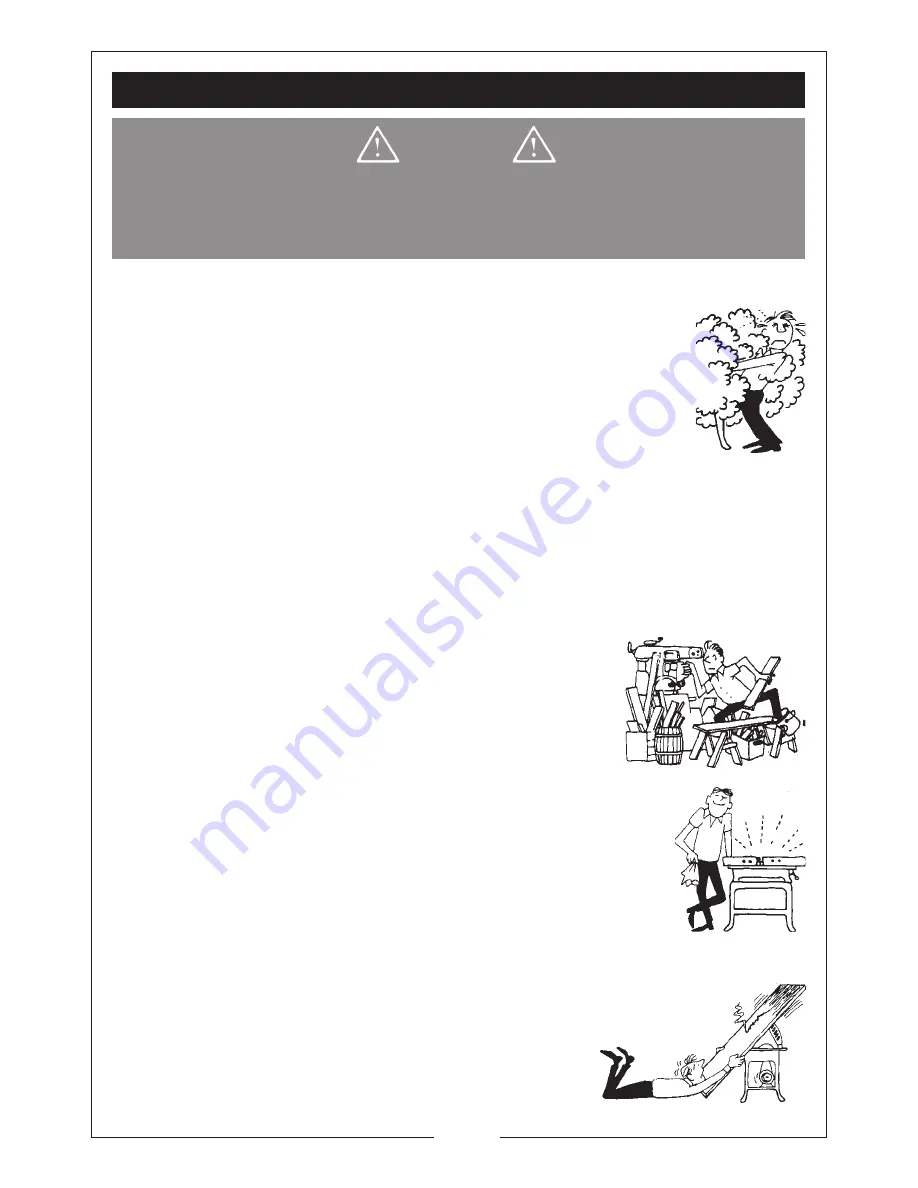
4
GENERAL SAFETY PRECAUTIONS
WARNING:
As with all machinery, there are certain hazards involved with their operation
and use. Exercising respect and caution will considerably lessen the risk of
personal injury. However, if normal safety precautions are overlooked or
ignored, personal injury to the operator or damage to property, may result.
1.
ALWAYS
Learn the machines’ applications, limitations and the specific potential
hazards peculiar to it. Read and become familiar with the entire
operating manual.
2.
ALWAYS
use a face or dust mask if operation is particularly dusty.
3.
ALWAYS
check for damage. Before using the machine, any damaged
part, should be checked to ensure that it will operate properly, and
perform its intended function. Check for alignment of moving parts,
breakage of parts, mountings, and any other condition that may
affect the machines’ operation. Any damage should be properly repaired
or the part replaced. If in doubt,
DO NOT
use the machine. Consult your local dealer.
4.
ALWAYS
disconnect the tool/machine from the power supply before servicing and
when changing accessories.
5.
ALWAYS
wear safety goggles, manufactured to the latest European Safety Standards.
Everyday eyeglasses do not have impact resistant lenses, they are not safety glasses.
6.
ALWAYS
keep work area clean. Cluttered areas and benches
invite accidents.
7.
ALWAYS
ensure that adequate lighting is available. A
minimum intensity of 300 lux should be provided. Ensure
that lighting is placed so that you will not be working in your
own shadow.
8.
ALWAYS
keep children away. All visitors should be kept a
safe distance from the work area, especially whilst operating
the machine.
9.
ALWAYS
maintain machine in top condition. Keep tools/machines
clean for the best and safest performance. Follow maintenance
instructions.
10.
ALWAYS
handle with extreme care do not carry the tool/machine
by its’ electric cable, or yank the cable to disconnect it from the
power supply .
11.
ALWAYS
ensure the switch is off before plugging in to mains. Avoid accidental
starting.
12.
ALWAYS
concentrate on the job in hand, no matter how trivial it may
seem. Be aware that accidents are caused by
carelessness due to familiarity.
13.
ALWAYS
keep your proper footing and balance at all
times, don’t overreach. For best footing, wear rubber
soled footwear. Keep floor clear of oil, scrap wood, etc.