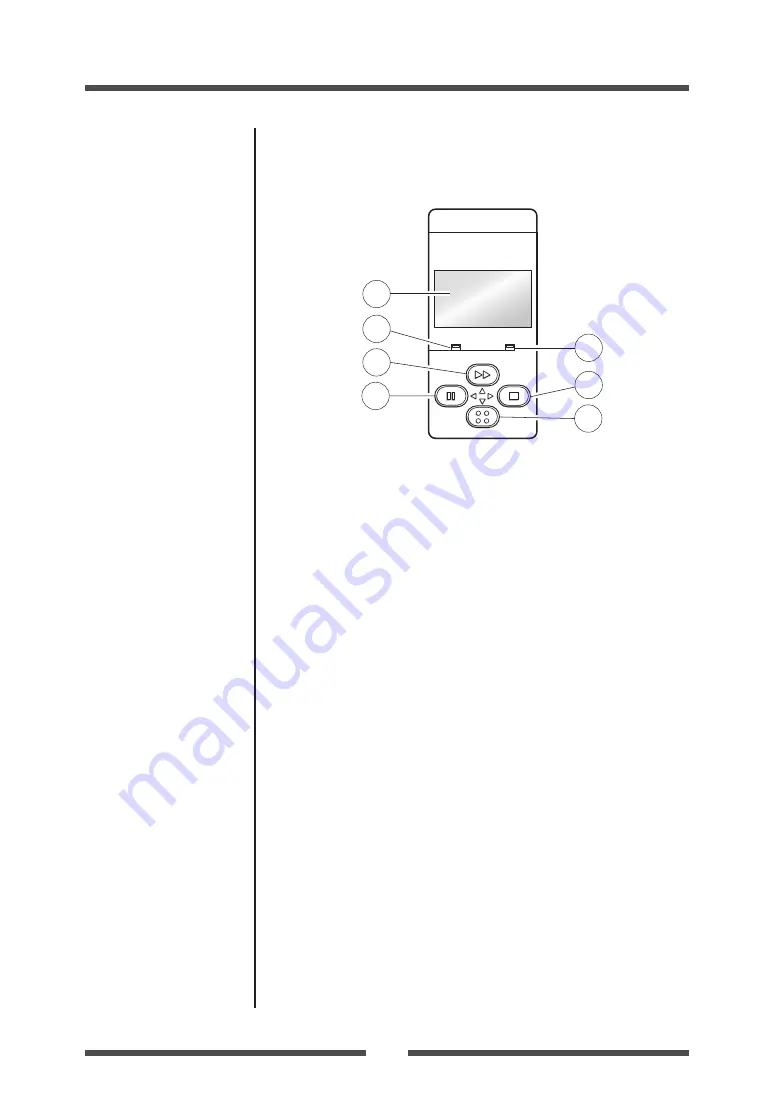
Setup
15
Part Names and Functions
Operation Panel
POWER
ERROR
FEED
STOP
MENU
PAUSE
1
2
4
5
3
6
7
1
LCD display
This displays the operational status of the printer.
2
POWER LED
This is lit when the printer power is on. (green)
3
ERROR LED
This is lit or flashes when the printer is in an alarm or error status.
(orange)
4
FEED key
This key feeds the media to the top of the next label or form.
5
PAUSE key
This temporarily stops printing.
6
STOP key
This stops printing or cancels the alarm.
7
MENU key
In normal operation, this key will enter the menu configuration mode.
It can be configured to repeat the previous label, if preferred.