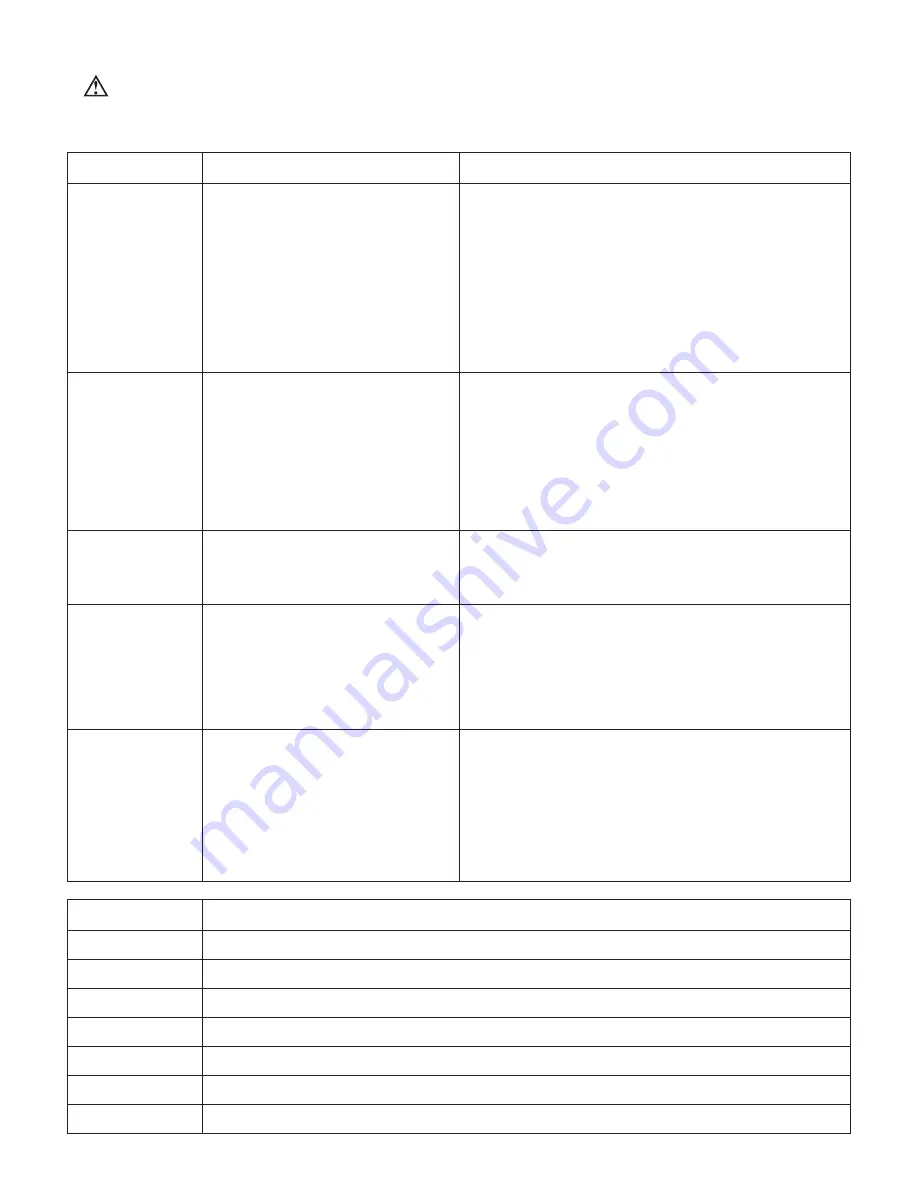
15
Date Performed
Service Performed
Symptom
Possible Causes
Corrective Action
Unit will not run.
1. Improper electrical connection.
1. Assure unit is wired correctly and connected to a live power
line with good fuses.
2. Blower wheel loose.
2. Remove cyclone separator section from inlet to blower
housing. Check wheel to make sure it is not loose on
motor shaft. If it is loose, replace both set screws in the
wheel hub with "knurled cup point set screws with a nylon
locking patch". Tighten set screws to 100 inch pounds on
3 Horsepower models and to 155 inch pounds on all other
models.
NOTE: Setscrews can never be tightened more than once.
Replace wheel if unable to keep it tight on the shaft.
Air flow too low.
1. Incorrect motor rotation.
1. Turn off unit and observe the motor cooling wheel on top
of the motor as it stops. Correct rotation is Counter Clock-
wise. Rewire motor leads as needed to change to the
correct rotation.
2. Duct to small or too long.
2. Review duct design with engineer or duct supplier. Make
changes as necessary.
3. Dirty dust bag.
3. Clean dust bag. See procedure in "Maintenance" on page
12. If dust bag is excessively dirty and can no longer be
cleaned, replace the dust bag.
Dust leaking.
1. Air pressure too high within dust bag.
1. Install air flow diverter (Per STEP 17, Fig. 22, page 11) to
at filter bag.reduce air flow pressure on sidewall of bag.
2. Dust finer than 5 microns.
2. Replace with 1 micron dust bag.
NOTE: 1 micron bag is standard on 7-1/2 Hp model.
Noise level.
1. Air leaking between blower housing
1. Replace gasket between cyclone separator and blower
too high.and cyclone separator.housing. See STEP 3, Fig.
4, page 6.
2. Air leaking at connection between
2. Reseal joint (with RTV sealant) between blower discharge
blower discharge and transition.
and transition. See STEP 9 and 9A, Fig. 12&13 on page 8.
3. Air leaking at any duct joints.
3. Apply RTV sealant at any joint in the duct work that is
leaking.
Motor appears.
1. Dirt accumulation on motor.
1. Blow off excessive dirt. See procedure in "Maintenance"
to be too hot.on page 12.
2. Motor pulling to many AMPS.
2. Check actual amp draw of motor leads and compare them
to AMPS shown on motor nameplate. Actual running amps
should be lower than nameplate amps.
3. Motor temperature may be okay as
3. Check motor surface temperature with a contact pyrometer.
normal motor operation results in a
Normal temperature is 170-175
°
F.
surface temperature too hot to touch.
TROUBLESHOOTING GUIDE
WARNING!
BEFORE attempting to perform ANY of the Corrective Action steps below, make sure that
power to the motor has
first
been properly disconnected or locked-out to prevent accidental starting.
Failure to do so can cause bodily injury and death.