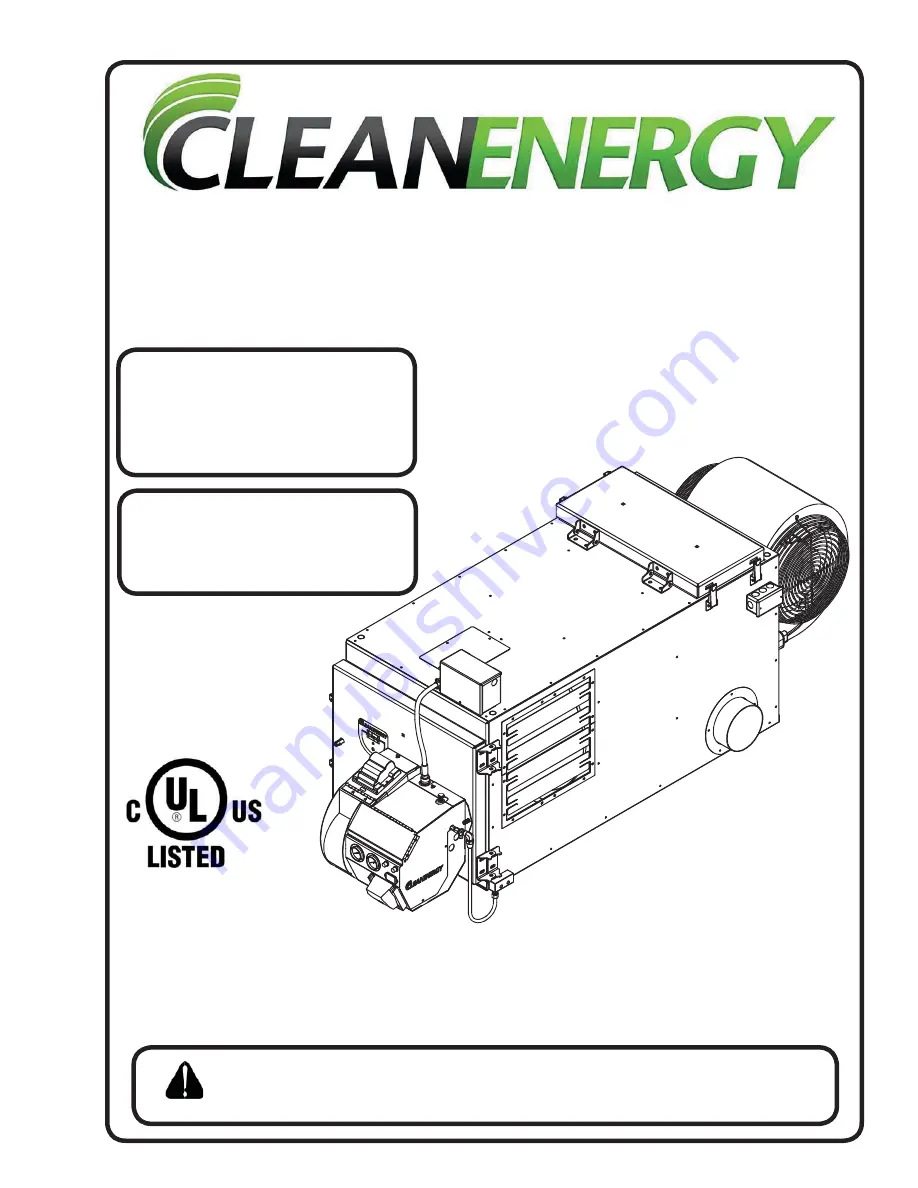
OWNER’S MANUAL
CE-140 Mul -Oil Furnace
CE-180 Mul -Oil Furnace
CE-250 Mul -Oil Furnace
With CE-3 Burner
CE-330 Mul -Oil Furnace
CE-440 Mul -Oil Furnace
With CE-4 Burner
Clean Energy Heating Systems, LLC
PO Box 1341, 540 Maple Street, Honey Brook, PA 19344
www.CleanEnergyHeatingSystems.com
(888) 519-2347
WARNING:
For your safety - DO NOT store gasoline or other flammable
vapors and liquids in the vicinity of this or any appliance.
Heating Systems
®
CE70155
Summary of Contents for CE-140
Page 50: ...50 NOZZLE ADAPTER HEATER BLOCK ASSEMBLY 2 3 19 5 7 8 15 9 17 14 18 16 13 1 4 6 10 11 12 ...
Page 52: ...52 MANIFOLD BLOCK ASSEMBLY 8 6 2 1 4 17 3 9 5 7 12 13 14 15 16 18 19 11 10 ...
Page 58: ...58 3 4 6 1 2 5 CE 140 180 BLOWER ...
Page 62: ...62 2 3 4 5 6 1 CE 250 BLOWER ...
Page 66: ...66 CE 330 BLOWER 12 8 7 4 13 1 2 3 5 6 9 10 11 ...
Page 70: ...70 CE 440 BLOWER 12 8 7 4 13 1 2 3 5 6 9 10 11 ...