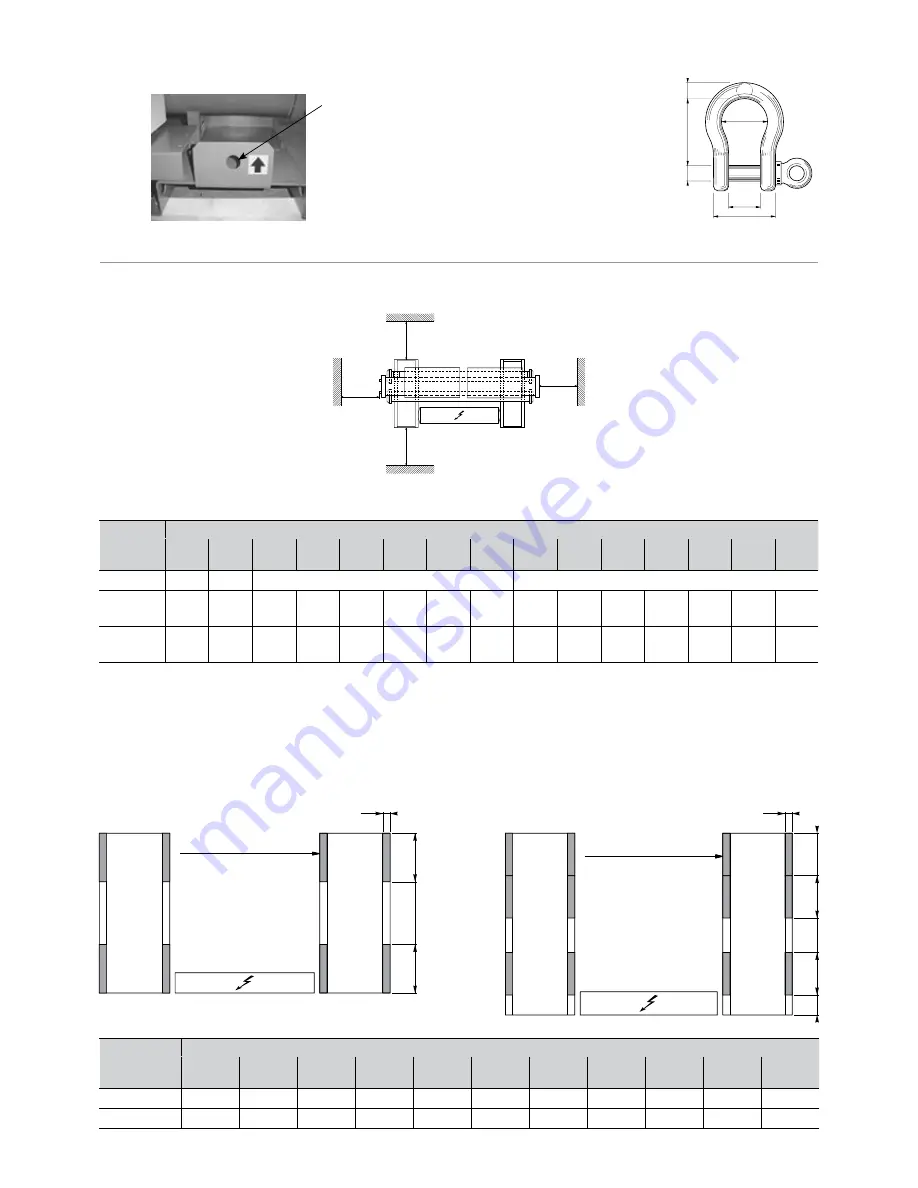
EN - 4
9 - INSTALLING THE UNIT
9.1 Dimensions and weight
Dimensions and clearance required for servicing the unit (see dimensional drawing supplied with the unit)
.
1
m
1
m
X (m)
X (m)
min.
min.
Clearance X required on just one side, opposite 1 m
9.2 Anti-vibration mounts
(Supplied as an option)
Anti-vibration mounts must be installed beneath the unit in the case of applications with extremely low vibrations.
The mounts must be placed at the locations illustrated below.
HYDROCIAT
LW - LWP
1800BX 1800BX
HPS
2150BX 2150BX
HPS
2500BX 2500BX
HPS
2800BX 2800BX
HPS
3050BX
HPS
3500BX
HPS
3600BX
HPS
3900BX
HPS
4200BX
HPS
4500BX
HPS
4800BX
HPS
X (metres)
3
3.5
4
Weight
(empty)
Kg
3130
3150
3520
3540
3830
3850
3840
3860
4691
4759
5106
5274
5293
5342
5362
Weight in
operation
Kg
3360
3380
3800
3820
4110
4130
4120
4140
5064
5275
5502
5812
5820
5905
5925
HYDROCIAT
LW - LWP
1800BX
(HPS)
2150BX
(HPS)
2500BX
(HPS)
2800BX
(HPS)
3050BX
HPS
3500BX
HPS
3600BX
HPS
3900BX
HPS
4200BX
HPS
4500BX
HPS
4800BX
HPS
A
520
520
520
520
155
125
195
155
165
165
165
B
-
-
-
-
283
313
243
283
273
273
273
8.1 Detailed view of the anchorage point for
handling
Ø see table, chapter 8
Handling and positioning
8.2 Type of shackle recommended for
handling the unit
We recommend using shackles to
handle the unit.
STAS shackle
- Forged steel bow shackle with pin
- STAS code: 130M
- Working load limit: 4000 kg
30
60
30
120
13
0
90
SYLOMER P 350 x 50 x 25
350
350
AB
350
50
SYLOMER P 400 x 70 x 25
400
A
400
70
LW - LWP
1800BX - 2150BX - 2500BX - 2800BX - 1800BX (HPS) -
2150BX (HPS) - 2500BX (HPS) - 2800BX (HPS)
LW - LWP
3050BX (HPS) - 3500BX (HPS) - 3600BX (HPS) - 3900BX (HPS)
4200BX (HPS) - 4500BX (HPS) - 4800BX (HPS)
Summary of Contents for HYDROCIAT 1800BX
Page 1: ...Instruction manual 01 2015 NA 01 29 I version B HYDROCIAT LW LWP...
Page 2: ......
Page 27: ......