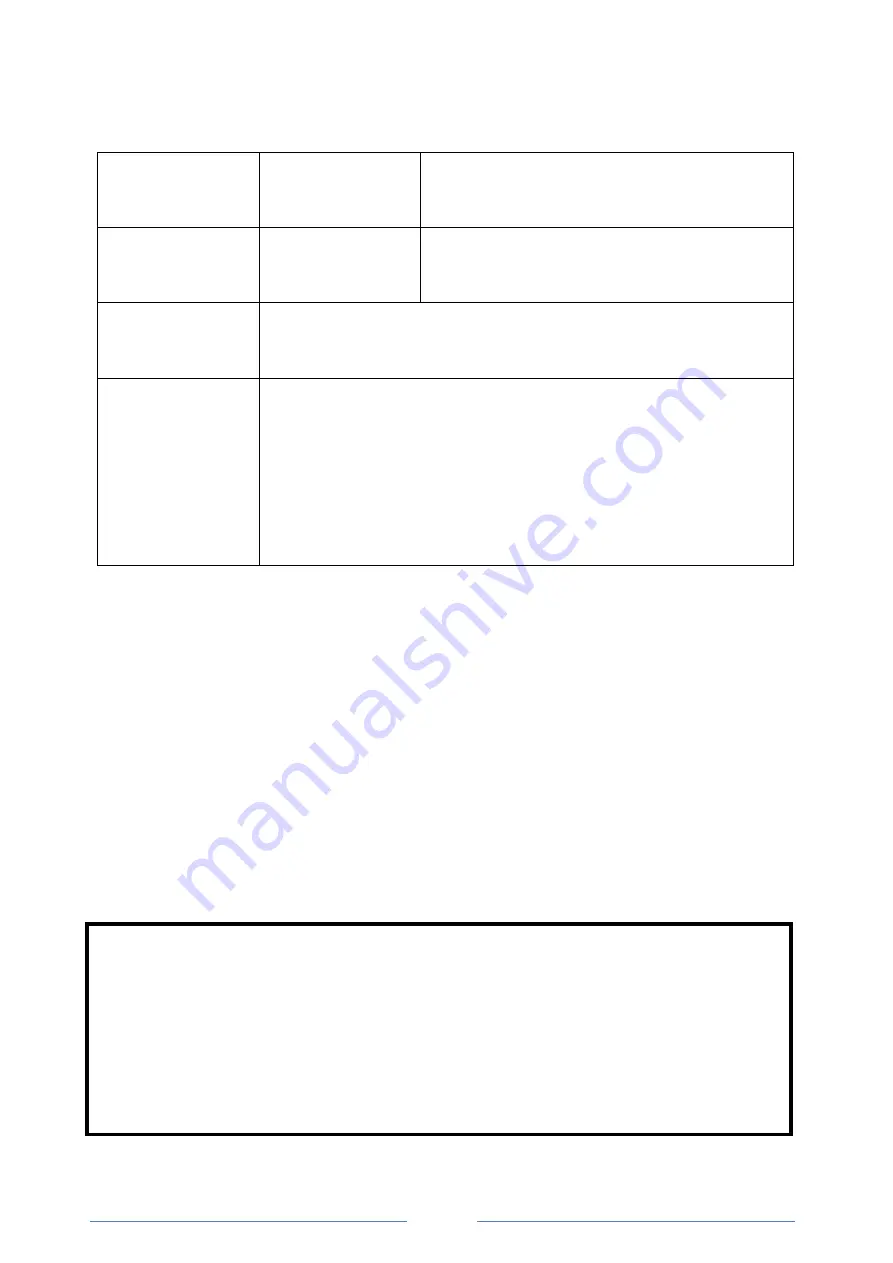
チコーエアーテック株式会社
Copyright CHIKO AIRTEC CO., LTD. 2009
20
お買い上げメモ
Memo about purchase
形 式
Model
製造番号
Manufacturer
’s serial number:
購入年月日
Date of purchase
運転開始日
年
月
Start of operation
お客様お名前
Your name
住所
Address:
電話
Phone :
担当者
Person in charge
チコーエアーテック株式会社
CHIKO AIRTEC CO., LTD.
〒562-0012 大阪府箕面市白島 2-27-24
2-27-24 Hakushima, Minoh City Osaka Japan 562-0012
TEL (81) 072-720-5151 FAX (81) 072-720-5133