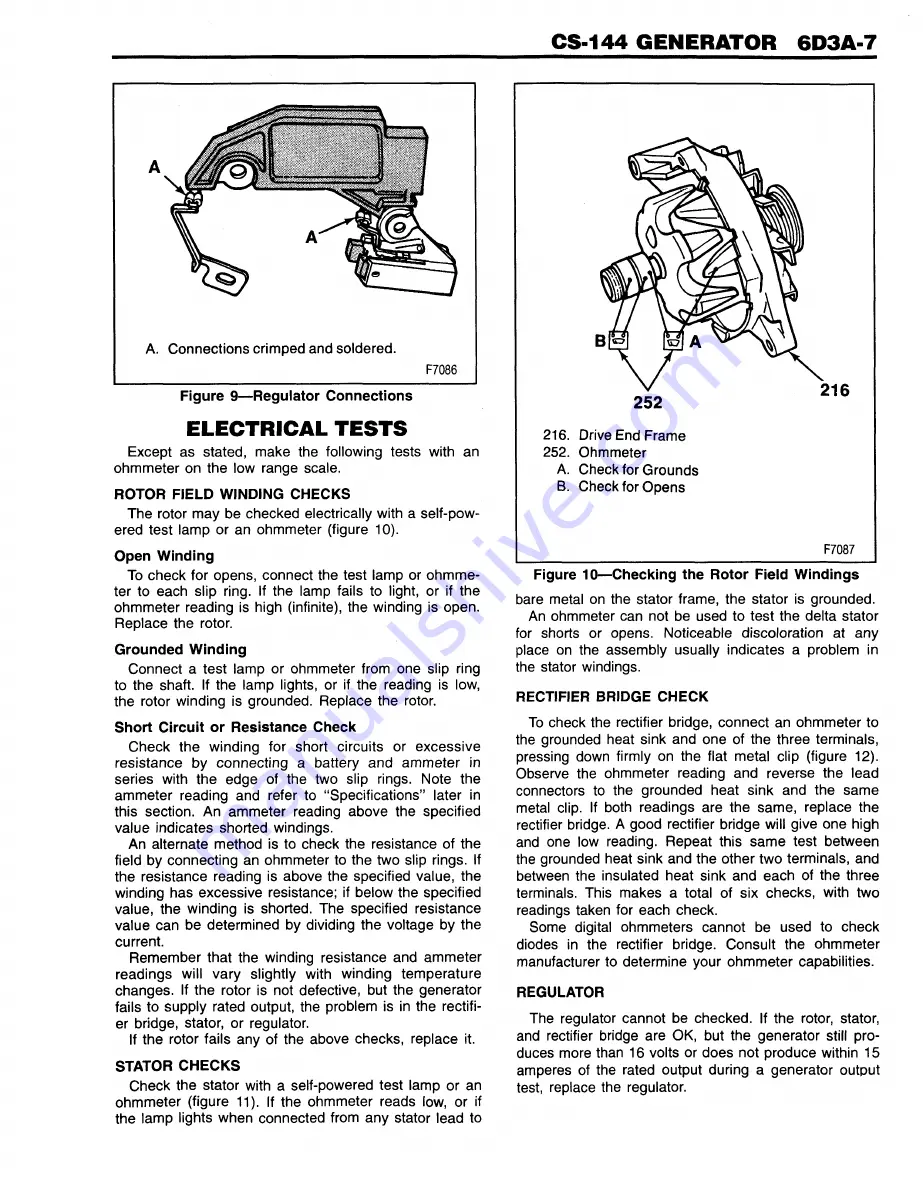
ELECTRICAL TESTS
Except as stated, make the following tests with an
ohmmeter on the low range scale.
ROTOR FIELD WINDING CHECKS
The rotor may be checked electrically with a self-pow
ered test lamp or an ohmmeter (figure 10).
Open Winding
To check for opens, connect the test lamp or ohmme
ter to each slip ring. If the lamp fails to light, or if the
ohmmeter reading is high (infinite), the winding is open.
Replace the rotor.
Grounded Winding
Connect a test lamp or ohmmeter from one slip ring
to the shaft. If the lamp lights, or if the reading is low,
the rotor winding is grounded. Replace the rotor.
Short Circuit or Resistance Check
Check the winding for short circuits or excessive
resistance by connecting a battery and ammeter in
series with the edge of the two slip rings. Note the
ammeter reading and refer to “ Specifications” later in
this section. An ammeter reading above the specified
value indicates shorted windings.
An alternate method is to check the resistance of the
field by connecting an ohmmeter to the two slip rings. If
the resistance reading is above the specified value, the
winding has excessive resistance; if below the specified
value, the winding is shorted. The specified resistance
value can be determined by dividing the voltage by the
current.
Remember that the winding resistance and ammeter
readings will vary slightly with winding temperature
changes. If the rotor is not defective, but the generator
fails to supply rated output, the problem is in the rectifi
er bridge, stator, or regulator.
If the rotor fails any of the above checks, replace it.
STATOR CHECKS
Check the stator with a self-powered test lamp or an
ohmmeter (figure 11). If the ohmmeter reads low, or if
the lamp lights when connected from any stator lead to
bare metal on the stator frame, the stator is grounded.
An ohmmeter can not be used to test the delta stator
for shorts or opens. Noticeable discoloration at any
place on the assembly usually indicates a problem in
the stator windings.
RECTIFIER BRIDGE CHECK
To check the rectifier bridge, connect an ohmmeter to
the grounded heat sink and one of the three terminals,
pressing down firmly on the flat metal clip (figure 12).
Observe the ohmmeter reading and reverse the lead
connectors to the grounded heat sink and the same
metal clip. If both readings are the same, replace the
rectifier bridge. A good rectifier bridge will give one high
and one low reading. Repeat this same test between
the grounded heat sink and the other two terminals, and
between the insulated heat sink and each of the three
terminals. This makes a total of six checks, with two
readings taken for each check.
Some digital ohmmeters cannot be used to check
diodes in the rectifier bridge. Consult the ohmmeter
manufacturer to determine your ohmmeter capabilities.
REGULATOR
The regulator cannot be checked. If the rotor, stator,
and rectifier bridge are OK, but the generator still pro
duces more than 16 volts or does not produce within 15
amperes of the rated output during a generator output
test, replace the regulator.
Summary of Contents for Light Duty Truck 1994 Series
Page 1: ......
Page 11: ...VIEW A p n n n j VIEW C F7554 Figure 10 Hydra Matic 4L60 E Transmission I D Location ...
Page 24: ...NOTES ...
Page 26: ... ...
Page 69: ...NOTES ...
Page 71: ...3 2 STEERING ...
Page 73: ......
Page 84: ......
Page 102: ...40 ...
Page 130: ...NOTES ...
Page 146: ...NOTES ...
Page 162: ...NOTES ...
Page 166: ...Figure 5 Removing the Pinion Flange Figure 6 Pressing the Drive Pinion from the Cage ...
Page 178: ...Figure 3 Spreading the Differential Case Figure 4 Removing the Differential ...
Page 190: ...NOTES ...
Page 202: ...NOTES ...
Page 206: ...F5785 ...
Page 212: ...B Button Moved Out of Bearing Bore F5791 ...
Page 228: ...NOTES ...
Page 232: ......
Page 234: ......
Page 236: ...Adjuster 63 Bolt 64 Lock Figure 10 Turning the Adjuster Plug K3 Models ...
Page 237: ...Figure 13 Removing the Pinion Seal 39 Bearing Cup Figure 16 Removing the Inner Bearing Cap ...
Page 261: ...F7475 ...
Page 267: ...B Button Moved Out of Bearing Bore F5791 ...
Page 294: ...NOTES ...
Page 300: ...NOTES ...
Page 318: ...NOTES ...
Page 322: ...SR207LN2 EDS ...
Page 324: ......
Page 326: ...OVERHEAD OILING AND RETURN MAIN OIL GALLERY N30005 6A2 J EDS ...
Page 368: ...103 153 127 V1200 ...
Page 370: ......
Page 372: ......
Page 374: ...F9375 Figure 7 Engine Lubrication Diagram Engines Without Balance Shaft ...
Page 376: ...Figure 9 Engine Lubrication Diagram Engines With Balance Shaft ...
Page 399: ...V2974 ...
Page 410: ......
Page 412: ...195 196 201 174 252 163 165 164 244 3706r3924 ...
Page 452: ......
Page 454: ...163 164 V1202 ...
Page 456: ...20 21x 302 210 4 0 41 2 5 2 5 1 2 51 4 2 e3 54 3 9 252 252 S 255 255 25 6 256 209 V1196 ...
Page 458: ...100 1 8 4 185 183 177 v 75 201 3706r1204 ...
Page 460: ......
Page 510: ......
Page 512: ...V2131 ...
Page 514: ...110 106 106 103 90 93 89 88 87 86 v 7 7 7 7 j A _ 111 f t 2 a a s 53 49 L 47 46 3706r4751 ...
Page 566: ...NOTES ...
Page 574: ...NOTES ...
Page 618: ...SPECIAL TOOLS ...
Page 620: ...NOTES ...
Page 672: ......
Page 682: ......
Page 686: ......
Page 694: ...RH0213 4L60 E ...
Page 695: ...657 659 m i J 8092 H J 34196 4 3 34196 5 657 658 665 J 23907 J 7004 1 J 8092 RH0214 4L60 E ...
Page 696: ...J 8092 J 34196 4 33 31 J 8092 RH0215 4L60 E ...
Page 697: ...SPECIAL TOOLS ...
Page 698: ...SPECIAL TOOLS ...
Page 758: ...RH0194 4L80 E ...
Page 764: ......
Page 770: ...SPECIAL TOOLS ...
Page 771: ...SPECIAL TOOLS CONT ...
Page 772: ......
Page 775: ......
Page 776: ......
Page 785: ......
Page 804: ...NOTES ...
Page 806: ......
Page 808: ......
Page 822: ...3707r5079 ...
Page 840: ......
Page 848: ...NOTES ...
Page 852: ......
Page 860: ...F5435 ...
Page 866: ......
Page 878: ...F9167 ...
Page 882: ...16 FrontOutputShaft 18 DrivtQNr 19 DrivenGm t 20 DriveChain 22 FrontOutputBearing V2836 ...
Page 890: ...F9168 ...
Page 908: ......
Page 919: ......