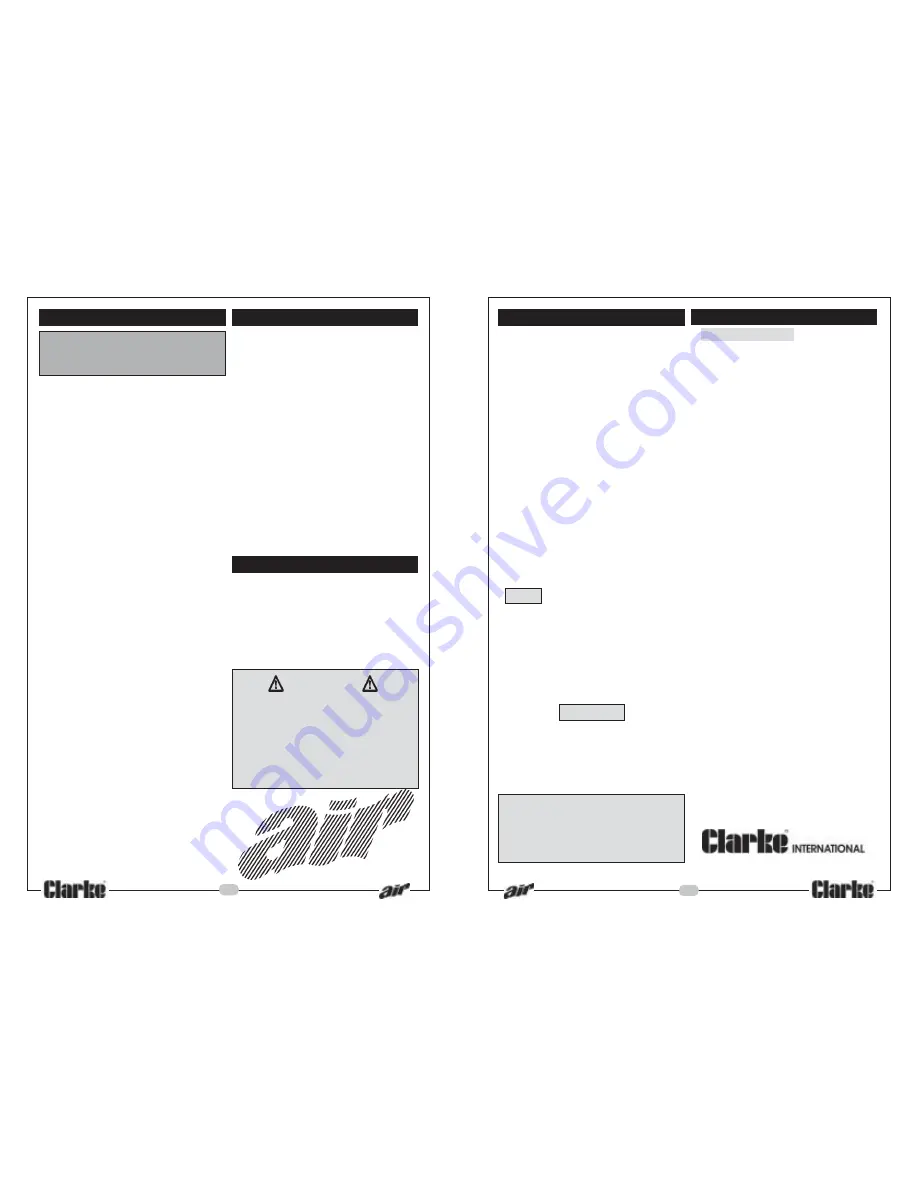
- 3 -
- 4 -
SAFETY PRECAUTIONS
IMPORTANT
Failure to follow these precautions could
result in personal injury, and/or damage to
property.
❐
When operating this tool, ALWAYS wear:
a.
approved impact resistant SAFETY
GOGGLES. (Eye glasses are NOT
safety glasses)
b.
a DUST MASK
c.
EAR DEFENDERS
d.
a good pair of INDUSTRIAL GLOVES
❐
ALWAYS
disconnect the tool when not
in use, and before carrying out any
maintenance
❐
ALWAYS
keep a safe distance between
yourself and other people when using
the tool.
❐
ALWAYS
maintain the tool with care. Keep
it clean for best and safest performance.
❐
NEVER
wear ill fitting clothing, remove
watches and rings.
❐
Quick change couplings should not be
located at the tool. They add weight
and could fail due to vibration.
❐
DO NOT
overreach. Keep your proper
footing and balance at all times.
❐
DO NOT
force or misuse the tool. It will
do a better and safer job at the rate for
which it was designed.
❐
DO NOT
abuse hoses or connectors.
NEVER carry a tool by the hose, or yank
it to disconnect from the air supply. Keep
hoses away from heat, oil and sharp
edges. Check hoses for leaks or worn
condition before use, and ensure that
all connections are secure.
❐
DO NOT
exceed 90 PSI at the tool.
❐
DO NOT
modify the tool in any way.
❐
DO NOT
remove any labels. Damaged
labels should be replaced.
❐
This tool vibrates with use. Vibration may
be harmful to your hands or arms. Stop
using the tool if discomfort, a tingling
feeling or pain occurs. Seek medical
advice before resuming use.
❐
ALWAYS
use screens to protect people
in the vicinity from flying debris.
❐
NEVER
point the tool at anyone.
WARNING
Compressed air can be
dangerous. Ensure that
you are thoroughly
familiar with all
precautions relating to the
use of compressors and
compressed air supply.
AIR SUPPLY
Tools of this type, operate on a wide range
of air pressures. It is recommended that air
pressure to this tool does not exceed 90 PSI
(6.1bar), at the tool when running. Higher
pressure and unclean air, will shorten the tools’
life because of faster wear, and could be a
safety hazard.
Water in the air line will cause damage to
the tool, ensure it is properly maintained at
all times.
The recommended procedure to connect
this tool to an air supply, is shown at fig. 1 on
inside front cover.
The air inlet used for connecting air supply,
has a standard ¼” BSP thread.
Line pressure, or hose inside diameter, should
be increased to compensate for unusually
long air hoses (over 10m). Minimum hose
diameter should be 6mm (¼") ID., and fittings
should have the same inside dimensions.
ASSEMBLY
Connect a suitable hose to the Impact
Wrench using a ¼” hose adapter, (A whip
hose with Quick Fit coupling is available from
your CLARKE dealer). then connect the other
end to the airline. NOTE
:
ensure the airline is
turned off.
Your Impact Wrench is now ready for use.
Before starting work drain any water from the
air tank and blow condensation from the air
line. Drain compressor more frequently in hot
humid weather.
1. Ensure air is turned OFF, select
appropriate impact socket, which
must be in good condition, and fits the
tool shank and nut closely.
2. Turn ON the air supply, and check for air
leaks. If any are apparent, rectify before
proceeding. Ensure the operating pressure
is set to 6.2bar.
3. Set the regulator (Item 15) to ‘0’
(Zero), and apply the wrench to the
nut or bolt.
4. Depress the throttle (Item 5), either
forward or reverse, depending
whether you are loosening or
tightening, also whether or not the
thread is left or right handed,
gradually adjust the regulator until the
fastener starts to move. The tool is now
set to duplicate that tightness.
NOTE:
When critical torque values are not required,
turn the nut or bolt one quarter to one half a
turn until it fits snugly - slightly more if gaskets
are used between surfaces.
For additional power on disassembly work
turn regulator out to it’s highest setting,
(maximum pressure).
IMPORTANT
Where torque settings are critical, the final
tightening of nuts or bolts must be by hand,
using a calibrated torque wrench.
OPERATING INSTRUCTIONS
MAINTENANCE
Daily before use.
1.
Drain water from air tank, air line and
compressor.
2.
Check and clean, if necessary, the
air inlet gauze filter .
3.
Pour a few drops of CLARKE Air Line
Oil (approx 3cc), into the air inlet. This
should be carried out regardless of
whether or not an air line lubricator
is used.
If an Air line lubricator is NOT used,
this procedure should be repeated
after every two to three hours of use.
If the wrench is to be stored, or is idle for longer
than 24 hours, run a few drops of Clarke Air
Line Oil into the air inlet, and run the tool for 5
seconds in order to lubricate the internal
parts.
For lubricating the air motor when in
operation, an air line lubricator should be
used, with Clarke Air Line Oil, adjusted to 2
drops per minute.
CLARKE
Air Line Oil is available from your
CLARKE
dealer, part no. 3050825.
Be aware that factors other than the tool may
effect its operation and efficiency, such as
reduced compressor output, excessive drain
on the airline, moisture or restrictions in the
line, or the use of connectors of improper size
or poor condition which will reduce air supply.
Grit or gum deposits in the tool may also
reduce efficiency. This condition can be
corrected by cleaning the air strainer and
flushing out the tool with gum solvent oil, or
failing this, the tool should be disassembled,
thoroughly cleaned, dried and reassembled.
If the tool runs erratically or becomes
inefficient, and the air supply is sound,
dismantle the air motor and replace worn or
damaged parts, or take the tool to your
CLARKE
dealer.
WARNING
NEVER
use standard hand sockets, as these
could shatter with serious consequences, use
only impact sockets, which must be in good
condition.