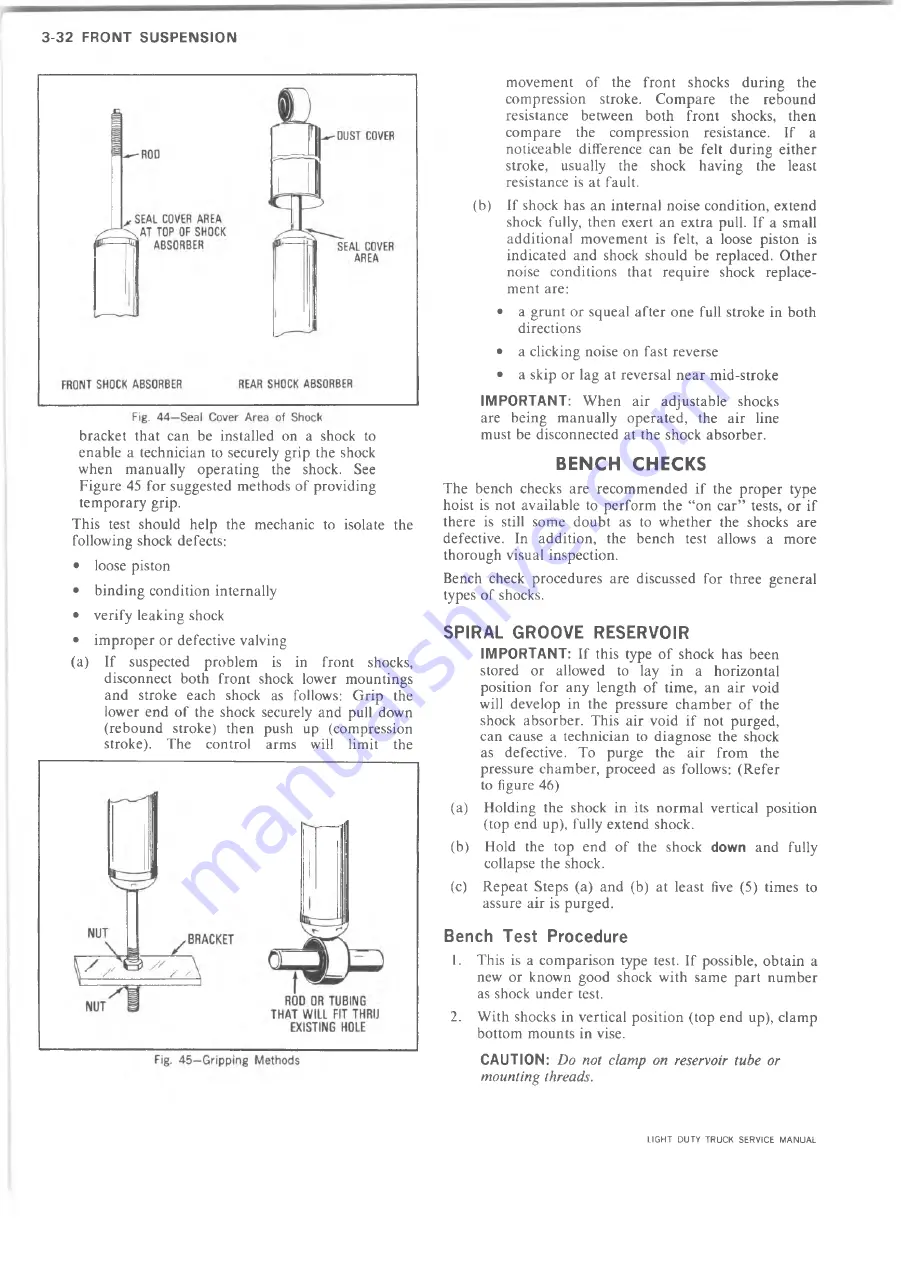
3 -3 2 FRONT S U S PEN SIO N
bracket that can be installed on a shock to
enable a technician to securely grip the shock
when manually operating the shock. See
Figure 45 for suggested methods of providing
temporary grip.
This test should help the mechanic to isolate the
following shock defects:
• loose piston
• binding condition internally
• verify leaking shock
• improper or defective valving
(a) If suspected problem is in front shocks,
disconnect both front shock lower mountings
and stroke each shock as follows: Grip the
lower end of the shock securely and pull down
(rebound stroke) then push up (compression
stroke). The control arms will limit the
movement of the front shocks during the
compression stroke. Compare the rebound
resistance between both front shocks, then
compare the compression resistance. If a
noticeable difference can be felt during either
stroke, usually the shock having the least
resistance is at fault.
(b) If shock has an internal noise condition, extend
shock fully, then exert an extra pull. If a small
additional movement is felt, a loose piston is
indicated and shock should be replaced. Other
noise conditions that require shock replace
ment are:
• a grunt or squeal after one full stroke in both
directions
• a clicking noise on fast reverse
• a skip or lag at reversal near mid-stroke
IM PORTANT:
When air adjustable shocks
are being manually operated, the air line
must be disconnected at the shock absorber.
BENCH CHECKS
The bench checks are recommended if the proper type
hoist is not available to perform the “on car” tests, or if
there is still some doubt as to whether the shocks are
defective. In addition, the bench test allows a more
thorough visual inspection.
Bench check procedures are discussed for three general
types of shocks.
SPIRAL GROOVE RESERVOIR
IM PORTANT:
If this type of shock has been
stored or allowed to lay in a horizontal
position for any length of time, an air void
will develop in the pressure chamber of the
shock absorber. This air void if not purged,
can cause a technician to diagnose the shock
as defective. To purge the air from the
pressure chamber, proceed as follows: (Refer
to figure 46)
(a) Holding the shock in its normal vertical position
(top end up), fully extend shock.
(b) Hold the top end of the shock
down
and fully
collapse the shock.
(c) Repeat Steps (a) and (b) at least five (5) times to
assure air is purged.
Bench Test Procedure
1. This is a comparison type test. If possible, obtain a
new or known good shock with same part number
as shock under test.
2. With shocks in vertical position (top end up), clamp
bottom mounts in vise.
CAUTION:
Do not clamp on reservoir tube or
mounting threads.
LIGHT DUTY TRUCK SERVICE MANUAL
Summary of Contents for Light Duty Truck 1973
Page 1: ......
Page 4: ......
Page 6: ......
Page 53: ...HEATER AND AIR CONDITIONING 1A 27 LIGHT DUTY TRUCK SERVICE MANUAL...
Page 115: ...LIGHT DUTY TRUCK SERVICE M A N U A L HEATER AND AIR CONDITIONING 1A 89...
Page 123: ...BODY 1B 3 Fig 6 Typical 06 Van LIGHT DUTY TRUCK SERVICE MANUAL...
Page 149: ...BODY 1B 29 Fig 84 Body Mounting 06 Fig 85 Body Mounting 14 LIGHT DUTY TRUCK SERVICE MANUAL...
Page 171: ...LIGHT DUTY TRUCK SERVICE M A N U A L Fig 2 Frame Horizontal Checking Typical FRAME 2 3...
Page 173: ...LIGHT DUTY TRUCK SERVICE M A N U A L Fig 4 10 30 Series Truck Frame FRAME 2 5...
Page 174: ...2 6 FRAME LIGHT DUTY TRUCK SERVICE MANUAL Fig 5 Underbody Reference Points G Van...
Page 185: ...FRONT SUSPENSION 3 11 Fig 16 Toe out on Turns LIGHT DUTY TRUCK SERVICE MANUAL...
Page 224: ......
Page 266: ......
Page 351: ...ENGINE 6 15 Fig ID Sectional View of Eight Cylinder Engine LIGHT DUTY TRUCK SERVICE MANUAL...
Page 375: ...EN G IN E 6 39 LIGHT DUTY TRUCK SERVICE MANUAL...
Page 376: ...6 4 0 ENGINE LIGHT DUTY TRUCK SERVICE MANUAL...
Page 377: ...ENG IN E 6 41 LIGHT DUTY TRUCK SERVICE MANUAL...
Page 378: ...LIGHT DUTY TRUCK SERVICE MANUAL Fig 37L K Series Engine Front Mount 6 42 ENG INE...
Page 400: ...6 6 4 ENG INE LIGHT DUTY TRUCK SERVICE MANUAL...
Page 401: ...ENG IN E 6 65 LIGHT DUTY TRUCK SERVICE MANUAL...
Page 402: ...6 6 6 ENGINE LIGHT DUTY TRUCK SERVICE MANUAL...
Page 403: ...E NG IN E 6 67 Fig 36V C Series Engine Mounts LIGHT DUTY TRUCK SERVICE MANUAL...
Page 410: ......
Page 423: ...EN G IN E C OOLING 6K 13 Fig 16 Overheating Chart LIGHT DUTY TRUCK SERVICE MANUAL...
Page 424: ...6 K 1 4 ENG INE COOLING Fig 17 Coolant Loss Chart LIGHT DUTY TRUCK SERVICE MANUAL...
Page 456: ...6M 32 ENGINE FUEL Fig K15 Accelerator Controls G Van L 6 LIGHT DUTY TRUCK SERVICE MANUAL...
Page 492: ......
Page 512: ...Fig 18e Vacuum Advance Diagram V8 Engine...
Page 516: ...6 T 2 4 E M IS S IO N CONTROL SYSTEMS LIGHT DUTY TRUCK SERVICE MANUAL...
Page 528: ......
Page 590: ......
Page 593: ...CLUTCHES MANUAL TRANSMISSIONS 7M 3 LIGHT DUTY TRUCK SERVICE MANUAL...
Page 598: ...7M 8 CLUTCHES MANUAL TRANSMISSIONS LIGHT DUTY TRUCK SERVICE MANUAL...
Page 642: ......
Page 654: ......
Page 743: ...FUEL TANKS AND EXHAUST 8 13 LIGHT DUTY TRUCK SERVICE MANUAL...
Page 744: ...8 14 FUEL TANKS AND EXHAUST LIGHT DUTY TRUCK SERVICE MANUAL...
Page 760: ...8 30 FUEL TANKS AND EXHAUST Fig 40 Exhaust Pipe P Models LIGHT DUTY TRUCK SERVICE MANUAL...
Page 761: ...FUEL TANKS AND EXHAUST 8 31 LIGHT DUTY TRUCK SERVICE MANUAL...
Page 763: ...FUEL TANKS AND EXHAUST 8 33 LIGHT DUTY TRUCK SERVICE MANUAL...
Page 766: ......
Page 832: ...LIGHT DUTY TRUCK SERVICE MANUAL Fig 106 Power Steering Pump Mounting Typical 9 66 STEERING...
Page 833: ...PUMP ASSEMBLY STEERING GEAR TYPICAL SMALL V8 TYPICAL LARGE V8 STEERING 9 67...
Page 861: ...STEERING 9 95 Fig 134 Power Steering Pump Leakage LIGHT DUTY TRUCK SERVICE MANUAL...
Page 864: ......
Page 876: ......
Page 886: ...11 10 CHASSIS SHEET METAL LIGHT DUTY TRUCK SERVICE MANUAL...
Page 891: ...ELECTRICAL BODY AND CHASSIS 12 5 LIGHT DUTY TRUCK SERVICE MANUAL...
Page 934: ......
Page 942: ......
Page 970: ......
Page 972: ......
Page 974: ......
Page 976: ...V...
Page 978: ......
Page 979: ......