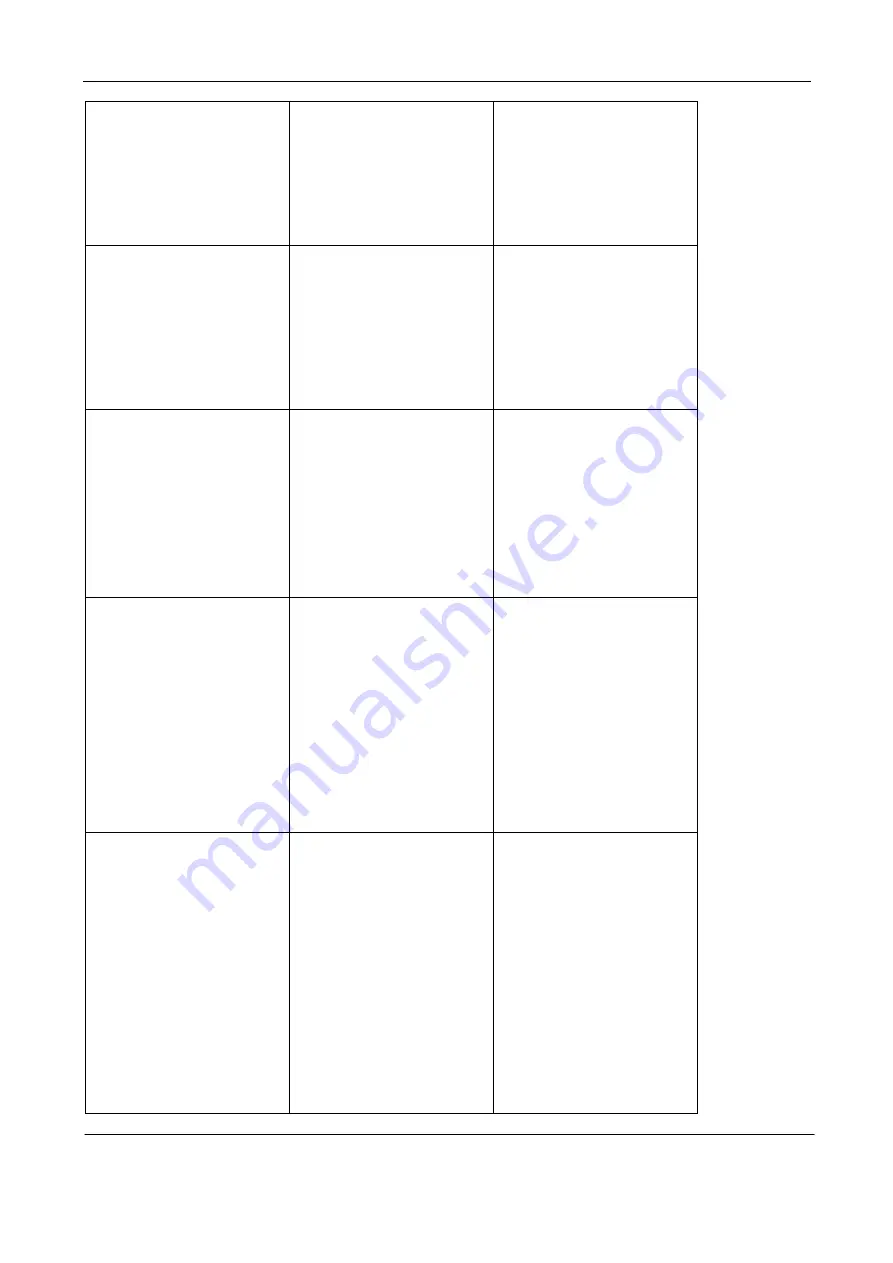
1.0 05/05/2013
33
Finished product surface
finish is not enough.
。
1
.
Wrong speed or feed
rate used.
2
.
The tool is not sharp or
poor in quality.
3
.
Pad iron is too loose.
4
.
Tool is too high.
1
.
Adjust rotation speed
or feed rate properly.
2
.
Sharpen
or
select
better tool.
3
.
Tighten up pad iron.
4
.
Reduce tool height.
Taper
centre
can
not
removed from tailstock.
1
.
Tail shaft has not
retracted
completely
into tailstock.
2
.
Before placing centre
into tail shaft, garbage
on it has not been
cleaned.
1
.
Turn rotation plate of
tailstock
to
make
centre
falling
automatically.
2
.
Always ensure that
centre surface is clean.
Longitudinal
carriage,
cross slide or saddle does
not move smoothly.
1
.
Pad iron has not been
adjusted properly.
2
.
Hand crank loose.
3
.
Lead
screw
mechanism
worn-out
or adjusted improperly.
1
.
Adjust pad iron screws
properly.
2
.
Tighten up hand crank
fasteners
3
.
Tighten up fasteners
that are loose in the
Lead
screw
mechanism.
Hand
cranks
of
longitudinal carriage, cross
slide or saddle are rotated
difficultly.
1
.
There are shavings,
dust or dirt on pad iron.
2
.
Pad iron screws are
too tight.
3
.
Machine bed is too dry.
1
.
Remove
pad
iron,
clean track/make them
coincide
with
each
other, lubricate them
and re-adjust pad iron.
2
.
Loosen screws slowly,
so as to move machine
bed smoothly.
3
.
Lubricate machine bed
and handles.
During cutting, there is
excessive
vibration
in
cutting tool or machine
components.
1.Tool post is not tight
enough.
2.Tool is placed too far
away from the tool post,
which is lack of support.
3.Pad
iron
adjusted
improperly.
4.Tool not sharp.
1
.
Check to find out and
clean off debris, and
then re-fix them.
2
.
Remount tool, so that
portion
of
tool
projecting out of tool
post should not be
more than 1/3 of total
length.
3
.
Tighten up screws of
component affected.
4
.
Replace or resharpen