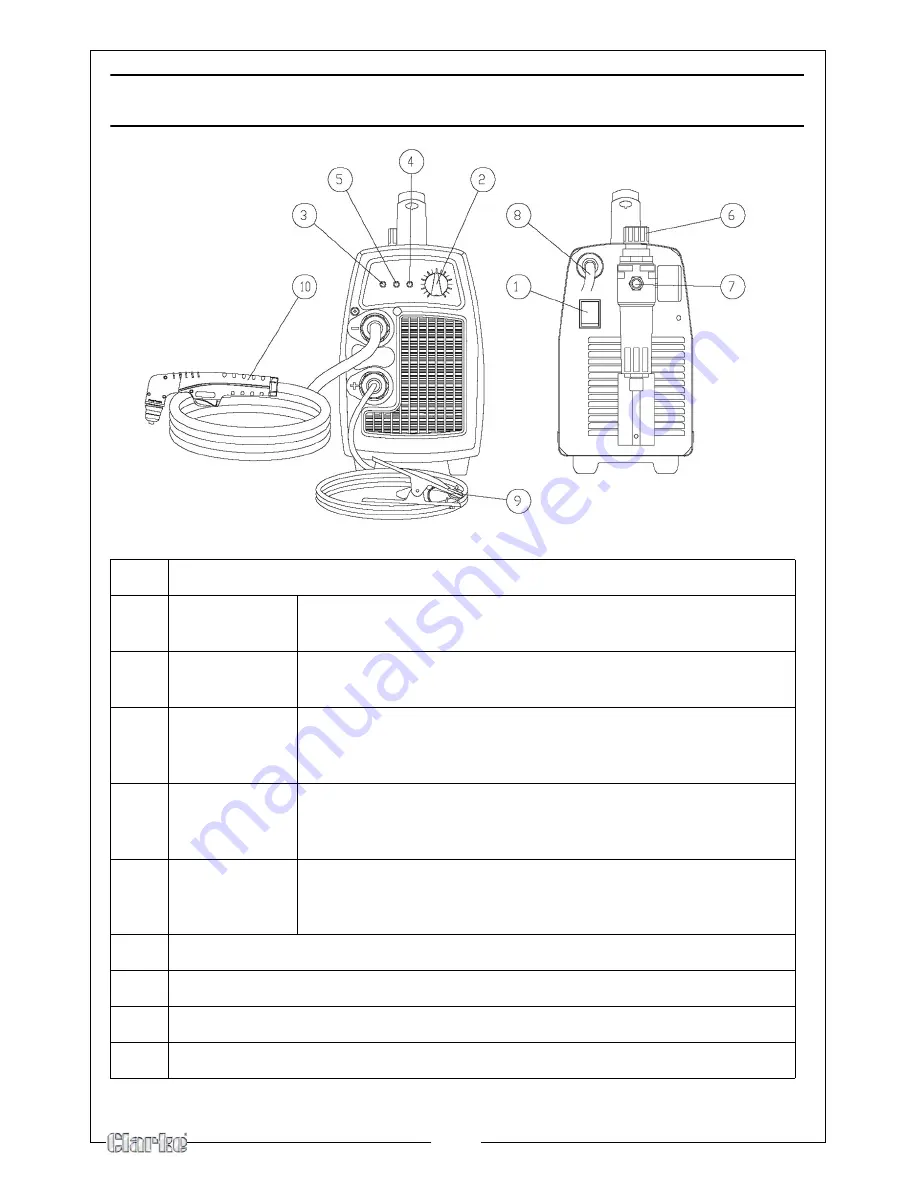
12
PARTS IDENTIFICATION
1
ON/OFF Switch
2
Output
current knob
Adjusts the cutting current supplied by the machine
according to the thickness of material/speed.
3
Green LED
Turns ON when input voltage is applied
blinks slowly when voltage goes above 260V, or below 180V.
4
Red LED
Turns ON when torch is triggered. Blinks quickly during 3 second
safety pre-flow prior to pilot arc ignition. Blinks slowly if
cutting arcs not initiated after 3 second pilot arc ignition.
5
Yellow LED
ON when the thermal protection is activated.
Blinks slowly when the under pressure protection is working
(the pressure is less than 3,8 Bar).
6
Air regulator
Adjusts the input air pressure - pull upward to unlock -
nominal air pressure setting is 4,5 Bar.
Note: the regulator should never be set above 6 Bar.
7
Compressed air connection
8
Input cord
9
Work cable with clamp
10
Torch (with a trigger security cap)
Summary of Contents for 30SI
Page 1: ...OPERATION MAINTENANCE INSTRUCTIONS LS1208 PLASMA CUTTER MODEL NO 30SI PART NO 6016010...
Page 2: ...2...
Page 25: ...25 WIRING DIAGRAM...
Page 26: ...26 DECLARATION OF CONFORMITY...
Page 27: ...27 NOTES...
Page 28: ......