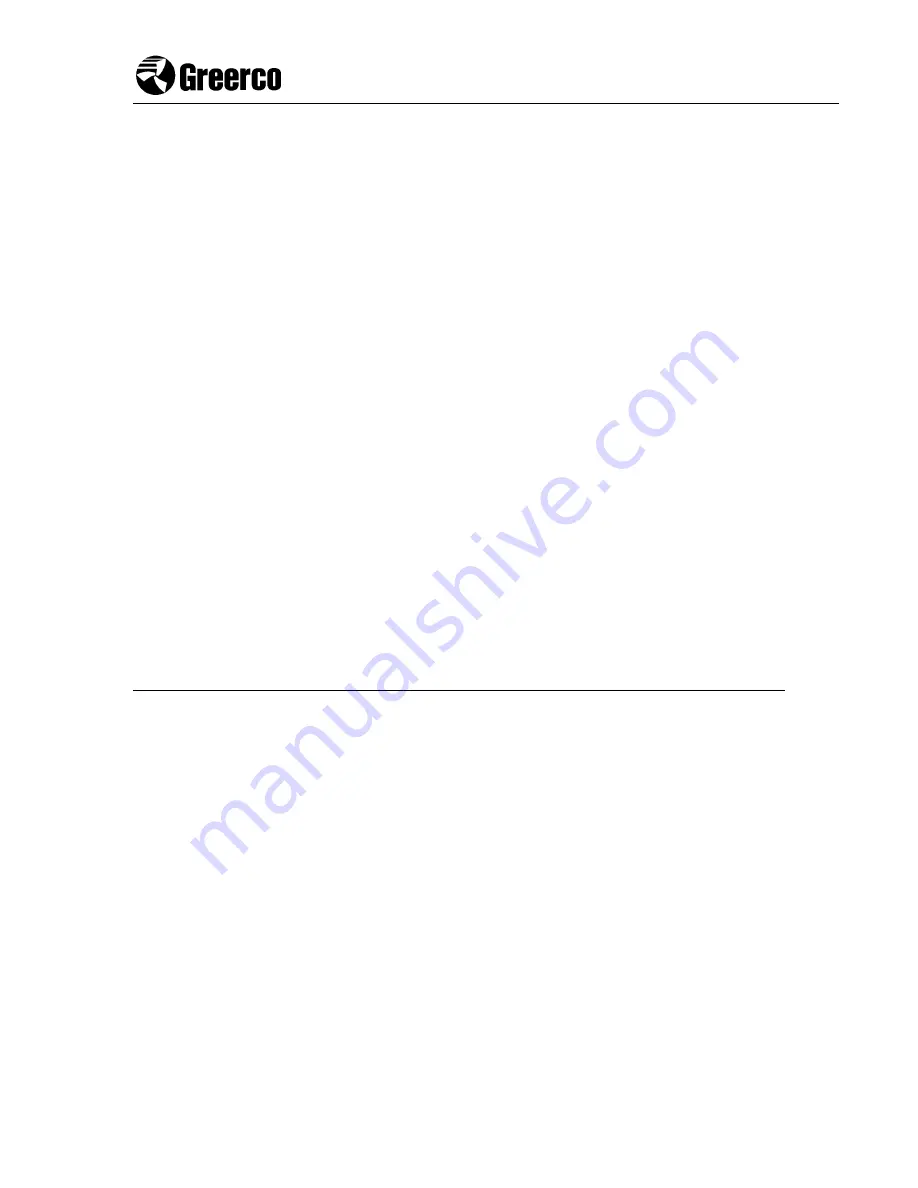
C
OLLOID
M
ILL
I. O. & M
19
3.0 Setting Zero
3.1 Turn dial in bot h directions ensuri ng that m ovement
stops at the point where lock screws were tightened and
that there is no “rubbi ng” or draggi ng when shaft is
turned by hand. Repeat sect ion 2.0 if any rotor/stator
“rubbing” occurs.
3.2 Remove the window frame and the small window
covering the index ring.
3.3 Undo the three (3) screws on the dial index ring
3.4 Align the zero on the index ring with the arrow/indicator
on the housing.
3.5 Retighten the three (3) screws
3.6 Replace the window.
4.0 Testing Zero
4.1 Test the machine setting at zero by turning by hand and
ensuring that there is no rubbing
5.0 Replace Coupling and Operate
N
OTES ON
M
ACHINE
R
EBUILDS
As you make com ponent changes to the equipment, be aware of the
following:
•
If the rotor and stator have been replaced, the m ill will need to be
recalibrated. See preceding procedures.
•
Use caution to be sure that o-ri ngs have not been “pinched” when
placing stator within the stator housing.
•
Before operating, be certain that th e shaft operates freely at t he zero
gap setting.