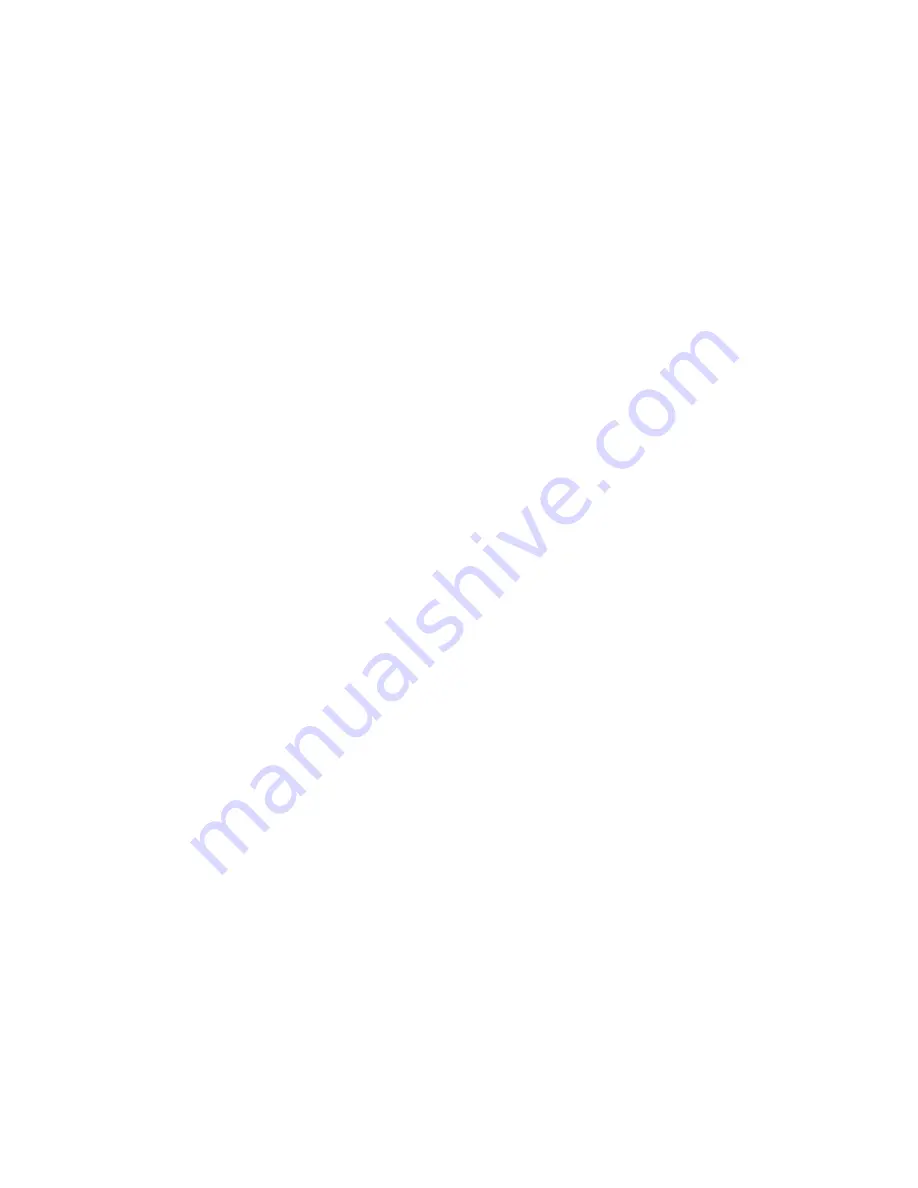
10
into the blower chamber which could damage the blower
itself. The inline vacuum breaker adds years to the
vacuum blowers life by reducing stress caused plugged
filters and limited air intake. The recovery tank also has
two access lids for easy access to the lint basket and the
stainless steel blower protection filters. These filters
require regular cleaning on a daily basis as a minimum.
To finish off the recovery tank Cleanco added an
integrated storage shelf, giving the operator added
space for specialty tools that may be required at the
cleaning site.
MAINTENANCE
To avoid costly repairs and downtime, it is imperative to
develop and practice good maintenance procedures.
These procedures must be preformed on a daily, weekly,
monthly, quarterly and bi annual schedule.
As part of your Cleanco package you receive a
Cleanco
Maintenance Booklet.
This booklet provides you with a
convenient format for recording the required
maintenance of your Cleanco unit and van. You are
required to perform all maintenance items in the
Maintenance Schedule and record that you have done
so in this booklet as part of your Cleanco Warranty. It is
your responsibility to keep a copy of all repair orders and
receipts that relate to your Cleanco unit and Van. These
records of services and purchases will be required to
substantiate proper maintenance to your Cleanco unit
and Van for any warranty claim.
DAILY
Check van engine oil.
Check van engine coolant level.
Check high-pressure pump oil level.
Check vacuum blower oil level.
Clean vacuum tank lint basket.
(Should be cleaned
after every job)
Clean the stainless steel blower protection filters.
Lubricate blower with
LPS/TKX
lubricant.
Winterize system if necessary.
WEEKLY
Check engine air cleaner filter. (clean as necessary)
Check Front drive belts. (adjust if necessary)
Check blower belts. (adjust if necessary)
Check high-pressure pump belt. (adjust if necessary)
Clean in-coming water filter.
Flush chemical system with 50/50 mixture of vinegar
and water.
Inspect unit for loose wires, oil leaks, and water
leaks.
Check engine RPM with unit running at fast idle.
(setting 1450 RPM under load )
Blower Speed. (actual reading)
Vacuum Gauge. (actual reading)
Temperature Gauge. (actual reading)
Hour Meter. (actual reading)
Clean wand and inspect for clogged jets.
Clean recovery tank thoroughly with high pressure
water.
MONTHLY
Change van engine oil.
Check van transmission oil level.
Check van coolant level.
Check engine air cleaner filter. (clean as necessary)
QUARTERLY SERVICE
Change oil in high-pressure pump.
Change oil in vacuum blower.
Flush entire water flow system. (coil flush if
necessary)
Check that all nuts and bolts are tight.
Check all hose clamps, tighten if necessary.
Grease front and rear PTO shaft bearings with SKF
LGMT 3/0.4 bearing grease.
BI - ANNUAL MAINTENANCE
Change the coolant and flush the
coolant system completely.
AS REQUIRED / COIL FLUSH
If your area has hard water you may see evidence of
hard water deposits form in the water system, or on the
quick connects. If scale is present, the water system
should be flushed with Coil Cleaner. This procedure may
have to be increased to a monthly interval if heavy built-
up is present. For information on flushing coils contact
your nearest Cleanco distributor.
Over all machine maintenance and appearance is very
important. It represents your company’s professional
appearance and is how you make your living. A clean
well maintained machine will give you years of reliable
performance. Maintenance, troubleshooting, and repair
is much easier on a clean well maintained unit. Regular
cleaning and maintenance will give you the opportunity
to spot any potential problems normally before they
occur.
It is important that you follow and record the
maintenance on your Cleanco unit and van according to
the Cleanco Maintenance Booklet to insure complete
warranty coverage.
Summary of Contents for Compact 45
Page 1: ...VERSION AUG 2017...
Page 13: ...12...
Page 14: ...13...
Page 18: ...17 WATER PUMPING AND HEAT TRANSFER SYSTEM...
Page 19: ...18 WATER PUMPING AND HEAT TRANSFER SYSTEM DUAL HEAT EXCHANGER WITH P T I OPTION...
Page 28: ...27 CLEANCO COMPACT OVERHEAD VIEW...
Page 29: ...28...
Page 30: ...29 FRONT PANEL 45 47 FRONT VIEW...
Page 31: ...30 FRONT PANEL 45 47 BACK VIEW...
Page 33: ...32 FRONT PANEL PLUMBING P 1...
Page 34: ...33 FRONT PANEL PLUMBING P 2...
Page 37: ...36 COMPACT RECOVERY TANK...
Page 39: ...38 COMPACT BASEPLATE 45 47 P 1...
Page 40: ...39 COMPACT BASEPLATE 45 47 P 2...
Page 45: ...44 KIT INSTALLATION 45 47 P 1...
Page 46: ...45 KIT INSTALLATION 45 47 P 2...
Page 49: ...48 DUAL HEAT EXCHANGER...
Page 51: ...50 P T I...
Page 53: ...52 COVER HOLDER KIT...
Page 55: ...54 PTO SHAFT...
Page 58: ...57 C A D EXTERNAL OPTION PAGE 1...
Page 59: ...58 C A D EXTERNAL OPTION PAGE 2...
Page 61: ...60 F W TANK AQUA STORAGE 120 GALLON...
Page 63: ...62 F W TANK AQUA REEL TANK 125 GAL P 1...
Page 64: ...63 F W TANK AQUA REEL TANK 125 GAL P 2...
Page 75: ...74 CLEANCO COMPACT ELECTRIC WIRING P 1...
Page 76: ...75 CLEANCO COMPACT ELECTRIC WIRING P 2...
Page 77: ...76...
Page 78: ...77...
Page 79: ...78...
Page 80: ...79...
Page 81: ...80...
Page 82: ...81...
Page 83: ...82...
Page 84: ...83...