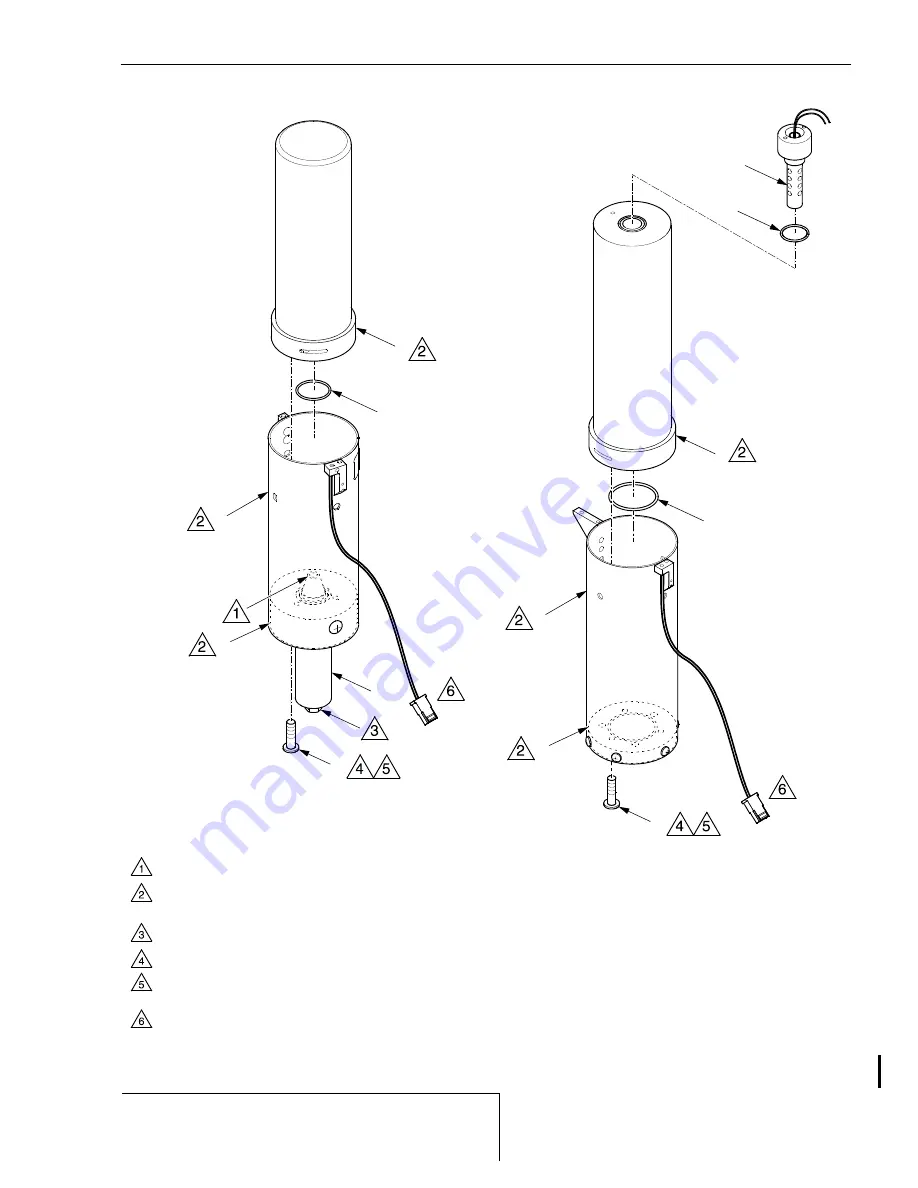
C I R R U S
C O M P O N E N T M A I N T E N A N C E M A N U A L - C A P S
M O D E L S R 2 0
95-01-01
Page 59
All
EFFECTIVITY:
Figure 95-01-0113
Rocket Assembly
Apply plastic fastener threadlocker to nylon screws.
Serials 1005 & subs w/o Aircraft Data Logger:
If plug P1046 is installed to anchor block
on launch tube, remove wire harness assembly from launch tube.
SR20_CM95_2962C
NOTE
LEGEND
1. Rocket Motor
2. Launch Tube
3. Rocket Base
4. Rocket Igniter
5. Nylon Shear Screws
6. O-Ring
Verify foil seal on rocket igniter is intact.
Verify surfaces of launch tube, rocket base, and
rocket motor are clean and free of any debris.
Verify safety wire is installed through firing pin actuator on bottom of rocket igniter.
5
3
2
1
Serials 1005 thru 1267 after SB2X-95-20,
1268 thru 1422 after SB2X-95-17,
2016 & subs w/o Perspective after SB2X-95-18,
2228 & subs.
Serials 1005 thru 1267 before SB2X-95-20,
1268 thru 1422 before SB2X-95-17,
1423 & subs w/o Perspective before SB2X-95-18,
2016 thru 2227.
1
4
5
2
3
4
6
6
6
Install nylon screws securing rocket base to rocket motor.
Torque to 3.0 ±0.5 in-lb (33.9 ±5.6 Ncm).
4 May 2015