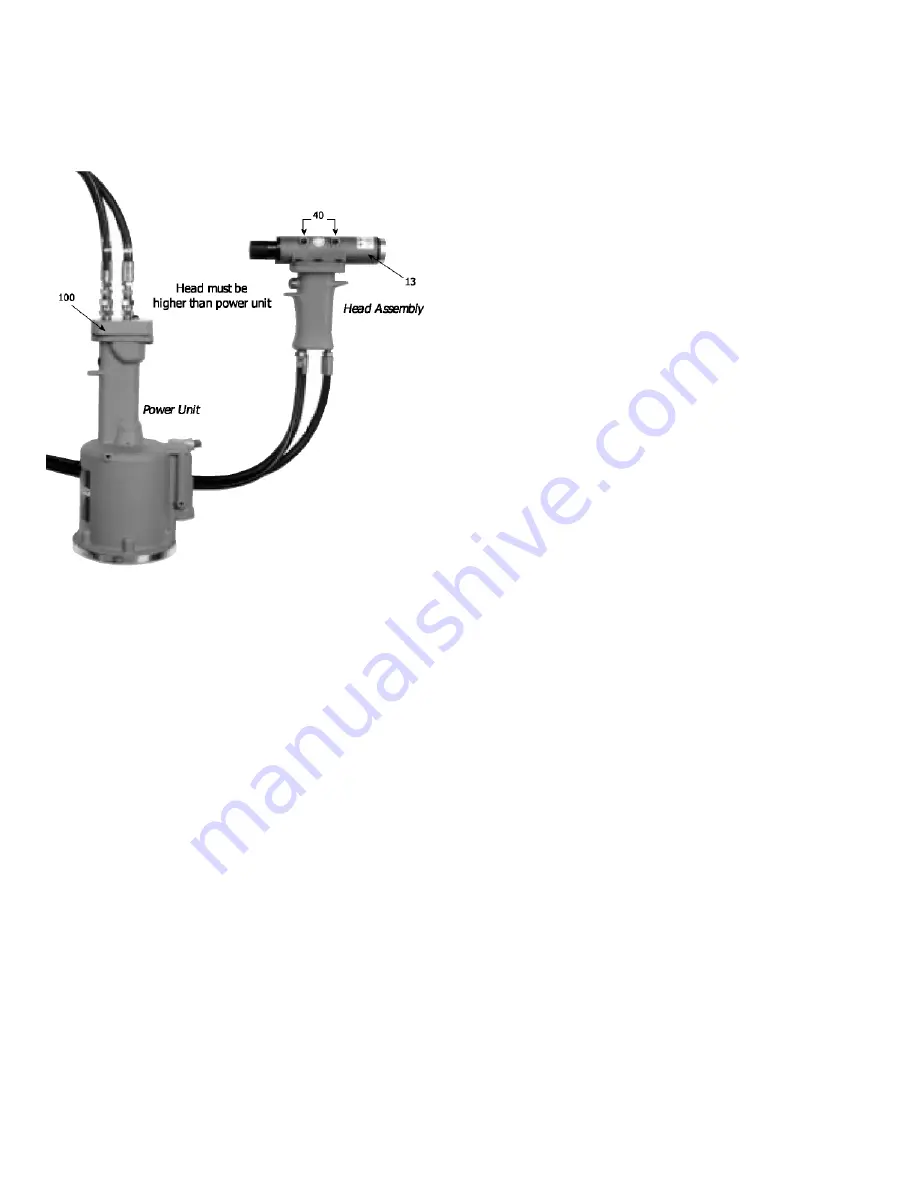
THIS
MODEL
HAS
BEEN
DISCONTINUED;
SEE
G686B
‐
S
FOR
REPLACEMENT
4
F I L L A N D B L E E D I N S T R U C T I O N S
This process is useful to replace a small amount of oil in the tool, place head assembly higher than the power unit.
Remove rear cap screw (40) located on the side of the head being sure NOT to cycle the tool. Attach the Cherry air
bleeder (700A77), connect the tool to the air line and slowly cycle several times. This will ensure the removal of any air
from the hydraulic system and its replacement with fluid.
Should it become necessary to completely refill the tool (such
as would be required after the tool has been dismantled and
re-assembled), take the following steps:
1. After removing the head sub-assembly, hoses and manifold
sub-assembly (100), fill power unit sub-assembly with the
recommended oil to within 1/8" (3 mm) from the top of the
power unit casting (59).
2. Replace head sub-assembly, hoses (86, 87, 88) and manifold
sub-assembly (100), being sure the gasket (95) and O-ring
(41) are properly oriented. Tighten cap screws (96) uniformly
to prevent leakage around gasket.
3. Connect tool to air line. With head and hoses higher than the
power unit, remove both cap screws (40) from the side of the
head sub-assembly.
4. Using a pressurized oil can filled with Dexron® III ATF (or
equivalent), force the fluid into the front hole until it flows
freely from the rear hole. Reverse the procedure until air
bubbles cease appearing at both holes.
5. Replace both cap screws (40) and Stat-O-Seals (39). Cycle the
trigger several times and then repeat steps 3 and 4 above.
6. To ensure the positive removal of all air from the hydraulic
system, we recommend the use of Cherry air bleeder (700A77).
Follow the instructions for the air bleeder above.
T R O U B L E S H O O T I N G
1. Check the air line for correct pressure at the tool. It must
be 90 to 110 psi (6,2 to 7,6 bar).
2. Check for oil leakage:
Oil leaking around the cap screws (40) in the head
indicates that a screw is loose or the Stat-O-Seals
(39) need replacing.
Oil leaking through the by-pass hole at the base of the
power unit (59) indicates that quad rings (61) are worn
or damaged.
Oil leaking from the front of the head body (13)
indicates that O-rings (5 and 11) are worn or
damaged.
3. Check for excessive air leakage from the air valve:
If spring (70) is broken or dislodged, air will
bleed directly through the bottom of the air valve and
the head piston (14) retreats to its full stroke without
returning. See air valve instructions on Page 5.
If O-ring (75) on valve plug (76) is worn or
damaged, replace.
If O-rings (71) on valve spool sub-assembly (99)
are worn or damaged, replace.
4. Check movement of the head piston (14). If it does not
move freely or is slow in operation:
Valve stem (18) may be held off its seat (21) by
contaminants, allowing oil to by-pass. Drain gun,
flush thoroughly and refill with fresh oil.
.Quad ring (63) or O-ring (15) may be damaged and
require replacement.
7. Head piston (14) may be mechanically locked due to
damaged parts.
8. Muffler (77) or air filter (73) inside valve spool sub-
assembly (99) may be plugged with dirt. Clean them
thoroughly with normal solvent and back-blow with
compressed air.
9. Hole in metering screw (74) in valve spool sub-assembly
(99) may be blocked or damaged. Hole diameter should be
.028" (0,711 mm). Clear and size or replace valve spool
sub-assembly (99). Valve spool (72), metering screw (73)
and filter (74) are not sold separately.
5. Check movement of shift piston (24). If it does not move
freely:
Small holes in screen in release piston sub-assembly
(28) may be plugged preventing oil flow. Drain gun, flush
thoroughly and refill with fresh oil. See Fill and Bleed
Instructions
Hole through valve stem (18) may be plugged by
contaminants. Drain gun, flush thoroughly and refill with
fresh oil.
Pulling head components may need maintenance.
Disassemble the pulling head, clean and replace worn
parts. Re-assemble following instructions on page 10.