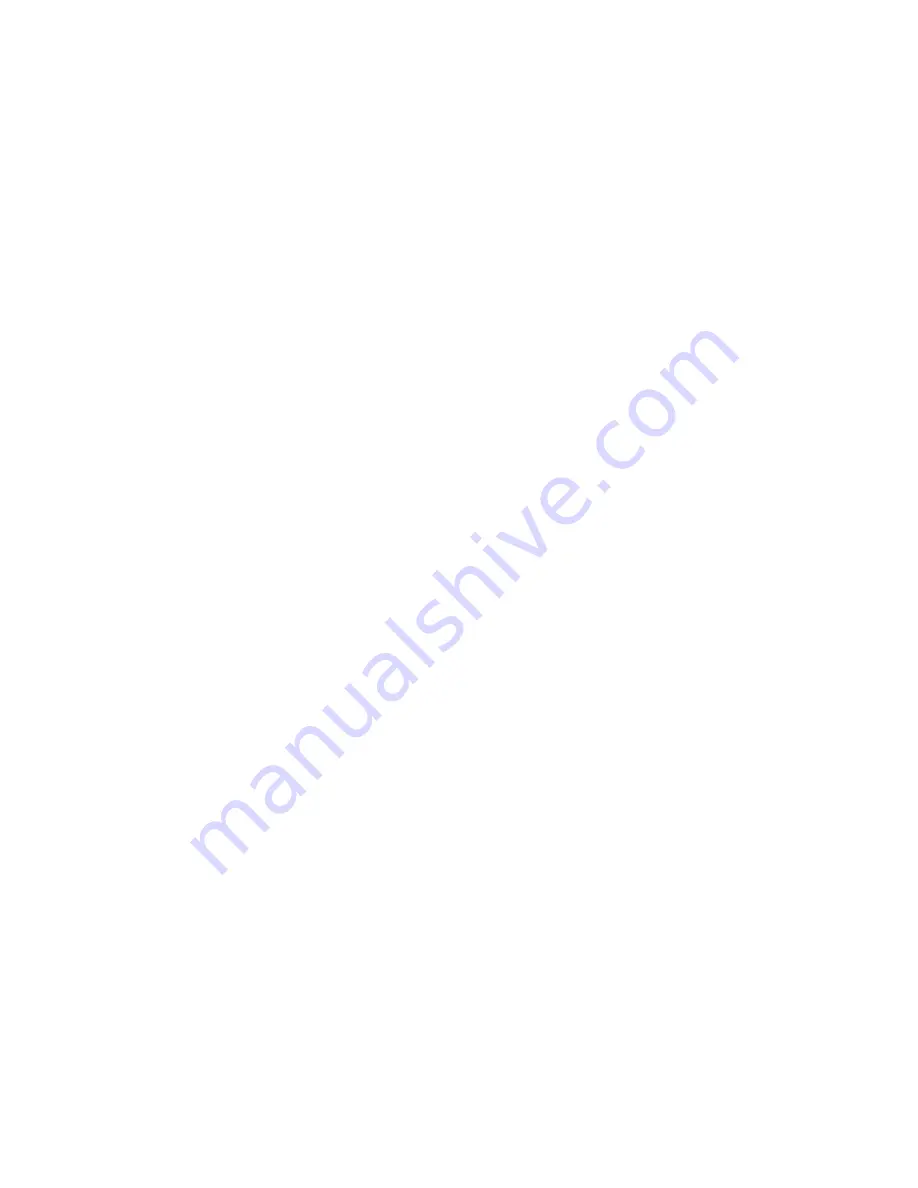
EN - 20
If the system needs to be opened just after shutting down the
compressor, e.g. to clean the oil strainer, be sure to let the oil
cool down for long enough so that any oil splashes no longer
pose any hazard.
A temperature of less than 35°C is recommended.
- Containers must be stored with their caps on. Avoid using oil
from an opened container stored under incorrect conditions.
20.1.4 Refrigerants - general information
-
Always remember that refrigeration systems contain
pressurised liquids and vapours.
- All necessary measures must be taken when partially opening
the system: Make sure that there is no pressure in the part of
the circuit concerned.
- Partial opening of the primary refrigerant circuit will cause
a certain quantity of refrigerant to be released into the
atmosphere.
- It is essential to keep the amount of lost refrigerant as low
as possible by pumping the charge and isolating it in another
part of the system.
- The refrigerant and lubricating oil, and the low-temperature
liquid refrigerant in particular, may cause inflammatory
lesions similar to burns if they come into contact with the skin
or eyes.
Always wear protective eyewear, gloves and other protective
equipment when opening pipes or tanks liable to have
liquids in them. Store unused refrigerant in the appropriate
containers and limit the amounts stored in mechanical rooms.
- Cylinders and tanks of refrigerant must be handled with care
and signs warning users of the related poisoning, fire and
explosion hazards must be clearly visible. Refrigerant that
reaches the end of its life must be collected and recycled in
accordance with applicable regulations.
20.1.5 Halocarbon and hydrofluorocarbon refrigerants
Although non-toxic, vapours from halocarbon and
hydrofluorocarbon refrigerants are still hazardous because
they are heavier than air and can force the latter out of the
machine rooms.
If refrigerant is accidentally released, ventilate the room with
fans. Workplace exposure levels must be kept to a practical
minimum, and must never exceed the recognised threshold of
1000 ppm (particles per million) for an 8-hour working day and
a 40-hour working week.
Although halocarbon and hydrofluorocarbon refrigerants are not
flammable, keep them away from open flames (e.g. cigarettes,
etc.), as temperatures of over 300°C cause their vapours to
break down and form phosgene, hydrogen fluoride, hydrogen
chloride and other toxic compounds. These compounds may
produce severe physiological consequences if accidentally
inhaled or swallowed.
20.1.6 Servicing
- For units used seasonally, note down the operating readings
and perform the checks indicated in the table in section
20 Servicing and maintenance, at least twice a year and
systematically whenever the unit is activated.
● Weekly checks
With the unit running at full capacity, check the following
values:
- Check the entire installation for traces of water or oil under or
around the unit, and for any unusual noises.
- LP compressor suction pressure,
- HP compressor discharge pressure,
-
The water inlet and outlet temperatures in
the exchangers
- The charge via the liquid sight glass and the condition of the
charge using the coloured indicator on the sight glass
- The oil level and its appearance. If the colour changes, check
the quality.
- Keep the unit clean
- Also check whether the safety devices operate correctly.
● Monthly checks
- Check all the values listed in the "Operating readings" table
on the previous page.
- Perform a corrosion check on all the metal parts. (Frame,
casing, exchangers, electrical boxes etc.)
- Make sure that the insulating foam is not detached or torn.
- Check the energy transfer fluids for any impurities which
could cause wear or corrosion in the exchanger.
- Check the circuits for leaks.
- Check whether the safety devices and the expansion valve(s)
operate correctly
● Annual checks
-
Carry out the same inspections as during
the monthly checks.
- Check the evaporator pressure drop (re-check after any
cleaning).
- Check the sealing of the compressor/separator discharge
check valve, and clean or replace the valve if necessary.
- Test the oil for contaminants (annually or every 5000 hours):
If acid, water or metal particles are detected, replace the oil
in the corresponding circuit and the dryer.
- If the whole oil load is being changed, use only new oil of the
same grade as the original oil, which has been stored in a
hermetically sealed container until loading. (see section 12
Main components of the refrigerating circuit).
- Check the filter dryer for clogging (measure the difference
in the temperature of the pipes at the dryer inlet and outlet).
- Check the electrical connections to ensure they are tight and
in good condition.
-
Check the insulation of the motor and the resistance
of the coils.
- Clean the water filter and vent air from the circuit.
- Clean the exchangers and check the pressure drop in each.
- Check the operation of the water flow switch.
- Check the water quality or condition of the coolant.
- Check the antifreeze concentration (MEG or PEG)
- Check the electrical box for water seepage.
- Check the condition of the contacts and the current at full load on
all three phases.
- Disconnect all the cables.
NB: The cleaning intervals are given as a guide and should be
adapted to each installation.
20.1.7 Disassembling the compressor
The compressor is fastened to the platform by 4 screws
with diameter 16 or 20 mm, according to the compressor size.
Warning:
Do not tighten the compressor screws to a torque
greater than 13 Nm ± 1 for HYDROCIAT LW and LWP. If you
do not have a torque wrench, tighten them until they are snug
then tighten a further ¾ turn.
IMPORTANT:
To ensure your unit runs smoothly and to obtain service
under the warranty, take out a maintenance contract with
your installer or an approved maintenance company.
Summary of Contents for HYDROCIAT 1800BX
Page 1: ...Instruction manual 01 2015 NA 01 29 I version B HYDROCIAT LW LWP...
Page 2: ......
Page 27: ......