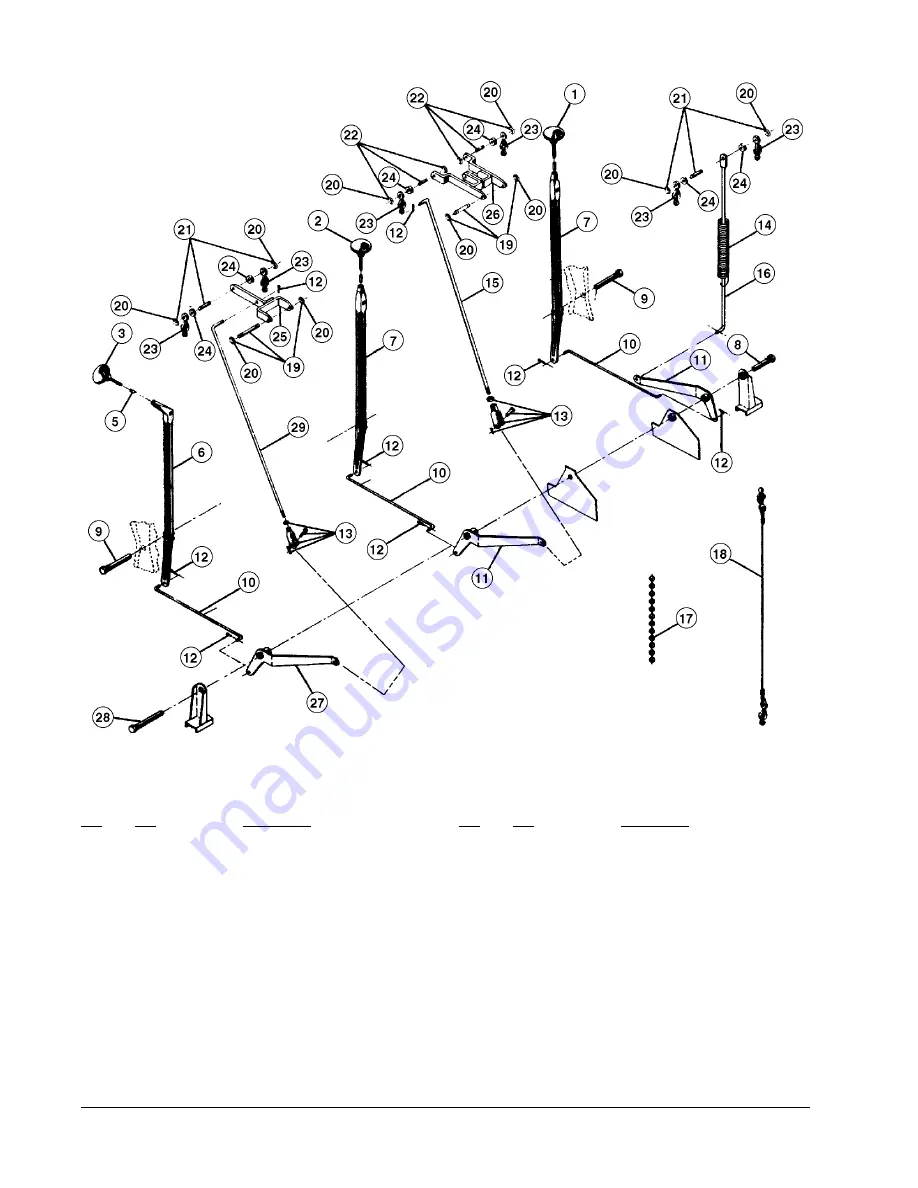
Page 24
Ref.
Part
No.
No.
Description
1
F322
Waist Control Knob
2
F322
Hip Control Knob
3
F321
Lower Control Knob
5
F300
Spacer for Lower Control
6
F319
Actuating Lever
7
F318
Actuating Lever
8
F377
Bearing Pin
9
F324
Bearing Pin
10
F325
Conecting Link
11
F490
Draw String Lever
12
V02
Cotter Pin
13
P39
Yoke, Pin & Cotter Pin
14
F429
Tension Spring
15
F439
D Lever Rod - Hip
F1056
G Lever Rod - Hip
WAIST, HIP, AND LOWER CONTROLS
FOR MODELS D & G
Ref.
Part
No.
No.
Description
16
F440
Lever Rod - Waist
17
040113282
Bead Chain
18
F442
Nylon Cord & Beads
19
F443
2 Pins w/4 E Rings
20
F888
E Rings Only (Pkg. of 6)
21
F444
2 Pins w/4 E Rings
22
F445
2 Pins w/4 E Rings
23
F446
12 Swivels & Beads
24
F447
6 Spacers
25
F448
Lower Control Swivel Arm
26
F449
Hip Control Swivel Arm
27
F450
Lever
28
F331
Bearing Pin
29
F451
D Lever Rod - Lower
F1059
G Lever Rod - Lower
Summary of Contents for FFCD
Page 3: ...Page 3 FF FORM FINISHER LOW BASE OVERALL DIMENSIONS...
Page 6: ...Page 6...
Page 16: ...Page 16...
Page 17: ...Page 17...