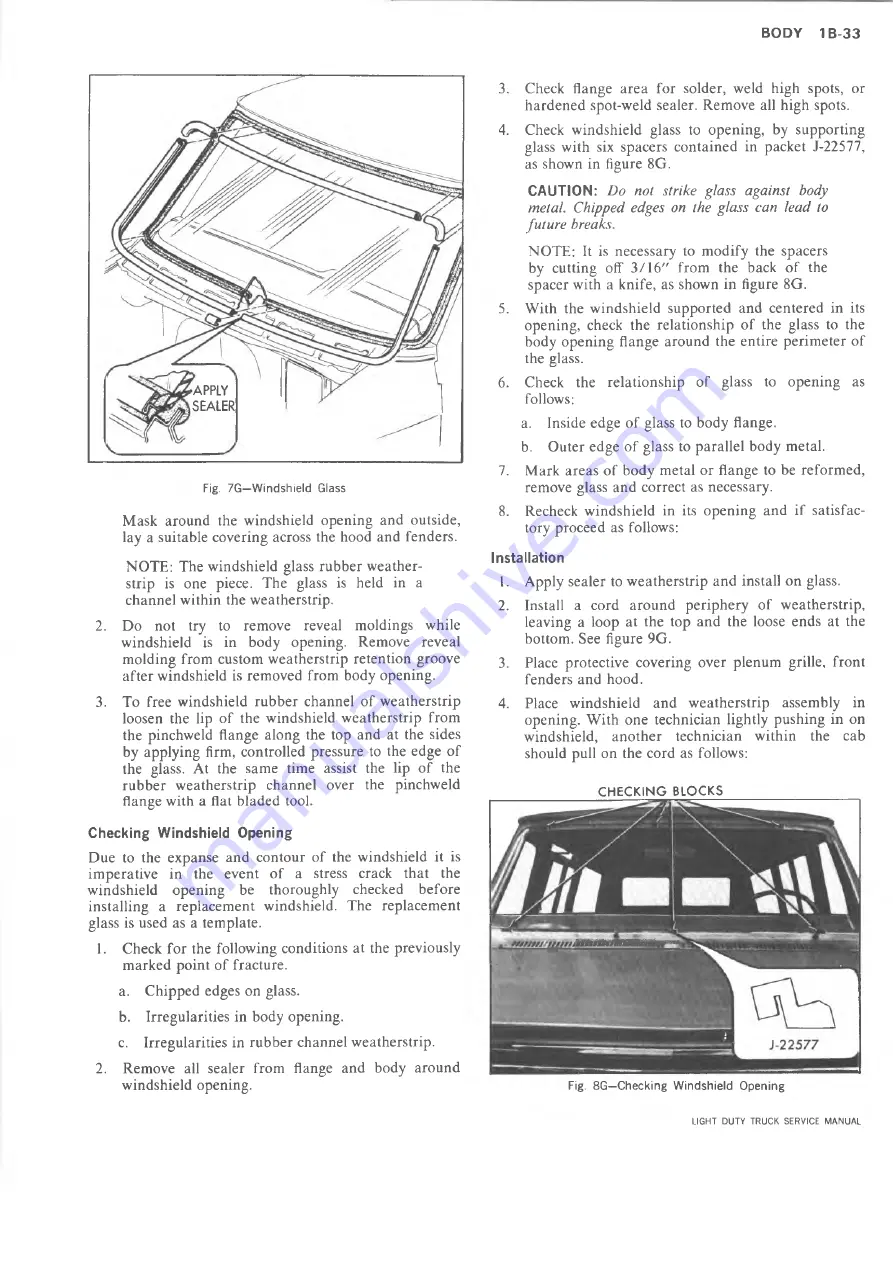
BODY
I B - 3 3
•APPLY
SEALER
Fig. 7G—Windshield Glass
Mask around the windshield opening and outside,
lay a suitable covering across the hood and fenders.
NOTE: The windshield glass rubber weather
strip is one piece. The glass is held in a
channel within the weatherstrip.
2. Do not try to remove reveal moldings while
windshield is in body opening. Remove reveal
molding from custom weatherstrip retention groove
after windshield is removed from body opening.
3. To free windshield rubber channel of weatherstrip
loosen the lip of the windshield weatherstrip from
the pinchweld flange along the top and at the sides
by applying firm, controlled pressure to the edge of
the glass. At the same time assist the lip of the
rubber weatherstrip channel over the pinchweld
flange with a flat bladed tool.
Checking Windshield Opening
Due to the expanse and contour of the windshield it is
imperative in the event of a stress crack that the
windshield opening be thoroughly checked before
installing a replacement windshield. The replacement
glass is used as a template.
1. Check for the following conditions at the previously
marked point of fracture.
a. Chipped edges on glass.
b. Irregularities in body opening.
c. Irregularities in rubber channel weatherstrip.
2. Remove all sealer from flange and body around
windshield opening.
3. Check flange area for solder, weld high spots, or
hardened spot-weld sealer. Remove all high spots.
4. Check windshield glass to opening, by supporting
glass with six spacers contained in packet J-22577,
as shown in figure 8G.
CAUTION:
Do not strike glass against body
metal. Chipped edges on the glass can lead to
future breaks.
NOTE: It is necessary to modify the spacers
by cutting off 3/16" from the back of the
spacer with a knife, as shown in figure 8G.
5. With the windshield supported and centered in its
opening, check the relationship of the glass to the
body opening flange around the entire perimeter of
the glass.
6. Check the relationship of glass to opening as
follows:
a. Inside edge of glass to body flange.
b. Outer edge of glass to parallel body metal.
7. Mark areas of body metal or flange to be reformed,
remove glass and correct as necessary.
8. Recheck windshield in its opening and if satisfac
tory proceed as follows:
Installation
1. Apply sealer to weatherstrip and install on glass.
2. Install a cord around periphery of weatherstrip,
leaving a loop at the top and the loose ends at the
bottom. See figure 9G.
3. Place protective covering over plenum grille, front
fenders and hood.
4. Place windshield and weatherstrip assembly in
opening. With one technician lightly pushing in on
windshield, another technician within the cab
should pull on the cord as follows:
Fig. 8G—Checking Windshield Opening
LIGHT DUTY TRUCK SERVICE MANUAL
CH EC K IN G BLOCKS
Summary of Contents for Light Duty Truck 1973
Page 1: ......
Page 4: ......
Page 6: ......
Page 53: ...HEATER AND AIR CONDITIONING 1A 27 LIGHT DUTY TRUCK SERVICE MANUAL...
Page 115: ...LIGHT DUTY TRUCK SERVICE M A N U A L HEATER AND AIR CONDITIONING 1A 89...
Page 123: ...BODY 1B 3 Fig 6 Typical 06 Van LIGHT DUTY TRUCK SERVICE MANUAL...
Page 149: ...BODY 1B 29 Fig 84 Body Mounting 06 Fig 85 Body Mounting 14 LIGHT DUTY TRUCK SERVICE MANUAL...
Page 171: ...LIGHT DUTY TRUCK SERVICE M A N U A L Fig 2 Frame Horizontal Checking Typical FRAME 2 3...
Page 173: ...LIGHT DUTY TRUCK SERVICE M A N U A L Fig 4 10 30 Series Truck Frame FRAME 2 5...
Page 174: ...2 6 FRAME LIGHT DUTY TRUCK SERVICE MANUAL Fig 5 Underbody Reference Points G Van...
Page 185: ...FRONT SUSPENSION 3 11 Fig 16 Toe out on Turns LIGHT DUTY TRUCK SERVICE MANUAL...
Page 224: ......
Page 266: ......
Page 351: ...ENGINE 6 15 Fig ID Sectional View of Eight Cylinder Engine LIGHT DUTY TRUCK SERVICE MANUAL...
Page 375: ...EN G IN E 6 39 LIGHT DUTY TRUCK SERVICE MANUAL...
Page 376: ...6 4 0 ENGINE LIGHT DUTY TRUCK SERVICE MANUAL...
Page 377: ...ENG IN E 6 41 LIGHT DUTY TRUCK SERVICE MANUAL...
Page 378: ...LIGHT DUTY TRUCK SERVICE MANUAL Fig 37L K Series Engine Front Mount 6 42 ENG INE...
Page 400: ...6 6 4 ENG INE LIGHT DUTY TRUCK SERVICE MANUAL...
Page 401: ...ENG IN E 6 65 LIGHT DUTY TRUCK SERVICE MANUAL...
Page 402: ...6 6 6 ENGINE LIGHT DUTY TRUCK SERVICE MANUAL...
Page 403: ...E NG IN E 6 67 Fig 36V C Series Engine Mounts LIGHT DUTY TRUCK SERVICE MANUAL...
Page 410: ......
Page 423: ...EN G IN E C OOLING 6K 13 Fig 16 Overheating Chart LIGHT DUTY TRUCK SERVICE MANUAL...
Page 424: ...6 K 1 4 ENG INE COOLING Fig 17 Coolant Loss Chart LIGHT DUTY TRUCK SERVICE MANUAL...
Page 456: ...6M 32 ENGINE FUEL Fig K15 Accelerator Controls G Van L 6 LIGHT DUTY TRUCK SERVICE MANUAL...
Page 492: ......
Page 512: ...Fig 18e Vacuum Advance Diagram V8 Engine...
Page 516: ...6 T 2 4 E M IS S IO N CONTROL SYSTEMS LIGHT DUTY TRUCK SERVICE MANUAL...
Page 528: ......
Page 590: ......
Page 593: ...CLUTCHES MANUAL TRANSMISSIONS 7M 3 LIGHT DUTY TRUCK SERVICE MANUAL...
Page 598: ...7M 8 CLUTCHES MANUAL TRANSMISSIONS LIGHT DUTY TRUCK SERVICE MANUAL...
Page 642: ......
Page 654: ......
Page 743: ...FUEL TANKS AND EXHAUST 8 13 LIGHT DUTY TRUCK SERVICE MANUAL...
Page 744: ...8 14 FUEL TANKS AND EXHAUST LIGHT DUTY TRUCK SERVICE MANUAL...
Page 760: ...8 30 FUEL TANKS AND EXHAUST Fig 40 Exhaust Pipe P Models LIGHT DUTY TRUCK SERVICE MANUAL...
Page 761: ...FUEL TANKS AND EXHAUST 8 31 LIGHT DUTY TRUCK SERVICE MANUAL...
Page 763: ...FUEL TANKS AND EXHAUST 8 33 LIGHT DUTY TRUCK SERVICE MANUAL...
Page 766: ......
Page 832: ...LIGHT DUTY TRUCK SERVICE MANUAL Fig 106 Power Steering Pump Mounting Typical 9 66 STEERING...
Page 833: ...PUMP ASSEMBLY STEERING GEAR TYPICAL SMALL V8 TYPICAL LARGE V8 STEERING 9 67...
Page 861: ...STEERING 9 95 Fig 134 Power Steering Pump Leakage LIGHT DUTY TRUCK SERVICE MANUAL...
Page 864: ......
Page 876: ......
Page 886: ...11 10 CHASSIS SHEET METAL LIGHT DUTY TRUCK SERVICE MANUAL...
Page 891: ...ELECTRICAL BODY AND CHASSIS 12 5 LIGHT DUTY TRUCK SERVICE MANUAL...
Page 934: ......
Page 942: ......
Page 970: ......
Page 972: ......
Page 974: ......
Page 976: ...V...
Page 978: ......
Page 979: ......