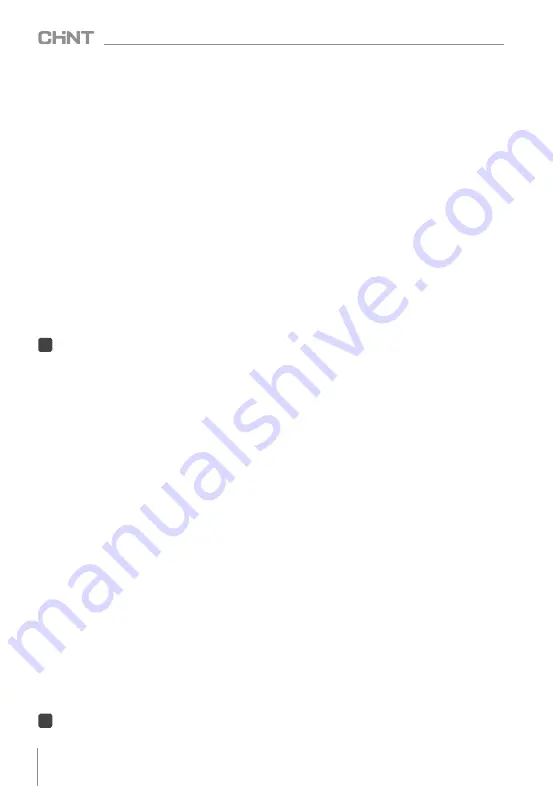
05
NWC1 Series Self-healing Low Voltage Shunt Capacitors
6
.
5
.
1
User
should
check
the
operating
status
of
the
capacitors
on
a
regular
basis
,
check
if
the
3
-
phase
current
is
balanced
by
using
the
amperemeter
in
the
cabinet
.
6
.
5
.
2
If
the
3
-
phase
current
is
not
balanced
,
use
clamp
on
amperemeter
to
test
the
current
and
voltage
of
phase
A
,
phase
B
and
phase
C
of
each
group
of
capacitors
.
6
.
5
.
3
If
there
is
voltage
but
no
current
between
phases
,
it
means
the
overpressure
protector
is
disconnected
,
user
should
maintain
the
product
in
time
or
replace
it
if
necessary
.
6
.
5
.
4
Check
the
surface
temperature
of
capacitor
case
during
operation
,
if
the
temperature
of
any
individual
capacitor
case
exceeds
65
℃,
maintain
the
product
or
replace
it
if
necessary;
if
the
temperature
of
all
the
capacitor
cases
is
higher
than
65
℃,
take
effective
ventilation
and
heat
dissipation
measures
and
check
if
any
harmonic
source
device
(
such
as
frequency
converter
,
rectifier
and
inverter
,
and
medium
and
high
frequency
heating
furnace
)
is
used
at
user
load
end
.
6
.
6
Operation
procedure
,
method
and
precautions
for
shut
down
6
.
6
.
1
If
any
deformation
,
oil
leakage
is
found
on
the
capacitor
case
or
the
reactive
compensation
controller
is
not
working
normally
,
shut
down
the
equipment
for
inspection
and
repair
.
6
.
6
.
2
If
the
busbar
in
the
cabinet
is
of
bottom
-
in
and
top
-
out
type
,
user
must
disconnect
the
bus
before
replacing
the
capacitors
or
other
electric
components
.
However
,
user
only
needs
to
disconnect
the
isolation
switch
in
the
cabinet
when
changing
the
secondary
wiring
or
testing
the
capacitors
.
6
.
6
.
3
Before
testing
and
touching
the
capacitors
,
user
must
conduct
short
circuit
discharge
between
each
two
terminals
of
the
3
-
phase
capacitor
.
7
Maintenance
and
Storage
7
.
1
Daily
maintenance
and
calibration
Check
if
the
operating
current
of
the
capacitor
is
normal
by
using
the
amperemeter
and
compensation
controller
in
the
cabinet
.
Check
if
there
is
any
deformation
,
oil
leakage
and
overheating
.
Abnormalities
such
as
overcurrent
and
overtemperature
caused
by
harmonic
will
reduce
the
service
life
of
the
capacitor
and
can
cause
damage
to
other
components
and
conductors
in
the
cabinet
due
to
overload
.
7
.
2
Maintenance
during
operation
Tighten
the
terminal
screws
of
the
capacitor
on
a
regular
basis
(
once
half
a
year
)
to
prevent
poor
contact
.
Remove
dust
and
greasy
dirt
also
.
User
should
pay
close
attention
to
the
cabinet
and
replace
any
damaged
capacitor
in
time
if
any
under
-
compensation
of
power
factor
occurs
due
to
significant
capacitance
drop
(
50
%
current
decrease
),
otherwise
it
may
lead
to
penalty
.
If
all
the
capacitors
are
operating
and
in
good
condition
but
the
power
factor
still
cannot
meet
requirement
,
user
must
add
capacity
in
time
to
ensure
the
automatic
cycle
operation
of
the
capacitors
.
7
.
3
Service
cycle
User
should
determine
the
service
cycle
based
on
the
application
conditions
,
the
recommended
service
cycle
for
cabinet
is
once
half
a
year
.
7
.
4
Maintenance
for
long
-
term
idle
If
the
capacitor
has
been
idled
for
one
year
or
longer
,
please
check
if
its
capacitance
value
is
within
the
allowable
deviation
range
(-
5
%~+
8
%);
conduct
pole
-
to
-
case
voltage
withstand
test
again
(
apply
AC
3kV
for
5
seconds
);
or
use
megameter
to
test
if
the
insulation
resistance
between
the
three
phase
terminals
and
the
case
is
larger
than
100M
Ω
before
using
the
product
.
7
.
5
Storage
conditions
,
storage
period
and
precautions
The
smart
capacitor
should
be
stored
in
a
dry
and
well
ventilated
room
and
protected
from
rain
,
moist
,
chemicals
and
dust
.
The
maximum
storage
period
of
the
product
is
36
months
.
Do
not
put
the
smart
capacitor
or
its
package
directly
on
the
floor
.
8
Analysis
and
Troubleshooting
of
Faults