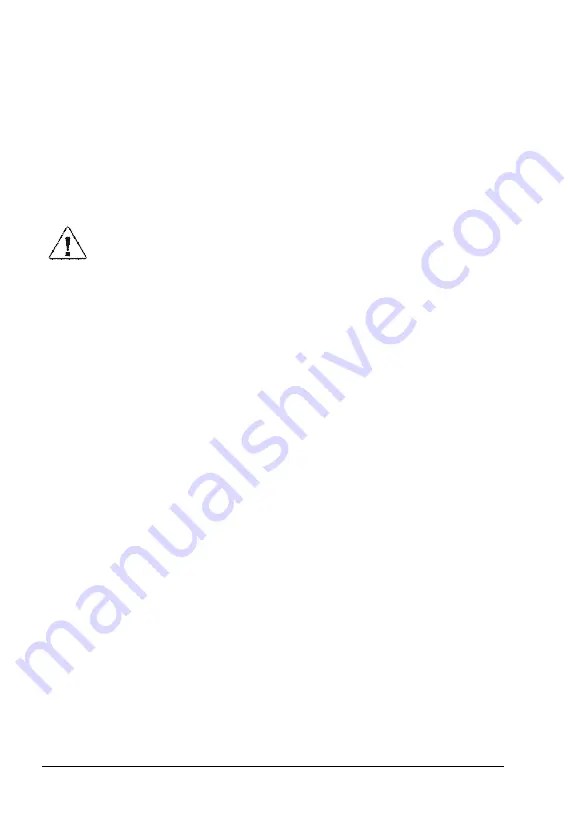
- 10 -
2 for 4-20mA signal input(white)
3 for pulse signal input( green)
4 for remote control (red)
4
4
4
4 Maintenance
Maintenance
Maintenance
Maintenance and
and
and
and Repair
Repair
Repair
Repair
Warning
Warning
Warning
Warning
�
Electric maintenance must be carried out by qualified electrician.
�
Before maintenance, please unplug the power socket or cut off the
power. If there is relay, it should be cut off. Make sure there is no power
during maintenance.
�
During maintenance, please release the pressure in the tubes first,
and clean the pump head. Don’t use corrosive liquids.
�
If medium is dangerous liquid, please check the performance
parameters of the medium. Discharge and wash the pump head before
maintenance.
4.1
4.1
4.1
4.1
Maintenance
Maintenance
Maintenance
Maintenance
Strictly check the following items when maintenance.
�
Pump head bolts (make sure it is firmly connected)
�
Inlet and outlet tubes(make sure it is firmly connected)
�
Pump head and valves(make sure it is firmly connected)
Summary of Contents for Precision-24
Page 1: ...Precision 24 Manual Specification ...
Page 2: ......
Page 18: ... 15 6 6 6 6 Main Main Main Main parts parts parts parts ...