1 ...
Page 28: ...Ergostyle FXTables 26 8 SCHEMATICS Daughter Board 58543 1 of 1 ...