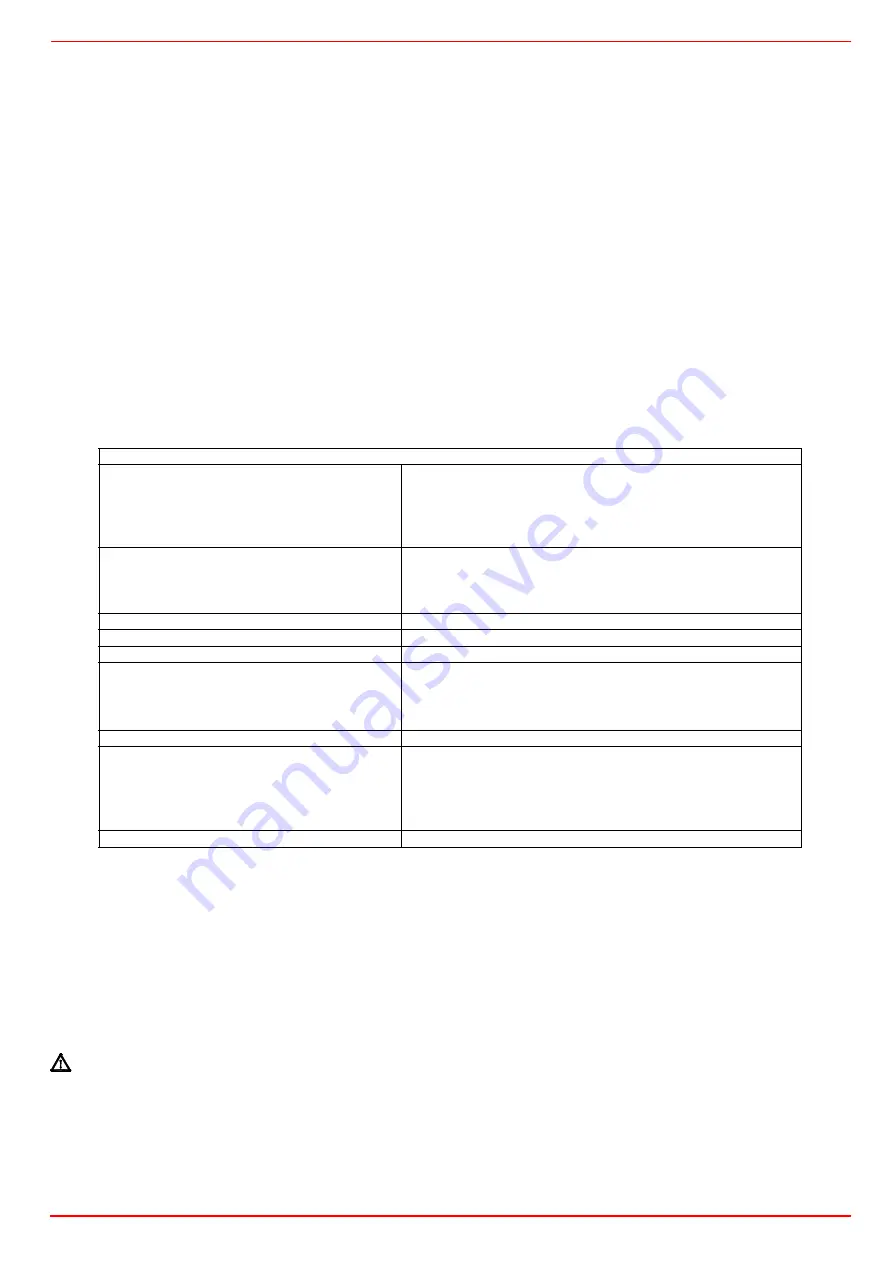
CONTROL PROGRAM IN THE EVENT OF FAULT
z
If a fault occurs, all outputs will immediately be deactivated (in less
than 1s).
z
After an interruption of power, a restart will be made with the full pro-
gram sequence.
z
If the operating voltage drops below the undervoltage thresold, a
safety shutdown is performed.
z
If the operating voltage exceeds the undervoltage thresold, a restart
will be performed.
z
In case of extraneous light during “t1”, a lockout occurs.
z
In case of extraneous light during “tw”, there is a prevention of startup
and a lockout after 30 seconds.
z
In case of no flame at the end of TSA, there will be max. 3 repetitions
of the startup cycle, followed by a lockout at the end of TSA, for mod.
LME11..; directly a lockout at the end of TSA for LME21-22 models.
z
For LME11 model: if a loss of flame occurs during operation, in case of
an establishment of flame at the end of TSA, there will be max. 3 repeti-
tions, otherwise a lockout will occur.
z
For LME21-22 models: if a loss of flame occurs during operation, there
will be a lockout.
z
If the contact of air pressure monitor LP is in working position, a pre-
vention of startup and lockout after 65 seconds will occur.
z
IIf the contact of air pressure monitor LP is in normal position, a
lockout occurs at the end of t10.
z
If no air pressure signal is present after completion of t1, a lockout will
occur.
CONTROL BOX LOCKED
In the event of lockout, the LME.. remains locked and the red signal lamp
(LED) will light up.The burner control can immediately be reset. This state
is also mantained in the case fo mains failure.
DIAGNOSITICS OF THE CASUE OF FAULT
z
Press the lockout reset button for more than 3 seconds to activate the
visual diagnostics.
z
Count the number of blinks of the red signsl lamp and check the fault
condition on the “Error code table” (the device repeats the blinks for
regular intervals).
During diagnostics, the control outputs are deactivated:
- the burner remains shut down;
- external fault indication is deactivated;
- fault status is showed by the red LED, inside the LME’s lockout reset
buttonaccording to the “Error code table”:
RESETTING THE BURNER CONTROL
When lockout occurs, the burner control can immediately be reset, by
pressing the lockout reset button for about 1..3 seconds. The LME.. can
only be reset when all contacts in the line are closed and when there is no
undervoltage.
LIMITATION OF REPETITIONS (only for LME11.. model)
If no flame is established at the end of TSA, or if the flame is lost during
operation, a maximum of 3 repetitions per controller startup can be perfor-
med via “R”, otherwise lockout will be initiated. Counting of repetitions is
restarted each time a controlled startup via “R” takes place.
Condensation, formation of ice and ingress of water are not
permitted!
TECHNICAL CHARACTERISTICS
Mains voltage
120V AC +10% / -15%
230V AC +10% / -15%
Frequency
50 ... 60 Hz +/- 6%
Power consumption
12VA
External primary fuse
max. 10 A (slow)
input current at terminal 12
max. 5 A
Detection cable length
max. 3m (for electrode)
Detection cable length
max. 20 m (laid separately, for QRA probe)
Reset cable length
max. 20 m (posato separatamente)
Term. 8 & 10 cable length
max. 20 m
Thermostat cable length
max. 3 m
and other terminals
Safety class
I
Index of protection
IP40 (to be ensured during mounting)
Operating conditions
-20... +60 °C, < 95% UR
Storage conditions
-20... +60 °C, < 95% UR
Weight
approx. 160 g
ERROR CODE TABLE
2 blinks **
No establishment of flame at the end of TSA
- Faulty or soiled fuel valves
- Faulty or soiled flame detector
- Inadequate adjustement of burner, no fuel
- Faulty ignition equipment
3 blinks ***
The air pressure switch does not switch or remains in idle position:
- LP is faulty
- Loss of air pressure signal after t10
- LPis welded in normal position.
4 blinks ****
- Extraneous light when burner starts up.
5 blinks *****
- LP is working position.
6 blinks *****
Free.
7 blinks *******
Loss of flame during operation
- Faulty or soiled fuel valves
- Faulty or soiled flame detector
- Inadequate adjustement of burner
8 ÷ 9 blinks
Free
10 blinks **********
Faulty output contacts
Attention: “lockout” remote signal (terminal no. 10) not enabled
- Wiring error
- Anomalous voltage on ouput terminals
- Other faults
14 blinks ************** (only for LME4x)
- CPI contact (gas valve microswitch) not closed.
Summary of Contents for IDEA NG280
Page 45: ...C I B UNIGAS M039132CD 45...