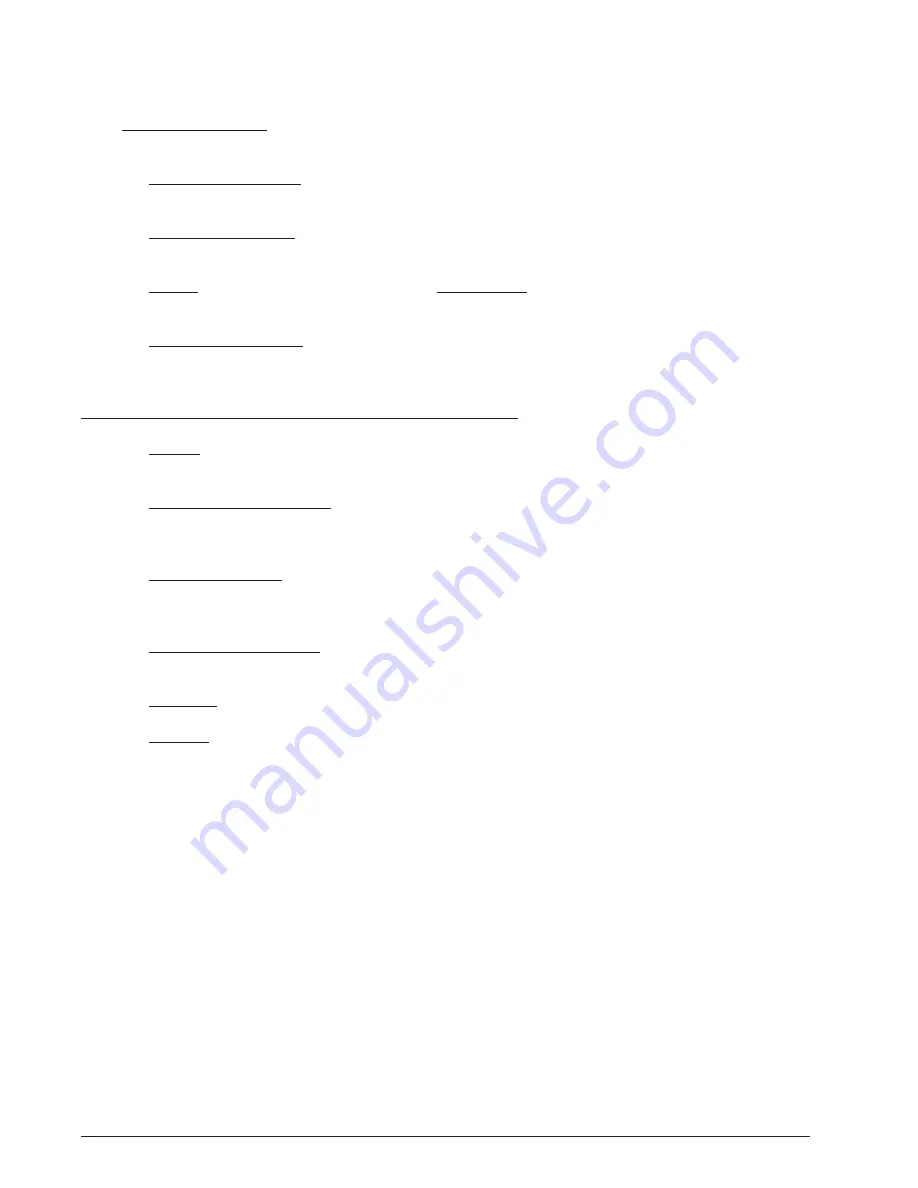
Page 28 Form No. 78149D
Clarke
®
American Sanders
American 8 Floor Sander Operator's Manual
Chatter Wave Prevention
(cont)
3)
UNEVEN WALKING PACE
..... can leave lengthy “waves”. The machine cuts more material during the slower pace.
Pay particular attention to a steady, even pace.
4)
EXCESSIVE LIGHT CUTS
.... may reveal high spots on the paper/contact wheel and cause chatter. Take a heavier cut
and increase the pace.
5)
DEBRIS
.... lodged between the paper and the drum will leave chatter. On a belt sander, debris may be adhered to the
drum. Insure the drum is clean and free of debris before placing the paper on.
6)
SANDER PAPER QUALITY
....may vary. Belt seams can be thicker on low quality paper and cause chatter. Use only
Clarke American Sanders speci
fi
ed sandpaper.
PROPER CARE OF YOUR MACHINE CAN MINIMIZE CHATTER AND WAVES
.
1)
V-BELTS
.... can cause vibration and chatter if they are of low quality. Use only belts speci
fi
ed by Clarke American Sand-
ers.
2)
TRUCK AND CASTER WHEELS
....with
fl
at spots, out-of-roundness, or debris adhered to their surface can cause
“waves” or a “chatter effect”. Always clean and inspect all wheels before starting to sand, and before the
fi
nish
cut. Replace or true the wheels if found to be out-of-round.
3)
DUST PICK-UP SHOES
.......may need adjusted differently for different materials that are to be sanded. An improperly
adjusted shoe will leave trailing debris that will be run over by the wheels and cause “random waves”.
4)
CONTACT WHEELS (DRUMS)
.......may be out-of-round and cause “chatter”. Contact your Clarke American Sanders
dealer for assistance to true or replace the drum.
5)
BEARINGS.
.....in the motor, drum, or fan system may become worn and induce vibration which could cause “chatter”.
6)
PULLEYS.
....that are damaged or severly worn can induce vibration and cause “chatter”. Contact your Clarke American
Sanders dealer for assistance.
Clarke American Sanders is not responsibile for rework of
fl
oors that are unacceptable to the customer. It is your
responsibility to insure your equipment is in proper operating order, and that you use the right machine for the job.
Summary of Contents for 07032C
Page 19: ...Page 18 Form No 78149D Clarke American Sanders American 8 Floor Sander Operator s Manual NOTES...
Page 30: ......
Page 31: ......
Page 32: ......