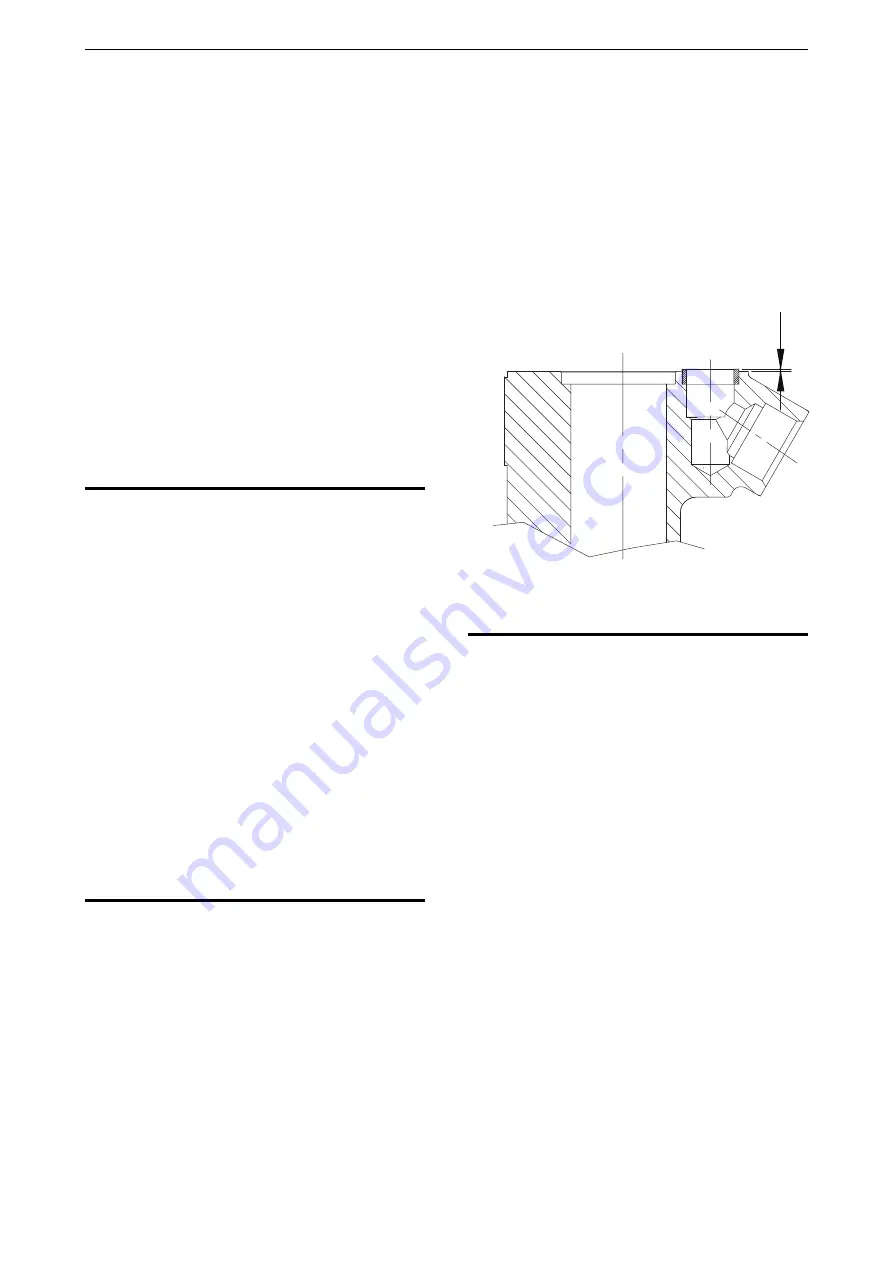
♦
Before starting maintenance on the machine,
clean it in order to avoid exposure to hazardous
substances. See “Dust and fume hazards”
♦
Use only authorised parts. Any damage or
malfunction caused by the use of unauthorised
parts is not covered by warranty or product
liability.
♦
When cleaning mechanical parts with solvent,
comply with appropriate health and safety
regulations and ensure there is satisfactory
ventilation.
♦
For major service of the machine, contact the
nearest authorised workshop.
♦
After each service, check that the machine's
vibration level is normal. If not, contact the nearest
authorised workshop.
Every day
Before undertaking any maintenance on pneumatic
machines, always switch off the air supply and bleed
the machine by depressing the start and stop device.
Then disconnect the air hose from the machine.
♦
Clean and inspect the machine and its functions
each day before the work commences.
♦
Conduct a general inspection for leaks and
damage.
♦
Check that the air inlet nipple is tightened and
that the claw coupling is free from damage.
♦
Change damaged parts immediately.
♦
Replace worn components in good time.
♦
Make sure that all the attached and related
equipment, such as hoses, water separators, and
oilers are properly maintained.
Assembly instructions
Reasonable care must be taken during assembly and
disassembly of the tool to avoid burring, scoring or
distortion of closely fitting precision built parts.
1. Check all metal to metal surfaces for nicks and
burrs before and during assembly.
2. Before re-assembly, lubricate all O-rings and coat
all moving parts of tool with recommended
lubricants.
3. During assembly take care to keep dirt out of
tool, particularly between mating surfaces.
4. The front head bolts must be tightened so that
the springs or bushings are evenly compressed.
5. When assembly is complete pour about ½ oz.
(1.5cl) of the recommended oil into the air inlet
and operate the pneumatic spike driver at
reduced throttle for 10–15 seconds. When
operating the pneumatic spike driver on the
floor, do so at reduced throttle to avoid damage
to piston, anvil block, and front head.
6. Before assembling the back head onto the
cylinder, check that the seal protrudes
approximately (B)
1
⁄
16
in. (1.6 mm) from the face
of the cylinder.
B
Periodic maintenance
After each operating period of approximately 150
impact hours or twice a year the machine must be
dismantled and all parts be cleaned and checked.
This work must be performed by authorized staff,
trained for this task.
1. Be sure that mating surfaces are clean and
smooth and that the bolts are tight.
2. Thoroughly clean and inspect internal parts and
make sure they are free from rust, grit and
foreign matter.
3. Thoroughly clean and inspect valve parts. Be
sure that the valve moves freely.
9800 0555 90a | Original instructions
14
CP 1230 SPDR, CP 1240 SPDR
Safety and operating instructions
www.CrowderSupply.com • Toll Free: 888-883-5144
Crowder
Supply
Co.,
Inc.
• 8495
Roslyn
St.,
Commerce
City,
CO
80022
• Toll
Free:
888-883-5144
• www.CrowderSupply.com