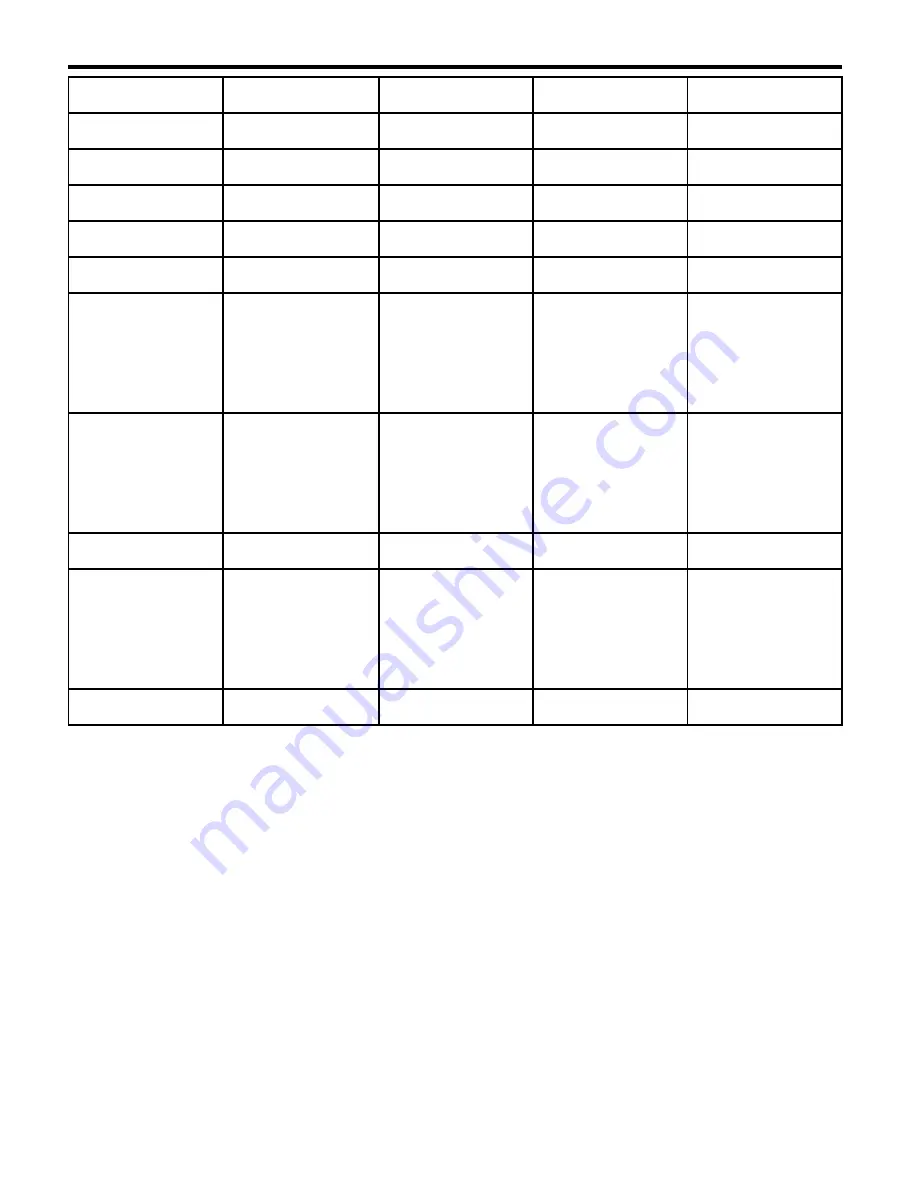
5-12
12 V Starting and Charging
Function
Battery Temperature
Calculation
Battery Voltage
Calculation
Amp-Hour
Calculation
Action Taken
Idle Boost 2 Start
—
Less Than 10.9 V
—
Second level Idle boost
requested
Idle Boost 2 End
—
Greater Than 12 V
Battery has a net loss
less than 0.8 AH
Second level Idle boost
request cancelled
Idle Boost 3 Start
—
—
Battery has a net loss
of 10.0 AH
Third level Idle boost
requested
Idle Boost 3 Start
—
Less Than 10.9 V
—
Third level Idle boost
requested
Idle Boost 3 End
—
Greater Than 12 V
Battery has a net loss
of less than 6.0 AH
Third level Idle boost
request cancelled
Load Shed 2 Start
—
Less Than 10.9 V
Battery has a net loss
greater than 12 AH
Rear Defrost, Heated
Mirrors, Heated Seats
cycled OFF for 50% of
their cycle. The
BATTERY SAVER
ACTIVE message will
be displayed on
the DIC
Load Shed 2 Start
—
Less Than 10.9 V
—
Rear Defrost, Heated
Mirrors, Heated Seats
cycled OFF for 50% of
their cycle. The
BATTERY SAVER
ACTIVE message will
be displayed on
the DIC
Load Shed 2 End
—
Greater Than 12.6 V
Battery has a net loss
of less than 10.5 AH
Clear Load Shed 2
Load Shed 3 Start
—
Less Than 11.9 V
Battery has a net loss
greater than 20 AH
Rear Defrost, Heated
Mirrors, Heated Seats
cycled OFF for 100% of
their cycle. The
BATTERY SAVER
ACTIVE message will
be displayed on
the DIC
Load Shed 3 End
—
Greater Than 12.6 V
Battery has a net loss
of less than 15 AH
Clear Load Shed 3
Starting System Description and
Operation
Starter Motor Operation (Without KL9)
The starter motors are non-repairable. They have pole
pieces that are arranged around the armature. Both
solenoid windings are energized. The pull-in winding
circuit is completed to the ground through the starter
motor. The windings work together magnetically to pull
and hold in the plunger. The plunger moves the shift
lever. This action causes the starter drive assembly to
rotate on the armature shaft spline as it engages with
the flywheel ring gear on the engine. Moving at the
same time, the plunger also closes the solenoid switch
contacts in the starter solenoid. Full battery voltage is
applied directly to the starter motor and it cranks the
engine.
As soon as the solenoid switch contacts close, current
stops flowing thorough the pull-in winding because
battery voltage is applied to both ends of the windings.
The hold-in winding remains energized. Its magnetic
field is strong enough to hold the plunger, shift lever,
starter drive assembly, and solenoid switch contacts in
place to continue cranking the engine. When the
engine starts, pinion overrun protects the armature from
excessive speed until the switch is opened.
When the crank signal is removed, the starter relay
opens and battery voltage is removed from the starter
solenoid S terminal. Current flows from the motor
contacts through both windings to the ground at the end
of the hold-in winding. However, the direction of the
current flow through the pull-in winding is now opposite
the direction of the current flow when the winding was
first energized.
The magnetic fields of the pull-in and hold-in windings
now oppose one another. This action of the windings,
along with the help of the return spring, causes the
starter drive assembly to disengage and the solenoid
switch contacts to open simultaneously. As soon as the
contacts open, the starter circuit is turned off.
2021 - Silverado 4500HD, 5500HD, and 6500HD Electrical Body Builder Manual