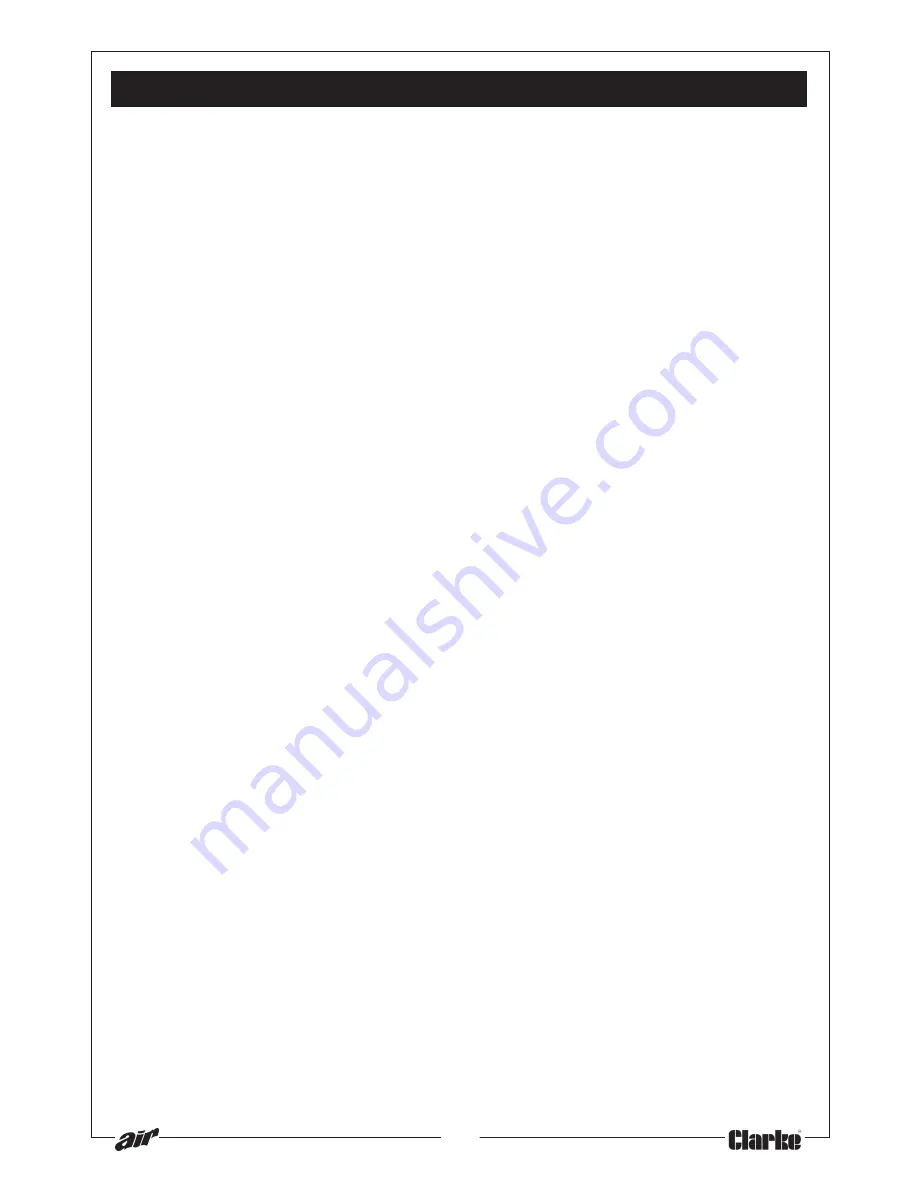
20
SPECIFICATIONS
Electrical Supply .....................................
230 V, 1 Phase 50Hz
Max. Operating Pressure .......................
10 bar / 145 psi
Motor Rating ...........................................
3 HP
Air Displacement ....................................
12.2 cuft/min
Air Receiver .............................................
100 litre
Net Weight ..............................................
71kg
Dimensions ( L x W x H ) .........................
1220 x 460 x 810 mm
Duty Cycle ..............................................
S1 (continuous)
Part No. ....................................................
2225460
Please note that the details and specifications contained herein, are correct at
the time of going to print. However, we reserve the right to change
specifications at any time without prior notice. Always consult the machine’s
data plate
Summary of Contents for BOXER 100
Page 1: ...1 OPERATION MAINTENANCE INSTRUCTIONS BOXER100 AIRCOMPRESSOR 0109 BOXER100 AIRCOMPRESSOR ...
Page 21: ...21 PARTS DIAGRAM ...
Page 23: ...23 ...
Page 24: ......