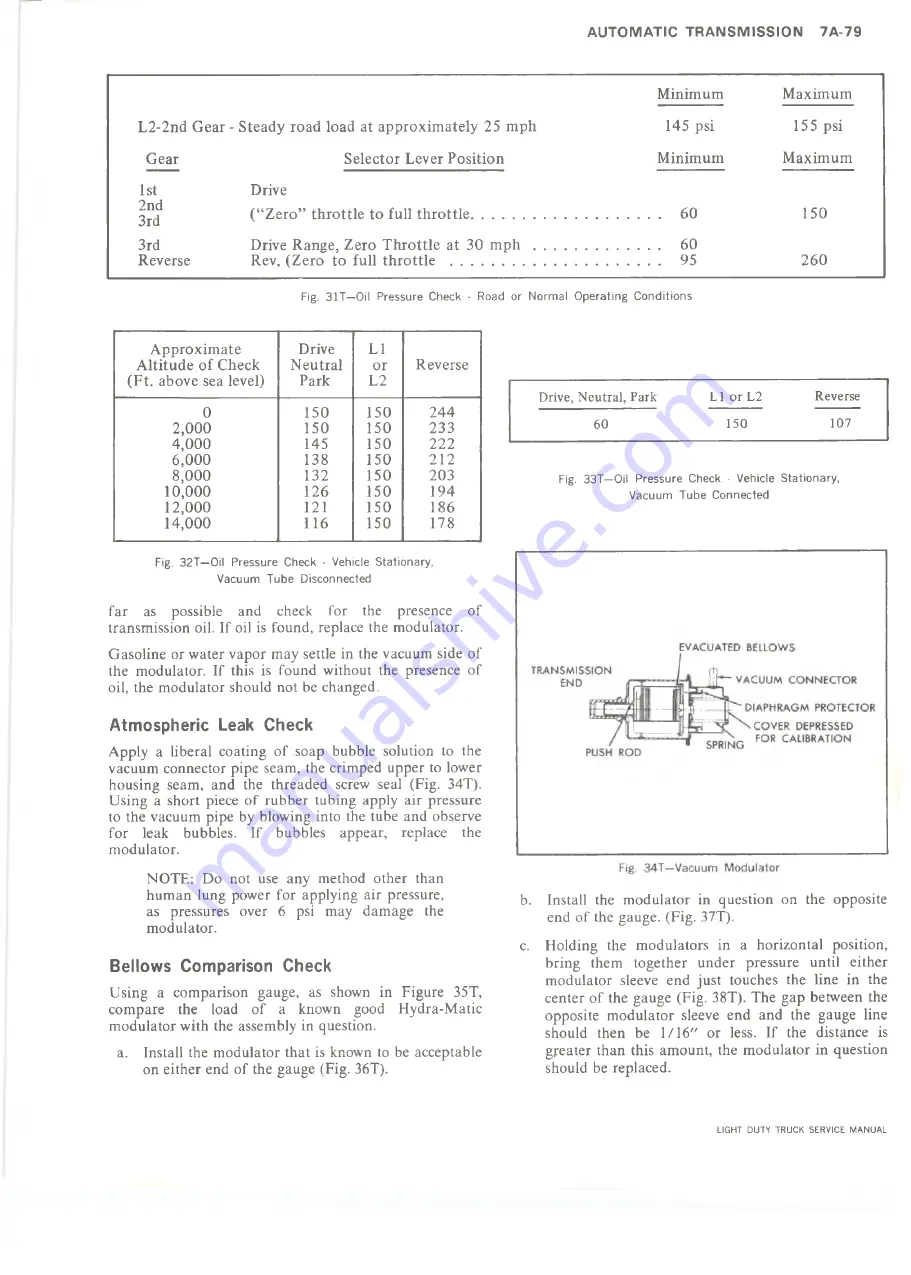
A U T O M A T IC T R A N S M IS S I O N
7 A -79
Minimum
Maximum
L2-2nd Gear - Steady road load at approxim ately 25 mph
145 psi
155 psi
Gear
Selector Lever Position
Minimum
Maximum
1st
Drive
2nd
3rd
(“ Zero” throttle to full thro ttle................................. ............... 60
150
3rd
Drive Range, Zero Throttle at 30 m p h ............... ............... 60
Reverse
Rev. (Zero to full throttle ....................................... ............... 95
260
Fig. 31T—Oil Pressure Check - Road or Normal Operating Conditions
Approxim ate
Altitude of Check
(Ft. above sea level)
Drive
Neutral
Park
LI
or
L2
Reverse
0
150
150
244
2,000
150
150
233
4,000
145
150
222
6,000
138
150
212
8,000
132
150
203
10,000
126
150
194
12,000
121
150
186
14,000
116
150
178
Drive, Neutral, Park
LI or L2
Reverse
60
150
107
Fig. 33T—Oil Pressure Check • Vehicle Stationary,
Vacuum Tube Connected
Fig. 32T—Oil Pressure Check • Vehicle Stationary,
Vacuum Tube Disconnected
far as possible and check for the presence of
transmission oil. If oil is found, replace the modulator.
Gasoline or water vapor may settle in the vacuum side of
the modulator. If this is found without the presence of
oil, the modulator should not be changed.
Atmospheric Leak Check
Apply a liberal coating of soap bubble solution to the
vacuum connector pipe seam, the crimped upper to lower
housing seam, and the threaded screw seal (Fig. 34T).
Using a short piece of rubber tubing apply air pressure
to the vacuum pipe by blowing into the tube and observe
for leak bubbles. If bubbles appear, replace the
modulator.
NOTE: Do not use any method other than
human lung power for applying air pressure,
as pressures over 6 psi may damage the
modulator.
Bellows Comparison Check
Using a comparison gauge, as shown in Figure 35T,
compare the load of a known good Hydra-Matic
modulator with the assembly in question.
a. Install the modulator that is known to be acceptable
on either end of the gauge (Fig. 36T).
b. Install the modulator in question on the opposite
end of the gauge. (Fig. 37T).
c. Holding the modulators in a horizontal position,
bring them together under pressure until either
modulator sleeve end just touches the line in the
center of the gauge (Fig. 38T). The gap between the
opposite modulator sleeve end and the gauge line
should then be 1/16" or less. If the distance is
greater than this amount, the modulator in question
should be replaced.
LIGHT DUTY TRUCK SERVICE MANUAL
Summary of Contents for Light Duty Truck 1973
Page 1: ......
Page 4: ......
Page 6: ......
Page 53: ...HEATER AND AIR CONDITIONING 1A 27 LIGHT DUTY TRUCK SERVICE MANUAL...
Page 115: ...LIGHT DUTY TRUCK SERVICE M A N U A L HEATER AND AIR CONDITIONING 1A 89...
Page 123: ...BODY 1B 3 Fig 6 Typical 06 Van LIGHT DUTY TRUCK SERVICE MANUAL...
Page 149: ...BODY 1B 29 Fig 84 Body Mounting 06 Fig 85 Body Mounting 14 LIGHT DUTY TRUCK SERVICE MANUAL...
Page 171: ...LIGHT DUTY TRUCK SERVICE M A N U A L Fig 2 Frame Horizontal Checking Typical FRAME 2 3...
Page 173: ...LIGHT DUTY TRUCK SERVICE M A N U A L Fig 4 10 30 Series Truck Frame FRAME 2 5...
Page 174: ...2 6 FRAME LIGHT DUTY TRUCK SERVICE MANUAL Fig 5 Underbody Reference Points G Van...
Page 185: ...FRONT SUSPENSION 3 11 Fig 16 Toe out on Turns LIGHT DUTY TRUCK SERVICE MANUAL...
Page 224: ......
Page 266: ......
Page 351: ...ENGINE 6 15 Fig ID Sectional View of Eight Cylinder Engine LIGHT DUTY TRUCK SERVICE MANUAL...
Page 375: ...EN G IN E 6 39 LIGHT DUTY TRUCK SERVICE MANUAL...
Page 376: ...6 4 0 ENGINE LIGHT DUTY TRUCK SERVICE MANUAL...
Page 377: ...ENG IN E 6 41 LIGHT DUTY TRUCK SERVICE MANUAL...
Page 378: ...LIGHT DUTY TRUCK SERVICE MANUAL Fig 37L K Series Engine Front Mount 6 42 ENG INE...
Page 400: ...6 6 4 ENG INE LIGHT DUTY TRUCK SERVICE MANUAL...
Page 401: ...ENG IN E 6 65 LIGHT DUTY TRUCK SERVICE MANUAL...
Page 402: ...6 6 6 ENGINE LIGHT DUTY TRUCK SERVICE MANUAL...
Page 403: ...E NG IN E 6 67 Fig 36V C Series Engine Mounts LIGHT DUTY TRUCK SERVICE MANUAL...
Page 410: ......
Page 423: ...EN G IN E C OOLING 6K 13 Fig 16 Overheating Chart LIGHT DUTY TRUCK SERVICE MANUAL...
Page 424: ...6 K 1 4 ENG INE COOLING Fig 17 Coolant Loss Chart LIGHT DUTY TRUCK SERVICE MANUAL...
Page 456: ...6M 32 ENGINE FUEL Fig K15 Accelerator Controls G Van L 6 LIGHT DUTY TRUCK SERVICE MANUAL...
Page 492: ......
Page 512: ...Fig 18e Vacuum Advance Diagram V8 Engine...
Page 516: ...6 T 2 4 E M IS S IO N CONTROL SYSTEMS LIGHT DUTY TRUCK SERVICE MANUAL...
Page 528: ......
Page 590: ......
Page 593: ...CLUTCHES MANUAL TRANSMISSIONS 7M 3 LIGHT DUTY TRUCK SERVICE MANUAL...
Page 598: ...7M 8 CLUTCHES MANUAL TRANSMISSIONS LIGHT DUTY TRUCK SERVICE MANUAL...
Page 642: ......
Page 654: ......
Page 743: ...FUEL TANKS AND EXHAUST 8 13 LIGHT DUTY TRUCK SERVICE MANUAL...
Page 744: ...8 14 FUEL TANKS AND EXHAUST LIGHT DUTY TRUCK SERVICE MANUAL...
Page 760: ...8 30 FUEL TANKS AND EXHAUST Fig 40 Exhaust Pipe P Models LIGHT DUTY TRUCK SERVICE MANUAL...
Page 761: ...FUEL TANKS AND EXHAUST 8 31 LIGHT DUTY TRUCK SERVICE MANUAL...
Page 763: ...FUEL TANKS AND EXHAUST 8 33 LIGHT DUTY TRUCK SERVICE MANUAL...
Page 766: ......
Page 832: ...LIGHT DUTY TRUCK SERVICE MANUAL Fig 106 Power Steering Pump Mounting Typical 9 66 STEERING...
Page 833: ...PUMP ASSEMBLY STEERING GEAR TYPICAL SMALL V8 TYPICAL LARGE V8 STEERING 9 67...
Page 861: ...STEERING 9 95 Fig 134 Power Steering Pump Leakage LIGHT DUTY TRUCK SERVICE MANUAL...
Page 864: ......
Page 876: ......
Page 886: ...11 10 CHASSIS SHEET METAL LIGHT DUTY TRUCK SERVICE MANUAL...
Page 891: ...ELECTRICAL BODY AND CHASSIS 12 5 LIGHT DUTY TRUCK SERVICE MANUAL...
Page 934: ......
Page 942: ......
Page 970: ......
Page 972: ......
Page 974: ......
Page 976: ...V...
Page 978: ......
Page 979: ......