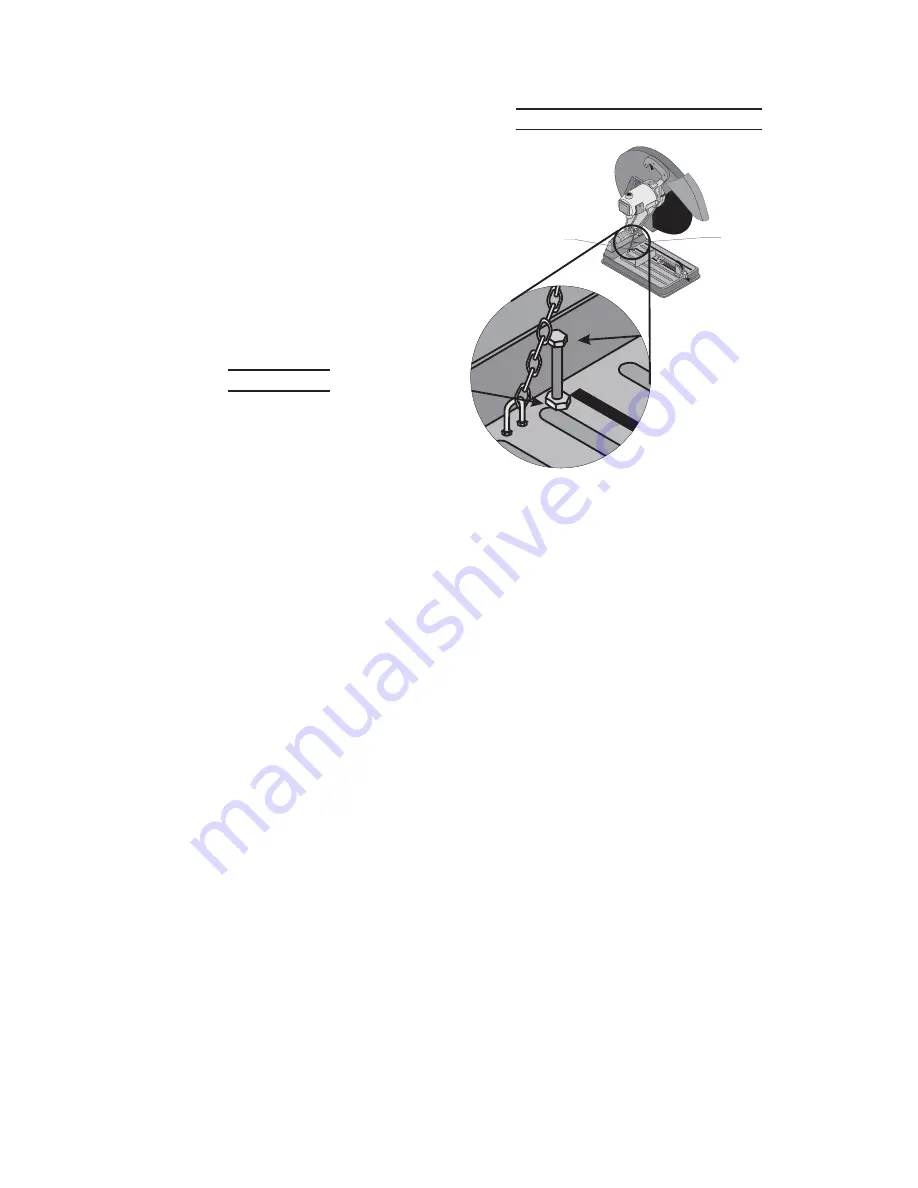
SKU 1624
for technical questions, please call 1-800-444-3353.
Page 8
VISE STOP (#69) to the desired posi-
tion. Tighten the BOLTS.
Raise the VISE LEAD SCREW RE-
3.
LEASE HANDLE (#89) and slide
the VISE FACE (#67) forward until it
contacts the stock.
Lower the RELEASE HANDLE
4.
so that it rests against the LEAD
SCREW (#81). Turn the VISE HAN-
DLE (#92) to tightly clamp the stock.
miter Cuts
Position stock as detailed in Step 1 of
1.
Vise Assembly Operation, above.
Position the VISE STOP (#69) as
2.
detailed in Step 2. Before tightening
the BOLTS (#68), position the VISE
STOP to the desired angle (from –30°
to +45°).
Advance the VISE FACE (#67) as de-
3.
tailed in Steps 3 & 4. The FACE will
adjust to the angle of your stock.
depth of Cut adjustment
set Bolt
depth
adjustment
Bolt
Figure 4 -- Adjusting Depth of Cut
1. Loosen the Set Nut on the Depth Ad-
justment Bolt as shown in Figure 4.
Raise or lower the Depth Adjustment
2.
Bolt as necessary to obtain the de-
sired depth of cut.