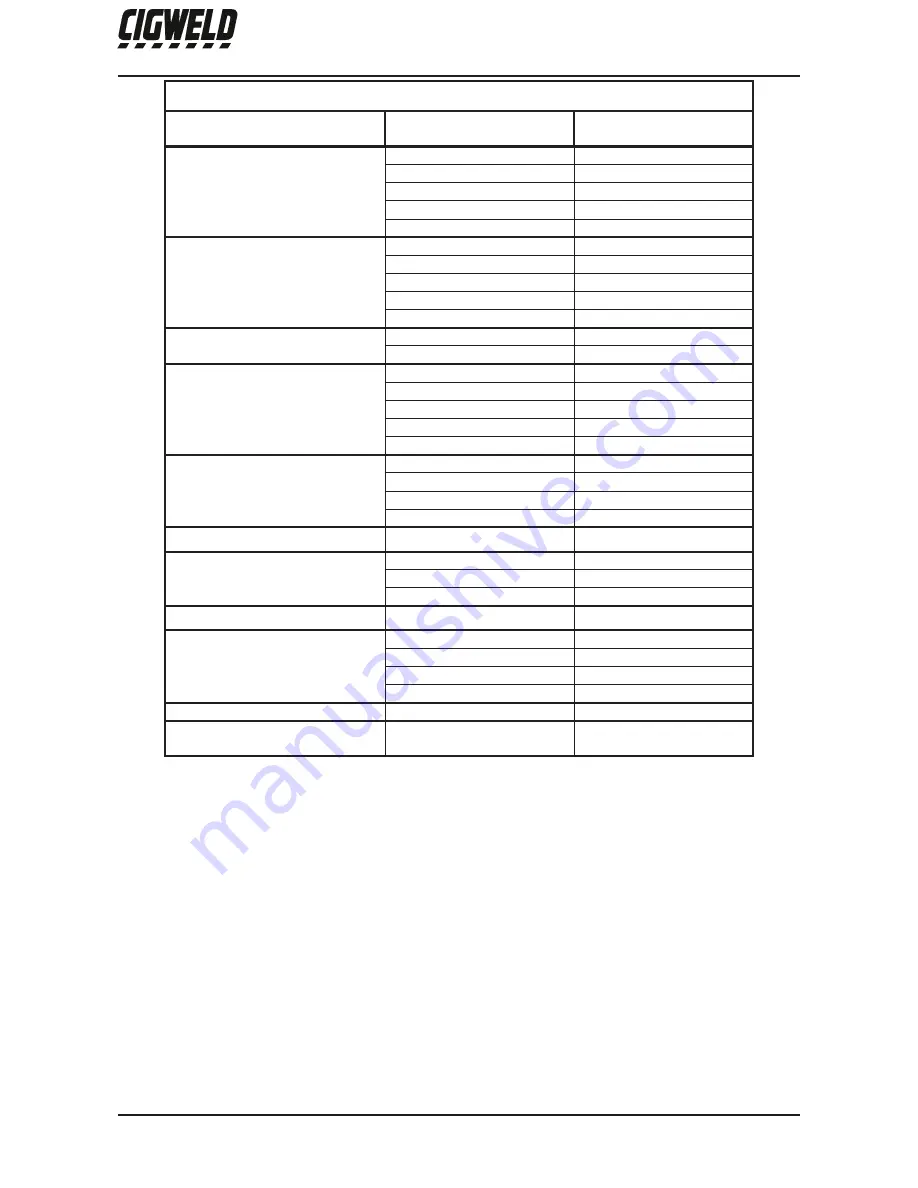
Spool Cover Assembly Instruction 6 Manual 0-5228
SPOOL COVER ASSEMBLY (W4016300) INSTRUCTIONS
Recommended Protective Filters for Electric Welding
Description of Process
Approximate Range of
Welding Current in Amps
Minimum Shade Number of
Filter(s)
Manual Metal Arc Welding - covered
electrodes (MMAW)
Less than or equal to 100
8
100 to 200
10
200 to 300
11
300 to 400
12
Greater than 400
13
Gas Metal Arc Welding (GWAW)
(MIG) other than Aluminium and
Stainless Steel
Less than or equal to 150
10
150 to 250
11
250 to 300
12
300 to 400
13
Greater than 400
14
Gas Metal Arc Welding (GMAW)
(MIG) Aluminium and Stainless Steel
Less than or equal to 250
12
250 to 350
13
Gas Tungsten Arc Welding (GTAW)
(TIG)
Less than or equal to 100
10
100 to 200
11
200 to 250
12
250 to 350
13
Greater than 350
14
Flux-cored Arc Welding (FCAW) -with
or without shielding gas.
Less than or equal to 300
11
300 to 400
12
400 to 500
13
Greater than 500
14
Air - Arc Gouging
Less than or equal to 400
12
Plasma - Arc Cutting
50 to 100
10
100 to 400
12
400 to 800
14
Plasma - Arc Spraying
—
15
Plasma - Arc Welding
Less than or equal to 20
8
20 to 100
10
100 to 400
12
400 to 800
14
Submerged - Arc Welding
—
2(5)
Resistance Welding
—
Safety Spectacles or eye
shield
Refer to standard AS/NZS 1338.1:1992 for comprehensive information regarding the above table