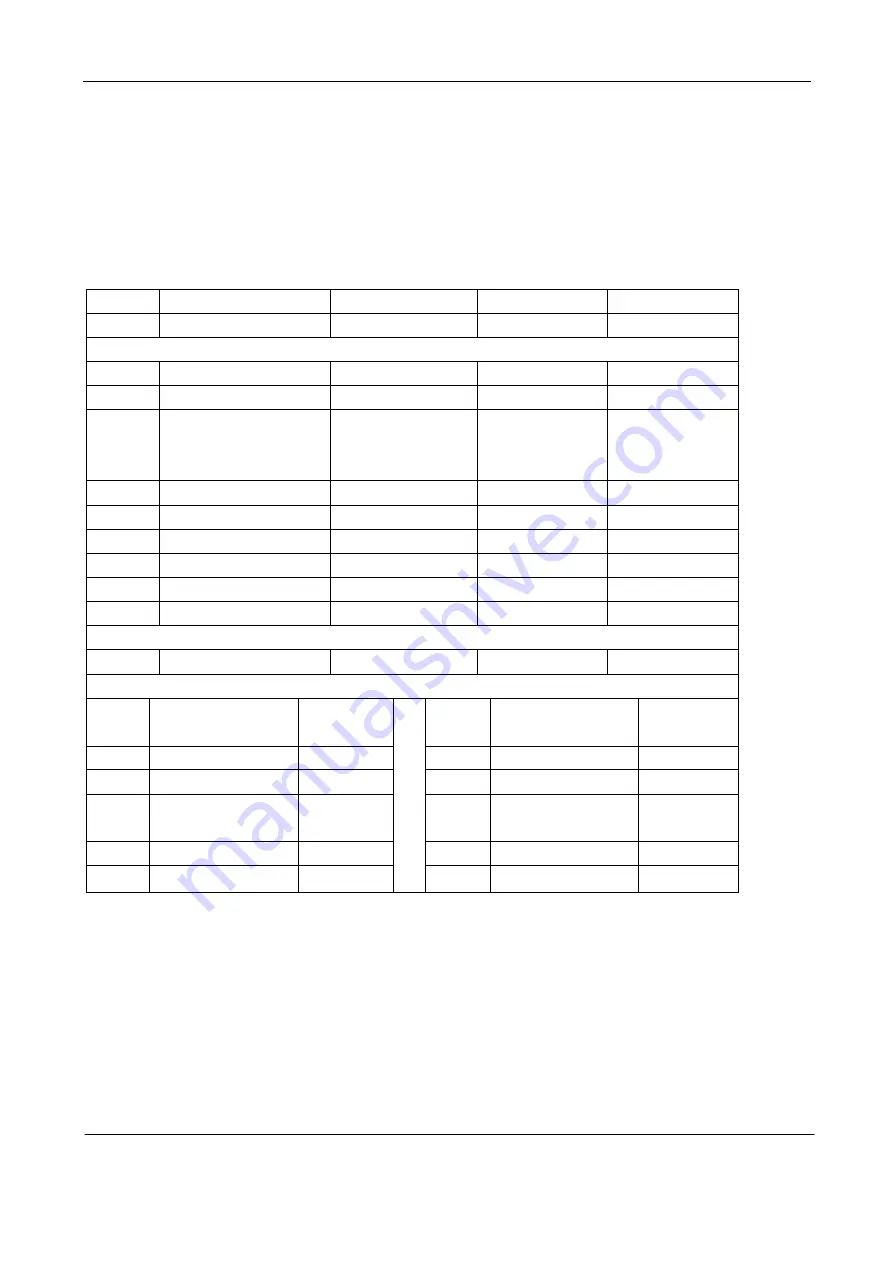
1.0 05/05/2013
43
Packing List
Machine Tool Type
:
CQ0618 Net/Gross Weight [kg]
:
40/45
Machine Tool Name
:
Bench Lathe Case Size (LxWxH)[mm]
:
800×370×420
Manufacturer's Serial No
:
Ser.No.
Name
Specification
Q’ty
Remarks
1
Main machine
CQ0618
1 pc
Accessories accompanied with the machine
:
2
Chuck key
K 180 Chuck
1
3
Anti-jaws of chuck
K1180 Chuck
1 pair
3 pcs/pair
4
Rubber shock pad
CQ0618-01-13
4 sets
Including
screws and
gaskets
5
Double-end spanner
8-10,14-17
1 each
6
Allen wrench
1 set
7
Plastic oiler
1 pc
8
Fixed centre
Morse No.2
1 pc
9
Metric change gears
CQ0618
1 set
10
Fuse
1 pc
Technical documents accompanied with the machine
:
11
Operation Instructions
1 copy
Special accessories accompanied with the machine
:
(
Please select with√ )
12
80mm 4-jaw chuck
13
160mmflower-sha
ped chuck
14
Follower rest
15
Center frame
16
MT3 fixed centre
17
MT2 rolling centre
18
B16 taper shank
connecting rod
19
B16 drill chuck
20
6-piece tool set
21
11-piece tool set
22
23
Warehouse Manager
:
Quality inspected by
:
Examed & verified by
:
Date
:
dd mm yy