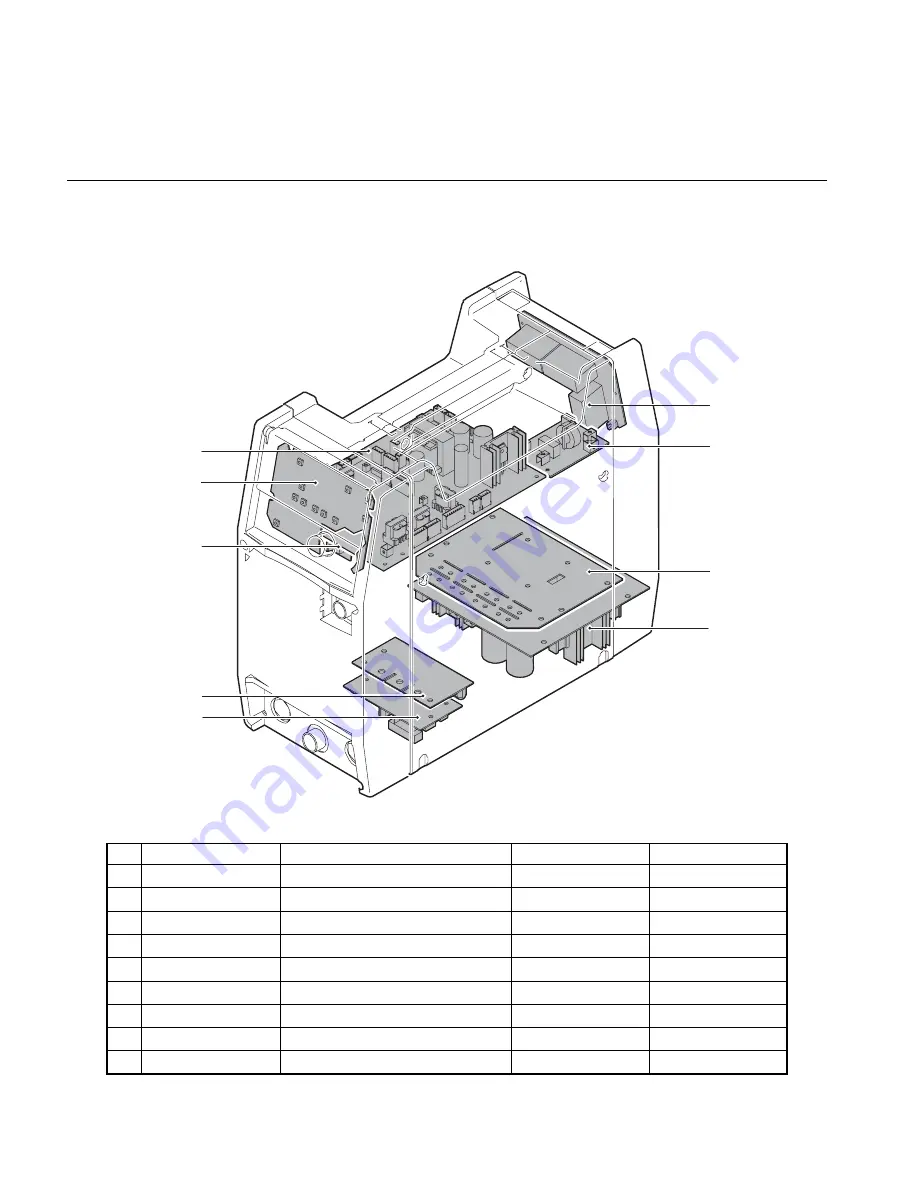
13 MAINTENANCE
MAINTENANCE
1
Maintenance List
8
9
1
4
5
2
3
6
7
No.
DWG No.
Parts name
Reference page
Part No.
1
PCB3
Print Circuit Board (WK-5548)
13-9
2
PCB10
Print Circuit Board (WK-5527)
13-13
3
PCB11
Print Circuit Board (WK-5528)
13-13
4
PCB12
Print Circuit Board (WK-5615)
13-15
5
PCB13
Print Circuit Board (WK-5569)
13-18
6
PCB14
Print Circuit Board (WK-5570)
13-19
7
PCB16
Print Circuit Board (WK-5499)
13-19
8
PCB17
Print Circuit Board (WK-4917)
13-20
9
PCB18
Print Circuit Board (WK-5861)
13-21
SERVICE MANUAL
TRANSTIG 200 AC/DC
January 17, 2008
13-1
W7001314
W7001812
W7001320
W7001594
W7001433
W7001434
W7001324
10-6740
W7001602
Summary of Contents for TRANSTIG 200 AC/DC
Page 8: ...THIS PAGE LEFT INTENTIONALLY BLANK ...
Page 20: ...TRANSTIG 200 AC DC SERVICE MANUAL 2 6 January 17 2008 NOTES ...
Page 34: ...5 2 January 17 2008 TRANSTIG 200 AC DC SERVICE MANUAL NOTES ...
Page 58: ...January 17 2008 11 2 TRANSTIG 200 AC DC SERVICE MANUAL NOTES ...
Page 74: ...TRANSTIG 200 AC DC SERVICE MANUAL January 17 2008 12 16 THIS PAGE LEFT INTENTIONALLY BLANK ...
Page 111: ...THIS PAGE LEFT INTENTIONALLY BLANK SERVICE MANUAL TRANSTIG 200 AC DC January 17 2008 13 37 ...
Page 122: ...A 11 January 17 2008 TRANSTIG 200 AC DC SERVICE MANUAL NOTES ...
Page 126: ......