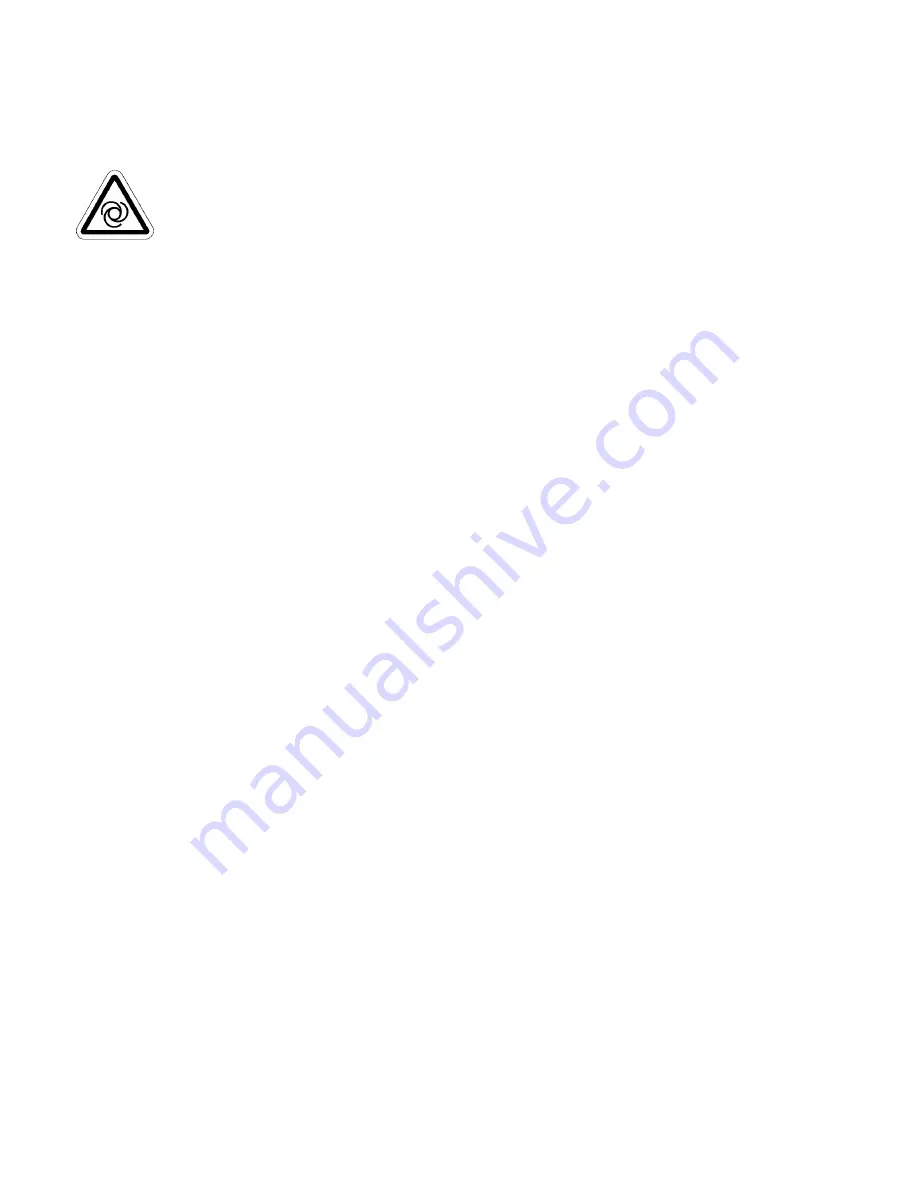
ChipBLASTER Inc
20
12.0.
OPERATION:
12.1. ELECTRICAL OPERATION:
12.1.1. Energizing CR1 will start the coolant system and provide pressurized coolant to
outlet #1. At this time the main motor and return pump motor will come on line.
12.2. COOLANT FLOW
(Refer to figure 1)
12.2.1. Coolant flow is divided into two groups, High-pressure and Low-pressure. Low-
pressure is the flow of coolant from the machine sump, through the
ChipBLASTER return pump to the high-pressure pump. High-pressure is the flow
of coolant from the high-pressure pump to the nozzle outlet or tool, at the
machining center.
12.2.2. LOW-PRESSURE – Low-pressure coolant enters the return pump, is pumped
through the filter and goes to the high-pressure pump inlet. Filter pressure gauges
are located at the inlet and outlet of the filters. They provide a visual indication of
dirty filter condition. When the outlet gauge reading drops to 1 bar (15 psig), the
alarm horn will sound to indicate the filter cartridge is dirty and should be
replaced. Two pressure switches are located between the filters and the high-
pressure pump inlet. 2PS closes at 1 bar (15 psi) falling, for dirty filter contact to
the alarm horn / machine center. When utilizing this contact in the machine
center control, be aware that a time delay is required to allow system pressure to
build and open the contact. 1PS closes at 0.7 bar (10 psi) falling, for dirty filter
contact to the fault (error signal) relay.
12.2.3. HIGH-PRESSURE - High-pressure coolant leaving the pump goes to the
manifold block, which contains a regulator and solenoid valve. The regulator is
adjustable to relieve coolant at the system operating pressure. The regulator
protects the high-pressure coolant system from over pressure condition. Relieved
coolant is returned to the inlet of the return pump. Upon activation of coolant on
relay, CR1, the normally open solenoid (dump) valve is activated and allows
coolant to pressurize the high-pressure hose leading to the machine center. The
normally open solenoid valve is also used to bypass coolant to the return pump
inlet when the index control relay, CR3, is energized. Thus relieving pressure in
the high-pressure hose leading to the machine center. A pressure gauge is
installed to read the overall pressure between the high-pressure pump and the
nozzle outlet at the machining center. High-pressure coolant leaves the manifold
block and flows through the high-pressure hose to the machining center and on to
the tool being used.
12.2.4.
LOW PRESSURE FLOOD
is a factory installed feature. It is designed to be
used to supply filtered coolant at 5 gpm (18.9 liters/minute) 35 psig (2.4bar)
maximum.
The flow and pressure is dependent
on orifice diameter.
The low
pressure flood is controlled by a separate maintained “M” code from the machine
tool. The low pressure, as supplied from the factory, is available at coolant outlet
number 1 and/or 2, depending on ChipBLASTER model. The low pressure flood
is used to flush parts, tool plates and general chip clearing.
NOTE: If the low pressure flood coolant is in use; high pressure coolant is
not available.