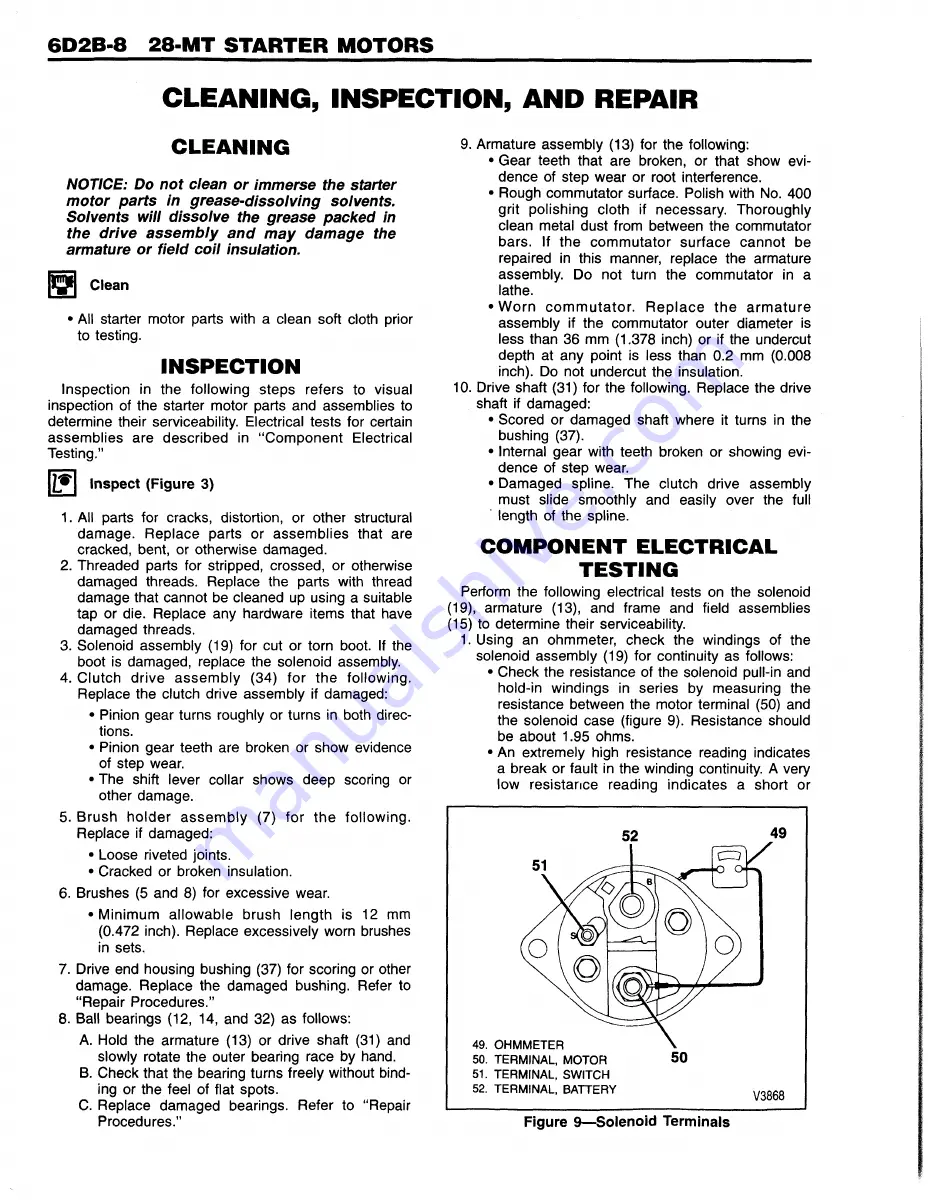
CLEANING, INSPECTION, AND REPAIR
C LEANING
N O T IC E : D o n o t c le a n o r i m m e r s e t h e s t a r t e r
m o t o r p a r t s in g r e a s e - d i s s o l v i n g s o lv e n t s .
S o lv e n t s w ill d is s o lv e t h e g r e a s e p a c k e d in
t h e d r i v e a s s e m b l y a n d m a y d a m a g e t h e
a r m a t u r e o r f i e l d c o i l in s u la t io n .
P iy i Clean
• All starter motor parts with a clean soft cloth prior
to testing.
INSPEC TIO N
Inspection in the following steps refers to visual
inspection of the starter motor parts and assemblies to
determine their serviceability. Electrical tests for certain
assemblies are described in “ Component Electrical
Testing."
I9
Inspect (Figure 3)
1. All parts for cracks, distortion, or other structural
damage. Replace parts or assem blies that are
cracked, bent, or otherwise damaged.
2. Threaded parts for stripped, crossed, or otherwise
damaged threads. Replace the parts with thread
damage that cannot be cleaned up using a suitable
tap or die. Replace any hardware items that have
damaged threads.
3. Solenoid assembly (19) for cut or torn boot. If the
boot is damaged, replace the solenoid assembly.
4. C lutch drive assem bly (34) fo r the following.
Replace the clutch drive assembly if damaged:
• Pinion gear turns roughly or turns in both direc
tions.
• Pinion gear teeth are broken or show evidence
of step wear.
• The shift lever collar shows deep scoring or
other damage.
5. Brush holder a ssem bly (7) fo r th e follow ing.
Replace if damaged:
• Loose riveted joints.
• Cracked or broken insulation.
6. Brushes (5 and 8) for excessive wear.
•M in im u m allow able brush length is 12 mm
(0.472 inch). Replace excessively worn brushes
in sets.
7. Drive end housing bushing (37) for scoring or other
damage. Replace the damaged bushing. Refer to
“ Repair Procedures.”
8. Ball bearings (12, 14, and 32) as follows:
A. Hold the armature (13) or drive shaft (31) and
slowly rotate the outer bearing race by hand.
B. Check that the bearing turns freely without bind
ing or the feel of flat spots.
C. Replace damaged bearings. Refer to “ Repair
Procedures.”
9. Armature assembly (13) for the following:
• Gear teeth that are broken, or that show evi
dence of step wear or root interference.
• Rough commutator surface. Polish with No. 400
grit polishing cloth if necessary. Thoroughly
clean metal dust from between the commutator
bars. If the com m utator surface cannot be
repaired in this manner, replace the armature
assembly. Do not turn the commutator in a
lathe.
• W o rn co m m u ta to r. R e p la ce th e a rm a tu re
assembly if the commutator outer diameter is
less than 36 mm (1.378 inch) or if the undercut
depth at any point is less than 0.2 mm (0.008
inch). Do not undercut the insulation.
10. Drive shaft (31) for the following. Replace the drive
shaft if damaged:
• Scored or damaged shaft where it turns in the
bushing (37).
• Internal gear with teeth broken or showing evi
dence of step wear.
• Damaged spline. The clutch drive assembly
must slide smoothly and easily over the full
length of the spline.
COM PONENT ELECTRICAL
TESTIN G
Perform the following electrical tests on the solenoid
(19), armature (13), and frame and field assemblies
(15) to determine their serviceability.
1. Using an ohmmeter, check the windings of the
solenoid assembly (19) for continuity as follows:
• Check the resistance of the solenoid pull-in and
hold-in windings in series by measuring the
resistance between the motor terminal (50) and
the solenoid case (figure 9). Resistance should
be about 1.95 ohms.
• An extremely high resistance reading indicates
a break or fault in the winding continuity. A very
low resistance reading indicates a short or
Summary of Contents for Light Duty Truck 1994 Series
Page 1: ......
Page 11: ...VIEW A p n n n j VIEW C F7554 Figure 10 Hydra Matic 4L60 E Transmission I D Location ...
Page 24: ...NOTES ...
Page 26: ... ...
Page 69: ...NOTES ...
Page 71: ...3 2 STEERING ...
Page 73: ......
Page 84: ......
Page 102: ...40 ...
Page 130: ...NOTES ...
Page 146: ...NOTES ...
Page 162: ...NOTES ...
Page 166: ...Figure 5 Removing the Pinion Flange Figure 6 Pressing the Drive Pinion from the Cage ...
Page 178: ...Figure 3 Spreading the Differential Case Figure 4 Removing the Differential ...
Page 190: ...NOTES ...
Page 202: ...NOTES ...
Page 206: ...F5785 ...
Page 212: ...B Button Moved Out of Bearing Bore F5791 ...
Page 228: ...NOTES ...
Page 232: ......
Page 234: ......
Page 236: ...Adjuster 63 Bolt 64 Lock Figure 10 Turning the Adjuster Plug K3 Models ...
Page 237: ...Figure 13 Removing the Pinion Seal 39 Bearing Cup Figure 16 Removing the Inner Bearing Cap ...
Page 261: ...F7475 ...
Page 267: ...B Button Moved Out of Bearing Bore F5791 ...
Page 294: ...NOTES ...
Page 300: ...NOTES ...
Page 318: ...NOTES ...
Page 322: ...SR207LN2 EDS ...
Page 324: ......
Page 326: ...OVERHEAD OILING AND RETURN MAIN OIL GALLERY N30005 6A2 J EDS ...
Page 368: ...103 153 127 V1200 ...
Page 370: ......
Page 372: ......
Page 374: ...F9375 Figure 7 Engine Lubrication Diagram Engines Without Balance Shaft ...
Page 376: ...Figure 9 Engine Lubrication Diagram Engines With Balance Shaft ...
Page 399: ...V2974 ...
Page 410: ......
Page 412: ...195 196 201 174 252 163 165 164 244 3706r3924 ...
Page 452: ......
Page 454: ...163 164 V1202 ...
Page 456: ...20 21x 302 210 4 0 41 2 5 2 5 1 2 51 4 2 e3 54 3 9 252 252 S 255 255 25 6 256 209 V1196 ...
Page 458: ...100 1 8 4 185 183 177 v 75 201 3706r1204 ...
Page 460: ......
Page 510: ......
Page 512: ...V2131 ...
Page 514: ...110 106 106 103 90 93 89 88 87 86 v 7 7 7 7 j A _ 111 f t 2 a a s 53 49 L 47 46 3706r4751 ...
Page 566: ...NOTES ...
Page 574: ...NOTES ...
Page 618: ...SPECIAL TOOLS ...
Page 620: ...NOTES ...
Page 672: ......
Page 682: ......
Page 686: ......
Page 694: ...RH0213 4L60 E ...
Page 695: ...657 659 m i J 8092 H J 34196 4 3 34196 5 657 658 665 J 23907 J 7004 1 J 8092 RH0214 4L60 E ...
Page 696: ...J 8092 J 34196 4 33 31 J 8092 RH0215 4L60 E ...
Page 697: ...SPECIAL TOOLS ...
Page 698: ...SPECIAL TOOLS ...
Page 758: ...RH0194 4L80 E ...
Page 764: ......
Page 770: ...SPECIAL TOOLS ...
Page 771: ...SPECIAL TOOLS CONT ...
Page 772: ......
Page 775: ......
Page 776: ......
Page 785: ......
Page 804: ...NOTES ...
Page 806: ......
Page 808: ......
Page 822: ...3707r5079 ...
Page 840: ......
Page 848: ...NOTES ...
Page 852: ......
Page 860: ...F5435 ...
Page 866: ......
Page 878: ...F9167 ...
Page 882: ...16 FrontOutputShaft 18 DrivtQNr 19 DrivenGm t 20 DriveChain 22 FrontOutputBearing V2836 ...
Page 890: ...F9168 ...
Page 908: ......
Page 919: ......