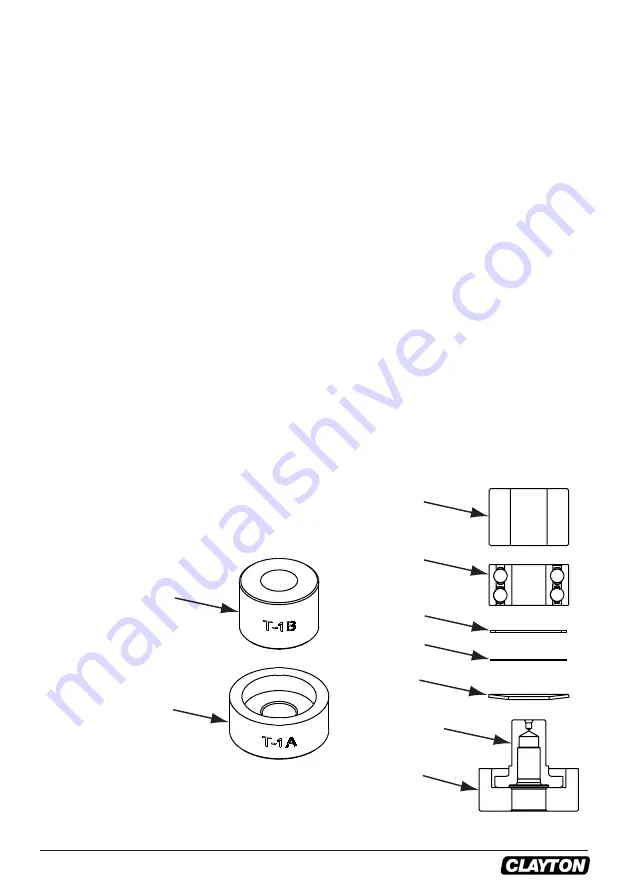
Copyright © 2016 Clayton Associates, Inc. • 1650 Oak St. • Lakewood, NJ 08701
800-248-8650 • www.VacuumSanding.com
6
o-ring pick or a #8 sheet metal screw to grip and pull
out the Retainer. Remove the Valve and Filter from the
bore in the Shaft Balancer. If the Retainer and Valve
were not damaged, they can be reused. However, the
Filter should be replaced on re-assembly.
4. Remove the Retaining Ring from the Spindle.
5. Remove the bearing from the Spindle. Remove the
Spacer, Dust Shield and Washer from the Spindle.
Discard Dust Shield.
Housing Disassembly:
1. Unscrew the threaded Plug(s) and/or the Handle (if
used) from the Motor Housing.
2. Remove the Hanger and Spacer Ring. (if used)
3. Remove the Retaining Ring. The Speed Control (with
O-Ring) will now pull straight out from the Motor Hous
-
ing. Use an o-ring pick to remove the O-Ring from the
Speed Control.
4. Use a T-20 Torx driver to unscrew all Screws.
5. Remove the Housings.
6. Remove the Muffler and Seals from the Housing.
6a. For Non-Vacuum (NV) machines: Remove the End
Cap.
6b. For Central Vacuum (CV) and Self Generated Vacuum
(SGV) machines: Remove the End Cap. Remove the
Hose Seal from the CV/SGV End Cap.
7. Unscrew the Inlet Bushing from the End Cap. Remove
the Mufflers, Captive Ring, O-Ring, and O-Ring from
the End Cap.
8a. For NV and CV machines: Remove the exhaust (Tub
-
ing, Tubing Clamp, and inlet Tubing from the motor
housing assembly. Separate the exhaust Tubing, Tub
-
ing Clamp, and inlet Tubing from each other.
8b. For SGV machines: Remove the inlet Tubing from the
motor housing assembly.
9. Unscrew the three Screws from the motor housing as
-
sembly.
10a.For NV and CV machines: Remove the NV/CV Ex
-
haust Nozzle and the Gasket from the motor housing
assembly.
10b.For SGV machines: Remove the SGV Exhaust Nozzle
and the Gasket from the motor housing assembly.
11. Press out the Spring Pin from the Motor Housing and
remove the Throttle Lever.
12. Remove the Seal Assembly. This component can
become damaged during removal and will need to be
replaced if damaged.
13. Remove the Spring, Valve, Valve Seat, and the Valve
Stem from the Motor Housing. Use an o-ring pick to
remove the o-ring from the Valve Stem.
14. Remove the Sleeve from the Motor Housing.
15. Remove the Shroud from the Motor Housing.
ASSEMBLY INSTRUCTIONS
NOTE: All assembly must be done with clean dry parts and
all bearings are to be pressed in place by the correct tools
and procedures as outlined by the bearing manufacturers.
Housing Assembly:
1. Press the Sleeve flush to the top of the Motor Housing.
Press Tool Top
Press Tool Base
Spacer
Dust Shield
Bearing
Washer
Spindle
T-1B
T-1A