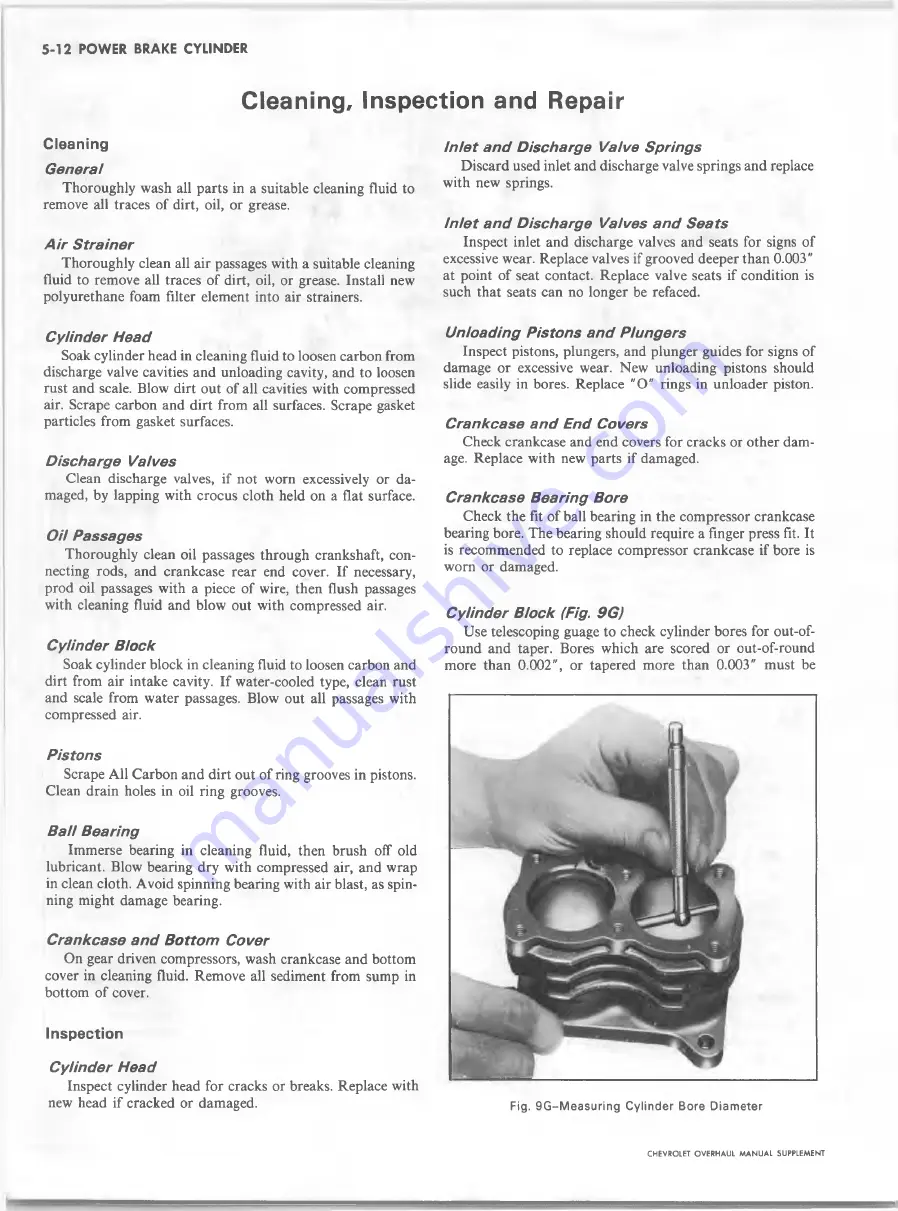
5-12 POW ER BRAKE CYLINDER
Cleaning, Inspection and Repair
C le a n in g
General
Thoroughly wash all parts in a suitable cleaning fluid to
remove all traces of dirt, oil, or grease.
A ir Strainer
Thoroughly clean all air passages with a suitable cleaning
fluid to remove all traces of dirt, oil, or grease. Install new
polyurethane foam filter element into air strainers.
Cylinder Head
Soak cylinder head in cleaning fluid to loosen carbon from
discharge valve cavities and unloading cavity, and to loosen
rust and scale. Blow dirt out of all cavities with compressed
air. Scrape carbon and dirt from all surfaces. Scrape gasket
particles from gasket surfaces.
Discharge Valves
Clean discharge valves, if not worn excessively or da
maged, by lapping with crocus cloth held on a flat surface.
Oil P assages
Thoroughly clean oil passages through crankshaft, con
necting rods, and crankcase rear end cover. If necessary,
prod oil passages with a piece of wire, then flush passages
with cleaning fluid and blow out with compressed air.
Cylinder Block
Soak cylinder block in cleaning fluid to loosen carbon and
dirt from air intake cavity. If water-cooled type, clean rust
and scale from water passages. Blow out all passages with
compressed air.
Pistons
Scrape All Carbon and dirt out of ring grooves in pistons.
Clean drain holes in oil ring grooves.
Ball Bearing
Immerse bearing in cleaning fluid, then brush off old
lubricant. Blow bearing dry with compressed air, and wrap
in clean cloth. Avoid spinning bearing with air blast, as spin
ning might damage bearing.
Crankcase and Bottom Cover
On gear driven compressors, wash crankcase and bottom
cover in cleaning fluid. Remove all sediment from sump in
bottom of cover.
In sp e ctio n
Cylinder Head
Inspect cylinder head for cracks or breaks. Replace with
new head if cracked or damaged.
Inlet a nd Discharge Valve Sp rings
Discard used inlet and discharge valve springs and replace
with new springs.
Inlet a nd D ischarge Valves and Seats
Inspect inlet and discharge valves and seats for signs of
excessive wear. Replace valves if grooved deeper than 0.003"
at point of seat contact. Replace valve seats if condition is
such that seats can no longer be refaced.
Unloading Pistons and P lungers
Inspect pistons, plungers, and plunger guides for signs of
damage or excessive wear. New unloading pistons should
slide easily in bores. Replace "O" rings in unloader piston.
Crankcase and End Covers
Check crankcase and end covers for cracks or other dam
age. Replace with new parts if damaged.
Crankcase Bearing Bore
Check the fit of ball bearing in the compressor crankcase
bearing bore. The bearing should require a finger press fit. It
is recommended to replace compressor crankcase if bore is
worn or damaged.
Cylinder Block (Fig. 9G)
Use telescoping guage to check cylinder bores for out-of-
round and taper. Bores which are scored or out-of-round
more than 0.002", or tapered more than 0.003" must be
Fig. 9G -M e a su rin g C ylinder Bore Diam eter
CHEVROLET OVERHAUL M A N U A L SUPPLEMENT
Summary of Contents for 40 60 Series
Page 1: ...40 60 SERIES TRUCK SUPPLEMENT ST 334 72...
Page 86: ......
Page 96: ...n 47 k u m i i i iin I ll II I...
Page 222: ......