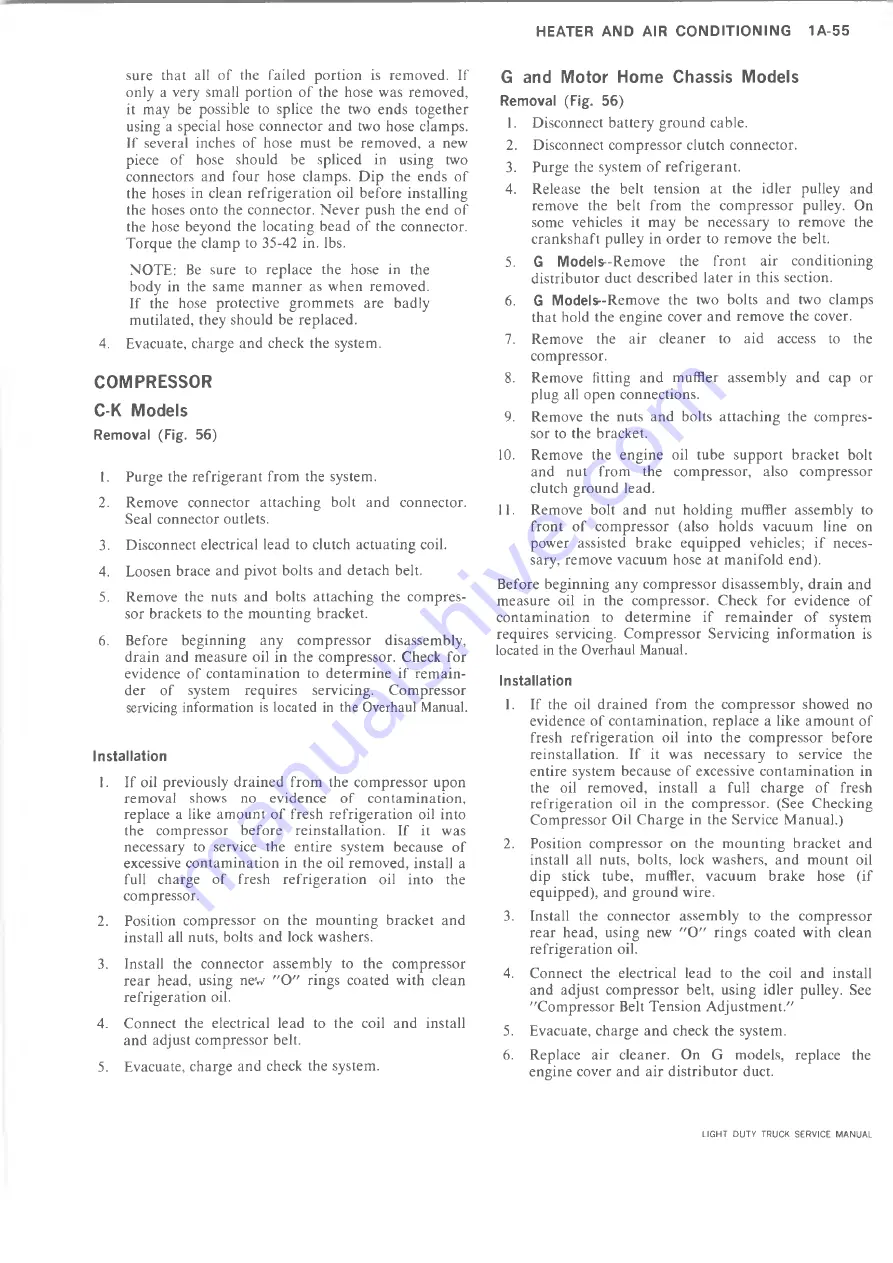
HEATER A N D AIR C O N D I T I O N I N G
1A-55
sure that all of the failed portion is removed. If
only a very small portion of the hose was removed,
it may be possible to splice the two ends together
using a special hose connector and two hose clamps.
If several inches of hose must be removed, a new
piece of hose should be spliced in using two
connectors and four hose clamps. Dip the ends of
the hoses in clean refrigeration oil before installing
the hoses onto the connector. Never push the end of
the hose beyond the locating bead of the connector.
Torque the clamp to 35-42 in. lbs.
NOTE: Be sure to replace the hose in the
body in the same manner as when removed.
If the hose protective grommets are badly
mutilated, they should be replaced.
4. Evacuate, charge and check the system.
COMPRESSOR
C-K Models
Removal (Fig. 56)
1. Purge the refrigerant from the system.
2. Remove connector attaching bolt and connector.
Seal connector outlets.
3. Disconnect electrical lead to clutch actuating coil.
4. Loosen brace and pivot bolts and detach belt.
5. Remove the nuts and bolts attaching the compres
sor brackets to the mounting bracket.
6. Before beginning any compressor disassembly,
drain and measure oil in the compressor. Check for
evidence of contamination to determine if remain
der of system requires servicing. Compressor
servicing information is located in the Overhaul Manual.
Installation
1. If oil previously drained from the compressor upon
removal shows no evidence of contamination,
replace a like amount of fresh refrigeration oil into
the compressor before reinstallation. If it was
necessary to service the entire system because of
excessive contamination in the oil removed, install a
full charge of fresh refrigeration oil into the
compressor.
2. Position compressor on the mounting bracket and
install all nuts, bolts and lock washers.
3. Install the connector assembly to the compressor
rear head, using new "O " rings coated with clean
refrigeration oil.
4. Connect the electrical lead to the coil and install
and adjust compressor belt.
5. Evacuate, charge and check the system.
G and Motor Home Chassis Models
Removal (Fig.
56)
1. Disconnect battery ground cable.
2. Disconnect compressor clutch connector.
3. Purge the system of refrigerant.
4. Release the belt tension at the idler pulley and
remove the belt from the compressor pulley. On
some vehicles it may be necessary to remove the
crankshaft pulley in order to remove the belt.
5.
G
Models-Remove the front air conditioning
distributor duct described later in this section.
6.
G
Models-Remove the two bolts and two clamps
that hold the engine cover and remove the cover.
7. Remove the air cleaner to aid access to the
compressor.
8. Remove fitting and muffler assembly and cap or
plug all open connections.
9. Remove the nuts and bolts attaching the compres
sor to the bracket.
10. Remove the engine oil tube support bracket bolt
and nut from the compressor, also compressor
clutch ground lead.
11. Remove bolt and nut holding muffler assembly to
front of compressor (also holds vacuum line on
power assisted brake equipped vehicles; if neces
sary, remove vacuum hose at manifold end).
Before beginning any compressor disassembly, drain and
measure oil in the compressor. Check for evidence of
contamination to determine if remainder of system
requires servicing. Compressor Servicing information is
located in the Overhaul Manual.
Installation
1. If the oil drained from the compressor showed no
evidence of contamination, replace a like amount of
fresh refrigeration oil into the compressor before
reinstallation. If it was necessary to service the
entire system because of excessive contamination in
the oil removed, install a full charge of fresh
refrigeration oil in the compressor. (See Checking
Compressor Oil Charge in the Service Manual.)
2. Position compressor on the mounting bracket and
install all nuts, bolts, lock washers, and mount oil
dip stick tube, muffler, vacuum brake hose (if
equipped), and ground wire.
3. Install the connector assembly to the compressor
rear head, using new "O " rings coated with clean
refrigeration oil.
4. Connect the electrical lead to the coil and install
and adjust compressor belt, using idler pulley. See
"Compressor Belt Tension Adjustment."
5. Evacuate, charge and check the system.
6. Replace air cleaner. On G models, replace the
engine cover and air distributor duct.
LIGHT DUTY TRUCK SERVICE MANUAL
Summary of Contents for Light Duty Truck 1973
Page 1: ......
Page 4: ......
Page 6: ......
Page 53: ...HEATER AND AIR CONDITIONING 1A 27 LIGHT DUTY TRUCK SERVICE MANUAL...
Page 115: ...LIGHT DUTY TRUCK SERVICE M A N U A L HEATER AND AIR CONDITIONING 1A 89...
Page 123: ...BODY 1B 3 Fig 6 Typical 06 Van LIGHT DUTY TRUCK SERVICE MANUAL...
Page 149: ...BODY 1B 29 Fig 84 Body Mounting 06 Fig 85 Body Mounting 14 LIGHT DUTY TRUCK SERVICE MANUAL...
Page 171: ...LIGHT DUTY TRUCK SERVICE M A N U A L Fig 2 Frame Horizontal Checking Typical FRAME 2 3...
Page 173: ...LIGHT DUTY TRUCK SERVICE M A N U A L Fig 4 10 30 Series Truck Frame FRAME 2 5...
Page 174: ...2 6 FRAME LIGHT DUTY TRUCK SERVICE MANUAL Fig 5 Underbody Reference Points G Van...
Page 185: ...FRONT SUSPENSION 3 11 Fig 16 Toe out on Turns LIGHT DUTY TRUCK SERVICE MANUAL...
Page 224: ......
Page 266: ......
Page 351: ...ENGINE 6 15 Fig ID Sectional View of Eight Cylinder Engine LIGHT DUTY TRUCK SERVICE MANUAL...
Page 375: ...EN G IN E 6 39 LIGHT DUTY TRUCK SERVICE MANUAL...
Page 376: ...6 4 0 ENGINE LIGHT DUTY TRUCK SERVICE MANUAL...
Page 377: ...ENG IN E 6 41 LIGHT DUTY TRUCK SERVICE MANUAL...
Page 378: ...LIGHT DUTY TRUCK SERVICE MANUAL Fig 37L K Series Engine Front Mount 6 42 ENG INE...
Page 400: ...6 6 4 ENG INE LIGHT DUTY TRUCK SERVICE MANUAL...
Page 401: ...ENG IN E 6 65 LIGHT DUTY TRUCK SERVICE MANUAL...
Page 402: ...6 6 6 ENGINE LIGHT DUTY TRUCK SERVICE MANUAL...
Page 403: ...E NG IN E 6 67 Fig 36V C Series Engine Mounts LIGHT DUTY TRUCK SERVICE MANUAL...
Page 410: ......
Page 423: ...EN G IN E C OOLING 6K 13 Fig 16 Overheating Chart LIGHT DUTY TRUCK SERVICE MANUAL...
Page 424: ...6 K 1 4 ENG INE COOLING Fig 17 Coolant Loss Chart LIGHT DUTY TRUCK SERVICE MANUAL...
Page 456: ...6M 32 ENGINE FUEL Fig K15 Accelerator Controls G Van L 6 LIGHT DUTY TRUCK SERVICE MANUAL...
Page 492: ......
Page 512: ...Fig 18e Vacuum Advance Diagram V8 Engine...
Page 516: ...6 T 2 4 E M IS S IO N CONTROL SYSTEMS LIGHT DUTY TRUCK SERVICE MANUAL...
Page 528: ......
Page 590: ......
Page 593: ...CLUTCHES MANUAL TRANSMISSIONS 7M 3 LIGHT DUTY TRUCK SERVICE MANUAL...
Page 598: ...7M 8 CLUTCHES MANUAL TRANSMISSIONS LIGHT DUTY TRUCK SERVICE MANUAL...
Page 642: ......
Page 654: ......
Page 743: ...FUEL TANKS AND EXHAUST 8 13 LIGHT DUTY TRUCK SERVICE MANUAL...
Page 744: ...8 14 FUEL TANKS AND EXHAUST LIGHT DUTY TRUCK SERVICE MANUAL...
Page 760: ...8 30 FUEL TANKS AND EXHAUST Fig 40 Exhaust Pipe P Models LIGHT DUTY TRUCK SERVICE MANUAL...
Page 761: ...FUEL TANKS AND EXHAUST 8 31 LIGHT DUTY TRUCK SERVICE MANUAL...
Page 763: ...FUEL TANKS AND EXHAUST 8 33 LIGHT DUTY TRUCK SERVICE MANUAL...
Page 766: ......
Page 832: ...LIGHT DUTY TRUCK SERVICE MANUAL Fig 106 Power Steering Pump Mounting Typical 9 66 STEERING...
Page 833: ...PUMP ASSEMBLY STEERING GEAR TYPICAL SMALL V8 TYPICAL LARGE V8 STEERING 9 67...
Page 861: ...STEERING 9 95 Fig 134 Power Steering Pump Leakage LIGHT DUTY TRUCK SERVICE MANUAL...
Page 864: ......
Page 876: ......
Page 886: ...11 10 CHASSIS SHEET METAL LIGHT DUTY TRUCK SERVICE MANUAL...
Page 891: ...ELECTRICAL BODY AND CHASSIS 12 5 LIGHT DUTY TRUCK SERVICE MANUAL...
Page 934: ......
Page 942: ......
Page 970: ......
Page 972: ......
Page 974: ......
Page 976: ...V...
Page 978: ......
Page 979: ......