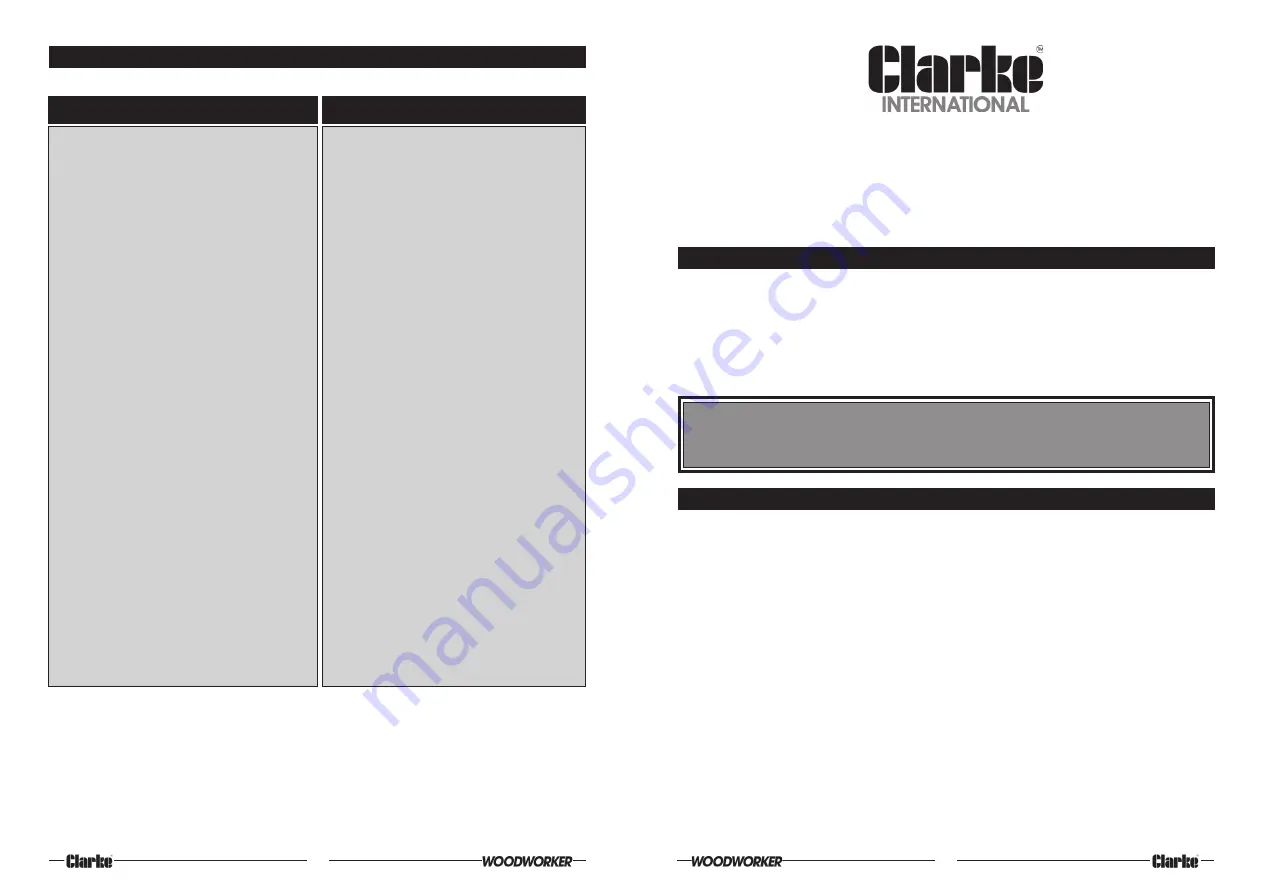
O
3
GUARANTEE
This CLARKE product is guaranteed against faulty manufacture for a period of 12 months from the
date of purchase. Please keep your receipt as it will be required as proof of purchase. This guarantee
is invalid if the product is found to have been abused or tampered with in any way, or not used for the
purpose for which it was intended.
Faulty goods should be returned to their place of purchase, no product can be returned to us without
prior permission. This guarantee does not effect your statutory rights.
Thank you for purchasing this CLARKE 20” Wood lathe, designed for DIY use only.
Before assembling this machine, please read this manual thoroughly and follow all instructions
carefully. In doing so you will ensure the safety of yourself and that of others around you, and you can
look forward to the wood lathe giving you long and satisfactory service.
WARNING:
THIS MACHINE MUST NOT BE MODIFIED, OR USED FOR ANY PURPOSE
OTHER THAN THAT FOR WHICH IT IS DESIGNED.
SPECIFICATIONS
Motor .............................................................................................. 230V 50Hz 1Ph
Power Rating ................................ 370W (1/2 HP)
Switch Type ................................... No Volt Release
Turning Capacity
(Between Centres) ....................... 20 in (508mm)
(Over Bed) .................................... 9 1/2in Dia (242mm)
Spindle Speeds
1. .................................................... 850RPM
2. .................................................... 1250RPM
3. .................................................... 1750RPM
4. .................................................... 2510RPM
Headstock Thread ........................................................................ 3/4” x 16TPI (UNF)
Tailstock Spindle ............................................................................ Fixed Rotating Centre
Tailstock Spindle Advance ........................................................... 2” (50mm) max. via hand wheel
Overall Dimensions (LxWxH) ......................................................... 950x220x280mm
Weight ............................................................................................ 24kg
No. Description
Part No.
1
Bearing Block
SD6001
2
Face Plate
SD6002
3
Tool Rest
SD6003
4
Tool Rest Holder
SD6004
5
Slide Block
SD6005
6
Locking Block
SD6006
7
Spindle Pulley
SD6007
8
Motor Pulley
SD6008
9
Hand Wheel
SD6009
10 Head Stock Spindle
SD6010
11 Driving Centre
SD6011
12 Name Plate (Not Shown)
SD6012
14 Tool Rest Shaft
SD6014
15 Tailstock Spindle
SD6015
16 Locknut
SD6016
17 Locknut
SD6017
18 Headstock Cover - 1
SD6018
19 Motor Cover
SD6019
20 Pulley Cover
SD6020
21 Headstock Cover - 2
SD6021
22 Headstock Cover - 3
SD6022
23 Mounting Foot
SD6023
24 Bed Rail
SD6024
25 Tailstock
SD6025
26 Belt Tension Lever
SD6026
27 Bolt
SD6027
28 Bolt
SD6028
29 Bolt
SD6029
30 Bolt
SD6030
31 Machine Screw
SD60231
32 Bolt
SD6032
33 Lock Knob
SD6033
34 Socket Head Screw
SD6034
35 Washer
SD6035
36 Washer
SD6036
37 Washer
SD6037
38 Bearing
SD6038
39 Bearing
SD6039
40 Switch
SD6040
41 Belt Tensioning Lever
SD6041
42 Hinge
SD6042
43 Belt
SD6043
45 Bolt
SD6045
46 Motor
SD6046
47 Washer
SD6047
48 Bolt
49 Power Cable with Plug
30
PARTS LIST
No. Description
Part No.